Understanding Peristaltic Pumps with Flow Control
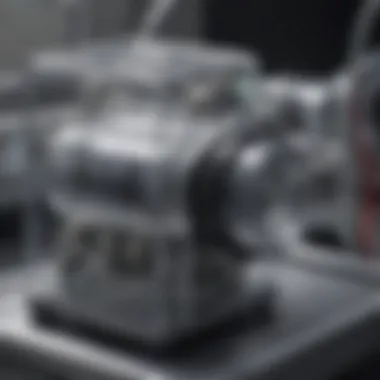
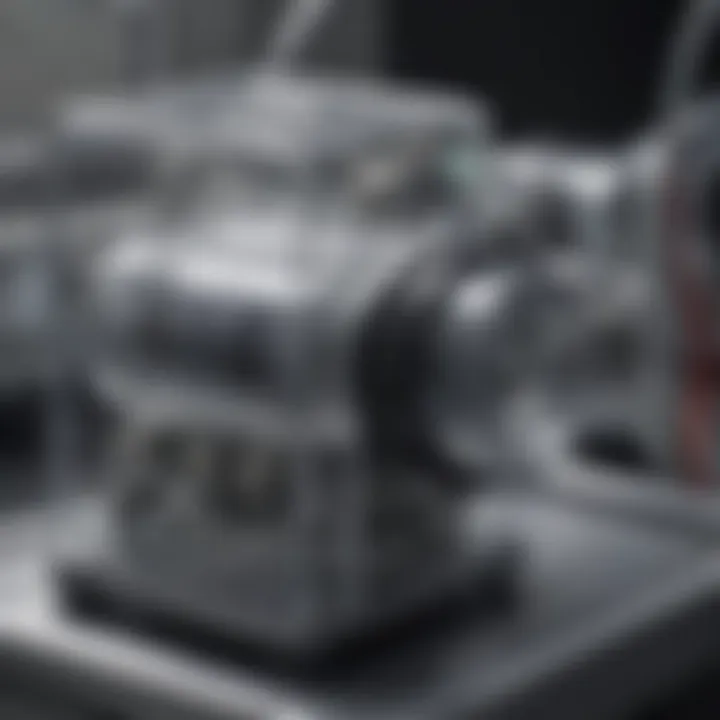
Intro
Peristaltic pumps are a crucial component in many industries due to their unique mode of operation. They function by using a series of rollers or shoes to compress a flexible tube, creating a pressure differential that moves fluid. This setup not only allows for the consistent flow of materials but also provides distinct advantages in scenarios where precise flow control is necessary.
Today, the integration of flow control technologies into peristaltic pumps enhances their overall efficiency. This article will explore how these systems operate, their specific applications across various sectors, and the technology enabling more accurate flow regulation.
Prelude to Peristaltic Pumps
Peristaltic pumps are a unique type of positive displacement pump that plays a crucial role in various industries, particularly where fluid handling and flow control are essential. Understanding the basics of these pumps helps professionals make informed decisions regarding their applications. This section will break down the fundamental concepts related to peristaltic pumps, revealing why they are significant in industrial settings.
Definition and Concept
Peristaltic pumps operate based on a simple yet effective principle: they move fluids through a system by compressing and relaxing flexible tubing. This mechanism is made possible by a series of rotating rollers or shoes that pinch the tube. The positive displacement aspect allows for accurate flow control, making these pumps favored in situations demanding precision.
The definition of peristaltic pumps is straightforward. A peristaltic pump consists of a motorized system that rotates a set of rollers along a tube, allowing for the movement of liquids without direct contact with the pump mechanism. This design minimizes contamination risks, making these pumps ideal for sensitive applications like pharmaceuticals and food processing.
Basic Operating Principles
Understanding the basic operating principles of peristaltic pumps can greatly assist in appreciating their functionality. When the rollers move, they compress the tube, creating a vacuum that draws fluid into the tubing. As the roller continues its rotation, the fluid is pushed forward, resulting in a continuous flow. This action can be illustrated through the following points:
- Suction: When the roller pinches the tube, it creates a vacuum that pulls fluid in.
- Flow: The fluid is then propelled forward continuously as more rollers move along the tube.
- Return to Original State: After the roller passes, the tubing returns to its original shape, ready for the next cycle.
