Comprehensive Overview of Surface Roughness Measurement Techniques
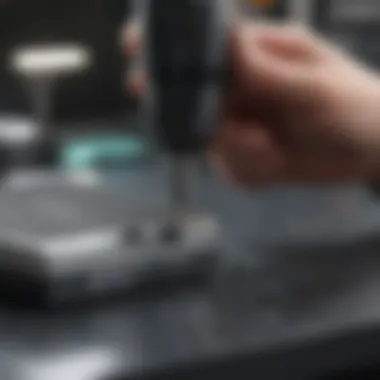
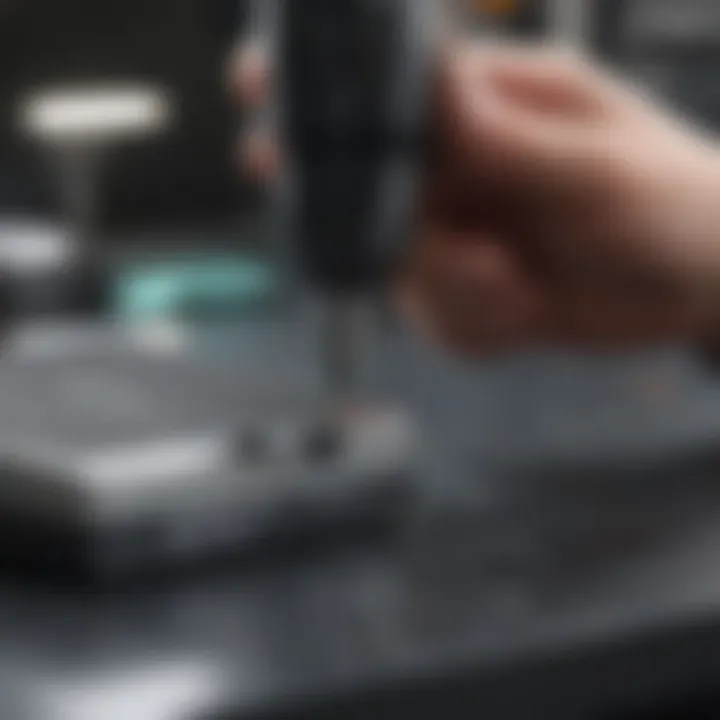
Intro
Surface roughness is a crucial parameter in many industries, including manufacturing, materials science, and engineering. It can significantly influence the performance and durability of products. As such, measuring surface roughness accurately is essential. This need has led to various techniques being developed over time, each suited for different applications. The evolution of these techniques reflects advancements in technology and our understanding of material properties.
The following sections will delve into the various methods for measuring surface roughness, from traditional to modern non-contact techniques. This comprehensive guide will explore their principles, advantages, and limitations, providing valuable insights for those engaged in this area of research and application.
Overview of Research Topic
Brief Background and Context
Surface roughness refers to the texture of a surface, which can have profound effects on friction, wear, and adhesion. Historically, surface quality has been assessed through manual techniques, but with the growth of industries and the complexity of materials, precise measurement has become more vital. Various industries now rely on sophisticated instruments to ensure high standards of surface quality. The methods have evolved from basic tactile measurements to intricate optical and electronic devices.
Importance in Current Scientific Landscape
In today's scientific landscape, accurate surface roughness measurement plays a fundamental role in developing new materials and products. Industries such as aerospace, automotive, and electronics depend on these measurements to enhance performance and reliability. Developing techniques continue to advance alongside industry needs, making it essential for experts to stay informed about the latest methods.
Methodology
Research Design and Approach
This article employs a review-based research design. It synthesizes existing literature, guidelines, and best practices in surface roughness measurement. The approach includes careful examination of both historical and contemporary measurement techniques and their applicability.
Data Collection Techniques
Data is gathered from multiple sources, including academic journals, industry reports, and reliable databases. This ensures that the information presented is comprehensive and relevant.
"Accurate measurement techniques not only enhance product quality but also reduce operational costs and improve safety across various engineering domains."
It is vital for professionals in the field to understand the nuances of these measurement techniques to apply them effectively in their work. This article aims to serve as a comprehensive resource for the diverse audience of students, researchers, educators, and industry professionals.
Foreword to Surface Roughness Measurement
Surface roughness measurement is an essential topic that plays a pivotal role in numerous fields that rely on surface quality. Understanding the characteristics of surface roughness is vital in areas such as manufacturing, aerospace, and materials science. The measurement techniques not only affect the quality and performance of products but also influence their reliability and lifespan. Precise measurements help engineers and researchers make informed decisions about design, processing, and quality control.
Surface roughness is defined as the texture of a surface, influenced by the manufacturing process and material properties. Variability in surface roughness can lead to significant implications in product functionality. For instance, in mechanical components, a rough surface might lead to increased friction, wear, and ultimately failure. Thus, having effective measurement techniques is paramount for ensuring that components meet specific standards.
By exploring various measurement techniques, this article aims to enhance understanding and provide guidance for selecting the appropriate methods based on specific applications. As technology advances, new methods continue to emerge, further complicating the decision-making process. Solid understanding of traditional and innovative techniques will aid professionals in optimizing surface quality assessments.
Fundamental Concepts in Surface Roughness Measurement
Understanding the fundamental concepts in surface roughness measurement is crucial for anyone involved in quality control, manufacturing, or research. Surface roughness directly affects the performance attributes of materials, including friction, wear, and the fit between parts. Each measurement technique offers different insights depending on material type and application requirements. Knowing various parameters helps in selecting the right approach, ensuring accurate evaluations.