It is important to note that flow rates can be easily adjusted by changing the roller speed, providing significant flexibility in operation. The peristaltic pump design allows various fluid types—viscous, shear-sensitive, or even abrasive— to be pumped without damage to the fluid or contamination of the pumping system.
"The unique design of peristaltic pumps makes them suitable for applications where contamination needs to be avoided and precision is paramount."
With these foundational understandings, readers can now delve deeper into the specific applications of flow control in peristaltic pumps, the advantages they offer, and their roles in modern industries.
Flow Control in Peristaltic Pumps
Flow control in peristaltic pumps is a crucial aspect that enhances the efficiency and precision of fluid transfer. The pumps' inherent design makes them suitable for a wide range of applications, yet controlling their flow is essential to meet specific requirements. Flow control allows operators to manage both the speed and volume of fluid being pumped, ensuring accurate dosing, consistent flow rates, and minimizing waste. Understanding flow control mechanisms can lead to significant improvements in various sectors, from pharmaceuticals to food processing.
Importance of Flow Control
The significance of flow control cannot be overemphasized in applications where precision is vital. In medical settings, for instance, delivering accurate dosages of medications can be a matter of life and death. Flow control systems help in achieving this accuracy, making peristaltic pumps indispensable in such scenarios.
In industries such as food and beverage, maintaining the right flow rate is important for both safety and quality standards. Unexpected flow variations can lead to contamination or spoilage, impacting product integrity. Thus, effective flow control is instrumental in ensuring that the product meets regulatory and safety standards. Overall, proper flow management confirms that peristaltic pumps function optimally across many sectors.
Mechanisms of Flow Control
Flow control in peristaltic pumps can be achieved through various mechanisms, each contributing to the goal of precision and functionality. Understanding these mechanisms can provide insights into their relevance and application.
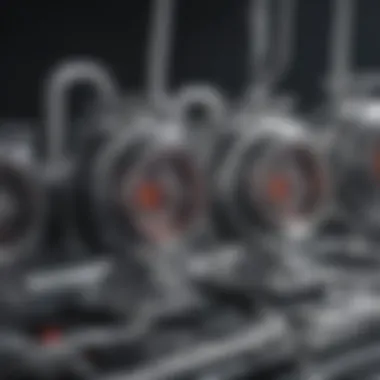
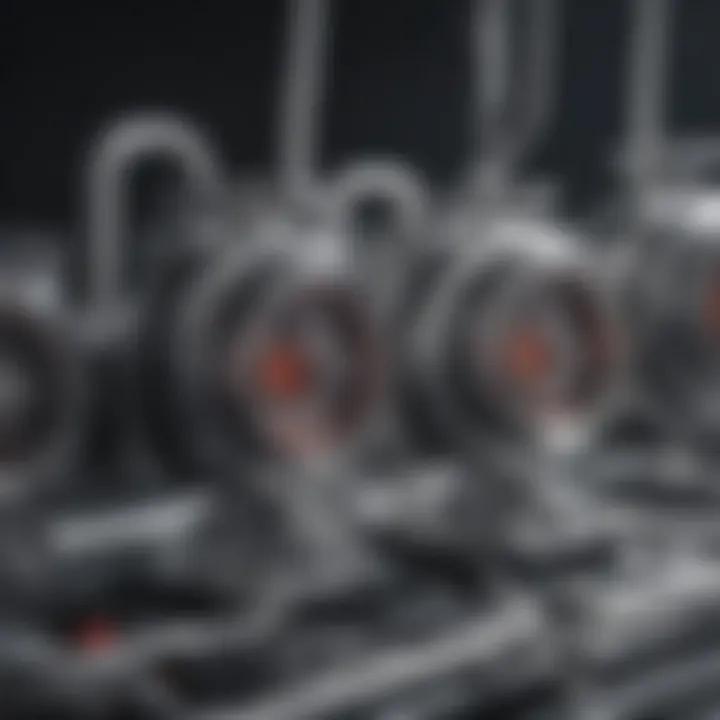
Adjustable speed settings
Adjustable speed settings represent a fundamental aspect of flow control in peristaltic pumps. By allowing operators to change the pumping speed, these settings can directly influence the rate at which fluid is delivered. This feature is particularly beneficial in environments where the properties of the fluid change frequently, requiring rapid adjustments to achieve consistent flow.
The primary characteristic of adjustable speed settings is their ability to accommodate varying process demands without needing to switch out components. This is economically beneficial, as it reduces downtime and enhances workflow fluidity. One unique advantage is the customization that it provides; users can tailor the pumping process to their specific needs, improving overall output quality. However, maintaining accuracy at very low speeds may pose challenges, requiring careful calibration.
Sensor integration
Sensor integration is another critical factor that enhances flow control in peristaltic pumps. Sensors monitor various parameters such as flow rate and pressure, relaying real-time feedback to the control system. This capability allows for swift adjustments to be made based on current operational conditions.
A key characteristic of sensor integration is the enhancement of automation within pumping systems. It enables the flow to be adjusted dynamically, reducing the risk of human error and increasing efficiency. The unique benefit is the ability to implement predictive maintenance; data gathered from sensors can predict potential problems before they escalate. However, sensor failures can lead to unexpected disruptions, necessitating regular maintenance checks to ensure functionality.
Feedback loops
Feedback loops form a sophisticated mechanism for flow control, allowing systems to self-regulate based on the output they produce. When integrated into peristaltic pumps, these loops help maintain the desired flow rates by adjusting performance in real-time.
The main characteristic of feedback loops is their reliance on continuous data analysis and adjustment. This is particularly valuable for processes that demand high precision, as minute fluctuations can be accounted for instantly. It promotes a level of consistency that is hard to achieve through manual monitoring. On the downside, the complexity of these systems may increase the need for technical expertise, which could elevate operational costs.
Effective flow control in peristaltic pumps is vital for optimizing performance across various industries, enabling accurate delivery and minimizing waste.
In summary, flow control in peristaltic pumps consists of essential features like adjustable speed settings, sensor integration, and feedback loops. Each mechanism contributes to precise fluid handling and operational efficiency, ensuring that peristaltic pumps meet the diverse needs of industries today.
Advantages of Peristaltic Pumps
Peristaltic pumps offer distinct advantages that are crucial in various applications. These pumps are notable for their design, which contributes to efficient fluid handling. Their operational features make them valuable in different industries, highlighting their growing importance in modern fluid dynamics. Here, we detail some key benefits that demonstrate why peristaltic pumps are often a preferred choice over traditional pumping methods.
Gentle Handling of Fluids
One of the most significant advantages of peristaltic pumps is their ability to handle sensitive fluids gently. This feature is especially important when pumping materials that can be adversely affected by high shear stress or turbulence.
In a peristaltic pump, the material being pumped is contained within a flexible tube. As the pump operates, rollers compress the tube, moving the fluid along in a controlled manner. This action minimizes turbulence and preserves the integrity of fragile materials, making these pumps suitable for medical and pharmaceutical applications.
- Ideal for delicate substances: Products such as cell cultures, blood, and other biologics require careful handling, and peristaltic pumps excel in this regard.
- Maintains fluid quality: Because of the low shear, the quality and characteristics of the fluid remain intact throughout the pumping process, reducing the risk of chemical alteration.
Reduced Risk of Contamination
Another compelling advantage of peristaltic pumps is their reduced risk of contamination. In many industrial settings, keeping the fluid free from external pollutants is paramount.
The design of peristaltic pumps ensures that the fluid only comes into contact with the tubing. The pump's mechanism isolates the pumped material from moving parts, which helps prevent contamination from the environment. This is especially critical in the food and beverage sector, where hygienic standards are strict. Peristaltic pumps are easy to clean and can be sterilized, further ensuring product integrity.
"Peristaltic pumps provide a closed system that minimizes exposure to environmental contaminants, making them ideal for sensitive applications."
Versatility in Pumping Various Fluids
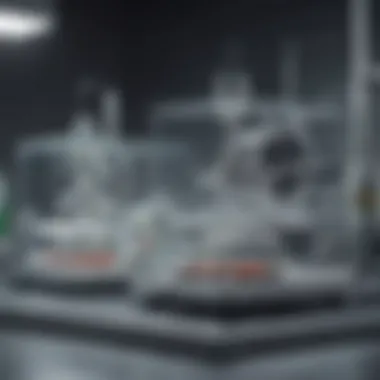
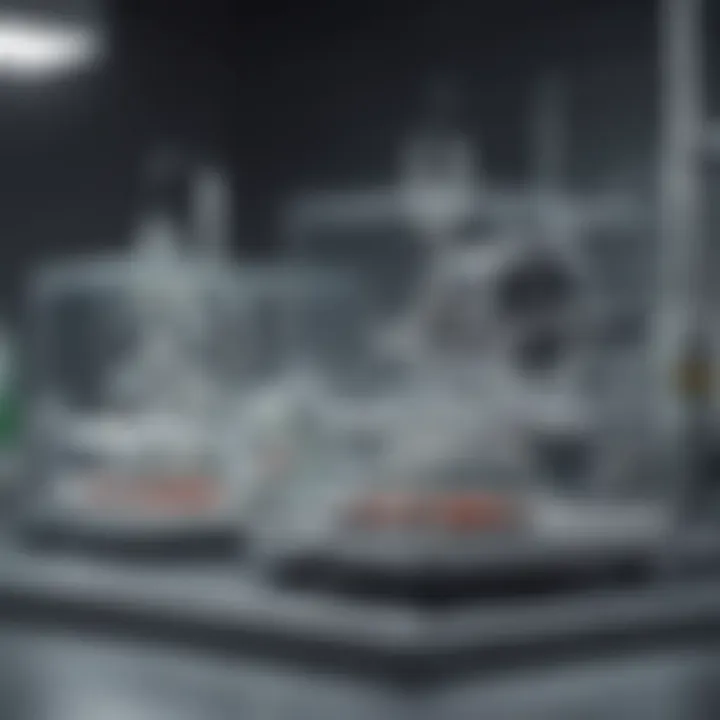
Peristaltic pumps are versatile, capable of handling a wide range of fluids, from thin liquids to highly viscous materials. This flexibility makes them suitable for diverse industries.
- Adaptability: Whether it involves shear-sensitive fluids, slurries, or even abrasive substances, peristaltic pumps can be engineered to meet specific requirements. Their adaptability allows for easy switching between different fluid types without significant modification.
- Customizable: By altering the tubing material and size, operators can fine-tune the pump for particular applications, enhancing overall efficiency and effectiveness.
In summary, peristaltic pumps provide several advantages that are aligned with the requirements of modern fluid handling across industries. Their gentle handling, contamination reduction, and versatility play pivotal roles in ensuring that the pumping process is efficient and safe.
Applications in Different Industries
Peristaltic pumps with flow control play a significant role across various sectors. They offer precise fluid handling capabilities that are essential in both medical and industrial applications. Their unique design enables them to handle different fluids without risk of contamination, making them ideal for sensitive processes. Understanding how these pumps are used in different industries sheds light on their versatility and functionality.
Medical and Pharmaceutical Applications
In the medical field, peristaltic pumps are vital for precise fluid delivery. They are widely used in the administration of medications, blood transfusions, and feeding applications. One notable benefit is the gentle handling of liquids, especially delicate biological materials. The capability to control flow rates allows healthcare professionals to tailor dosages to patient needs. Moreover, the closed system of a peristaltic pump ensures that there is no exposure to the external environment, thereby reducing the risk of contamination. This is particularly important in pharmaceutical manufacturing where maintaining sterile conditions is critical.
Food and Beverage Industry
The food and beverage sector relies heavily on peristaltic pumps due to their hygienic handling of sensitive products. These pumps are effective in managing ingredients such as sauces, syrups, and dairy products. One of the key advantages is that they minimize shear stress on the products while maintaining the necessary flow rate. This is crucial for preserving the quality and integrity of food items. Besides, easy cleaning and maintenance align with food safety standards, making these pumps a popular choice in food processing plants. Manufacturers appreciate the pumps’ ability to work with varying viscosities and product types, ensuring flexibility in production lines.
Chemical Processing
In the realm of chemical processing, peristaltic pumps are indispensable for their reliable performance with aggressive substances. These pumps handle corrosive chemicals, slurries, and viscous fluids with ease. The ability to control the flow rate precisely is vital in processes like mixing, dosing, and transferring materials. Furthermore, peristaltic pumps offer a one-way fluid movement, reducing risks of backflow that can lead to contamination in sensitive applications. Many industries benefit from their efficiency and low maintenance costs, contributing significantly to operational productivity.
In summary, the applications of peristaltic pumps are diverse and impactful across various industries, highlighting their adaptability and importance in modern fluid dynamics.
The understanding of these applications prepares students, educators, and professionals to appreciate the complexities involved in using peristaltic pumps in real-world scenarios.
Challenges in Using Peristaltic Pumps
Understanding the challenges associated with peristaltic pumps is crucial for anyone involved in their application or study. These pumps, while effective, do have certain limitations that can impact performance and overall efficiency.
The two main issues to consider are wear and tear of tubing and flow rate limitations. Each aspect contributes to operational costs and the need for regular maintenance. Addressing these challenges allows for better design and implementation strategies, which ultimately benefits the industries that utilize these pumps.
Wear and Tear of Tubing
Tubing is a fundamental component of peristaltic pumps. As the pump operates, the tubing experiences repeated flexing and compression as rollers compress the tube to move the fluid. Over time, this leads to material fatigue. Signs of wear may include cracks, brittleness, or color changes in the tubing material.
Factors affecting tubing wear include:
- Material quality: High-quality tubing is less likely to degrade quickly. Using FDA-approved materials may be necessary in medical and food applications.
- Fluid characteristics: The nature of the fluid being pumped can impact tubing lifespan. Abrasive, corrosive, or highly viscous fluids tend to create more wear.
- Operating conditions: Temperature and pressure can also affect the durability of the tubing. Higher temperatures can cause softening, whereas higher pressures may lead to premature failure.
Regular inspection and timely replacement of tubing are essential to maintain pump performance and avoid unexpected downtimes.
Flow Rate Limitations
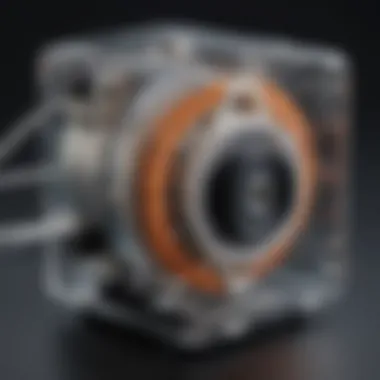
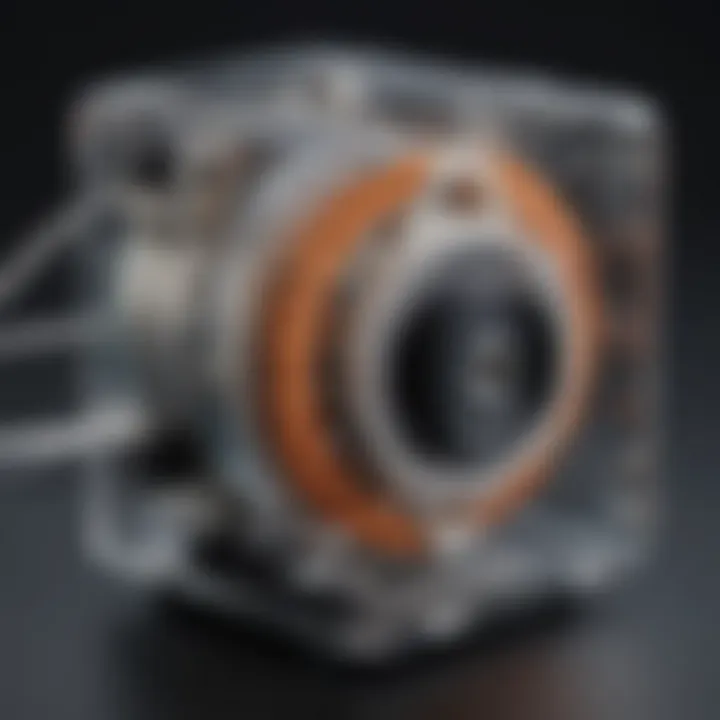
Flow rate is an essential aspect of any pumping system. Peristaltic pumps are generally best suited for low to medium flow applications. Unlike centrifugal or gear pumps, their flow rates are limited due to the mechanical nature of operation. Factors influencing flow rate include:
- Size of the tubing: Larger diameter tubing allows for higher flow rates. However, oversizing can lead to inefficiencies and more wear.
- Pumping speed: The rate at which the rollers rotate directly impacts flow. In most cases, increasing speed improves flow rate but can lead to noise and vibrations, ultimately affecting longevity.
- Pressure limits: Higher pressure settings can restrict flow for certain fluids, particularly if the tubing material is not designed for such conditions.
"Understanding these limitations is vital for enhancing peristaltic pump design and functionality in industrial applications."
Careful consideration of these factors during the design and operational phases will lead to improved efficiency and reliability in systems using peristaltic pumps.
Future Trends in Peristaltic Pump Technology
As industries evolve, so does the technology that supports them. The future trends in peristaltic pump technology play a crucial role in enhancing the functionality and efficiency of these systems. With the introduction of advanced features, such as smart technologies and sustainability measures, these pumps are set to become more efficient and reliable. This forward-looking approach is vital not only for meeting current demands but also for anticipating future challenges in fluid management.
Integration with Smart Technologies
The convergence of peristaltic pumps with smart technologies marks a significant advancement in fluid handling. This integration allows for real-time monitoring, diagnostics, and control, which enhances the operational precision of pumping systems. Smart technologies can include IoT sensors that provide valuable data on flow rates, pressure, and tubing conditions. Such insights enable operators to optimize performance and mitigate potential issues before they escalate.
A primary benefit of this smart integration is the capability for predictive maintenance. By analyzing data patterns, it is possible to forecast when maintenance is needed, reducing downtime and costly repairs. Moreover, connectivity allows for remote operation and management, improving the responsiveness of operators to changing conditions.
In summary, integrating smart technologies into peristaltic pumps leads to increased efficiency, reduced operational costs, and enhanced reliability, catering to the demands of modern industries.
Sustainable Materials and Practices
Sustainability is becoming increasingly important in all areas of manufacturing and industrial processes. Peristaltic pumps are no exception. The development of sustainable materials and practices signifies a commitment to minimizing environmental impact while ensuring operational efficiency. The use of biodegradable and recyclable materials in pump components can significantly reduce waste.
Furthermore, adopting practices that promote energy efficiency adds another layer of sustainability. For example, pumps designed with energy-saving technologies can operate under lower power requirements, contributing to decreased energy consumption. This shift not only meets regulatory standards but also appeals to eco-conscious consumers and businesses.
Implementing sustainable methods in the production and operation of peristaltic pumps establishes a responsible approach to industrial practices. This evolution resonates with the broader trend of prioritizing environmental health in all sectors.
The commitment to sustainability in peristaltic pump technology reflects a necessary evolution within industries, addressing both efficiency and environmental responsibilities.
Finale
In this final section, we will encapsulate the insights and discussions surrounding peristaltic pumps enhanced with flow control mechanisms. Understanding these pumps is essential due to their unique operational principles and increasing application across various sectors. They offer significant benefits like gentle fluid handling and reduced contamination risk. However, key considerations must be addressed when implementing these systems.
Summarizing Key Insights
Throughout our exploration, we identified several critical aspects about peristaltic pumps:
- Operational Principles: The mechanism operates by compressing flexible tubing, creating a smooth flow characteristic.
- Flow Control Importance: Precise flow regulation is vital in many industries, as it dictates how substances are handled.
- Technological Integration: Advances in smart technologies and sustainable materials shape the future landscape of these pumps.
- Industry Applications: The pumps have found relevance in medical, food, and chemical processing sectors.
This concise summary underlines the relevance of peristaltic pumps and flow control. Their functionality not only meets but also often exceeds the varying demands of different industries.
The Future of Peristaltic Pumps in Industry
Looking ahead, the trajectory of peristaltic pumps indicates several exciting developments:
- Smart Technologies: Integration of IoT and automation will enhance data analysis. This allows operators to respond to system changes in real-time, improving operational efficiency.
- Sustainability Focus: There is a growing emphasis on using eco-friendly materials. This trend not only addresses environmental concerns but also drives innovation in design and functionality.
- Adaptability: As industries evolve, there will be an increasing need for versatile pumping solutions. Peristaltic pumps are well-positioned to adapt to these changing needs, thanks to their inherent flexibility.
The ongoing developments in peristaltic pump technology underscore their crucial role in the respective fields they serve. Their ability to adapt and improve with advancements in technology will likely continue well into the future.