Parameters of Surface Roughness
Different parameters exist to quantify surface roughness. These parameters convey unique aspects of the surface texture, providing insights into performance and functionality.
Ra - Arithmetic Average Roughness
Ra, or Arithmetic Average Roughness, is one of the most commonly used parameters. It averages the absolute values of all surface height deviations measured over a specified length. This simplicity makes Ra a beneficial choice in industries where quick assessments are necessary, such as automotive and manufacturing.
The unique feature of Ra is its ability to provide an overall glimpse of surface roughness. However, it does not capture the entire intricacies of the surface profile, which can misrepresent actual conditions.
Advantages of Ra include its straightforward computation and widespread acceptance. Nevertheless, it lacks the sensitivity to peak and valley characteristics compared to other measures.
Rz - Average Maximum Height of the Profile
Rz measures the average of the maximum peak-to-valley height over a specified sampling length. It is beneficial when locating features like valleys and peaks that are critical to performance. Rz is often favored in specific contexts, such as engineering or material science, where surface texture features significantly influence material behaviors.
The principal advantage of Rz is that it provides a more comprehensive measure of extreme deviations than Ra. This parameter gives insights pertinent to load-bearing applications, where surface integrity is vital.
However, the drawback may lie in its potential to overlook smaller roughness details, which can matter in precision applications.
Rms - Root Mean Square Roughness
Rms, or Root Mean Square Roughness, calculates the square root of the average of the squares of the height deviations. This parameter offers a nuanced view of surface roughness. It accounts for peaks and valleys but does so with greater sensitivity. Researchers and engineers often prefer Rms due to its statistical relevance in surface analysis.
A unique feature of Rms lies in its ability to give a different perspective on surface irregularities by emphasizing larger deviations during calculations. The advantage of this approach is its robustness against random errors in measurement. However, its complexity may require more data processing, which could be a limitation if resources are constrained.
Effects of Surface Roughness on Material Performance
Surface roughness plays a significant role in how materials perform under various conditions. Rough surfaces can increase friction, leading to higher wear rates. In contrast, smoother surfaces may benefit lubrication and reduce wear.
"The impact of surface roughness extends across multiple domains, influencing product life cycles and operational efficiency."
Additionally, certain applications may require specific roughness parameters to ensure proper adhesion in coatings or bonding. For instance, in aerospace, where friction and drag are critical, optimized surface profiles can greatly enhance performance.
Traditional Contact-Based Measurement Techniques
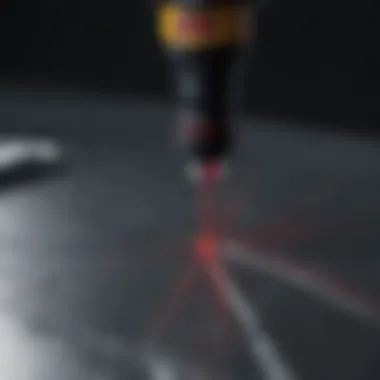
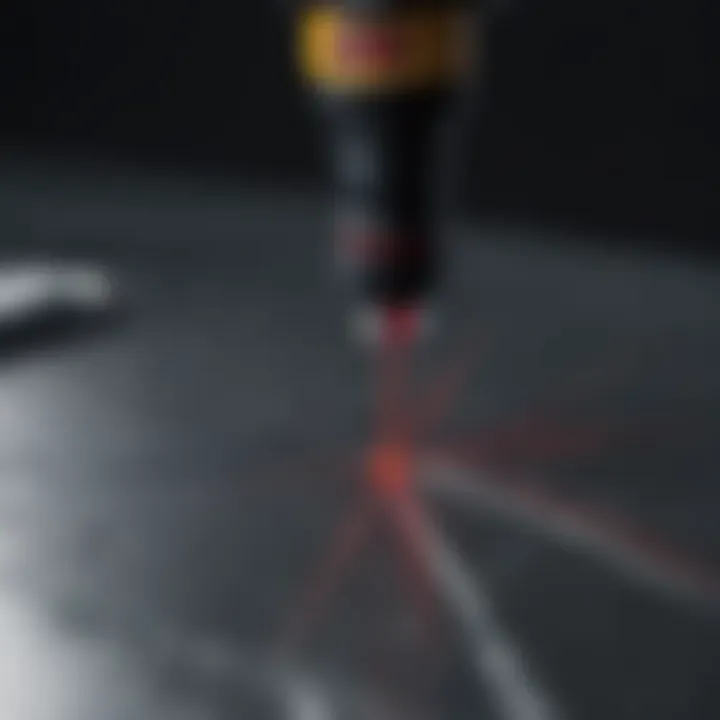
Traditional contact-based measurement techniques play a crucial role in surface roughness measurement. These methods involve physical contact between a stylus or probe and the surface being evaluated. They provide reliable and precise data, essential for ensuring product quality and functionality across multiple industries. Understanding these techniques helps researchers and professionals select the appropriate method for their specific applications, which can ultimately influence material performance.
Stylus Profilometry
Operating Principle
Stylus profilometry is one of the most widely used techniques for measuring surface roughness. The operating principle of this method involves dragging a fine stylus across the surface. As the stylus makes contact, it moves vertically in response to the surface's topography. The vertical displacement is then recorded and used to generate a profile of the surface.
A key characteristic of stylus profilometry is its ability to deliver detailed information about the surface's microtopography. This feature makes it a beneficial choice for diverse applications, from manufacturing to research. However, the method may be limited by stylus tip wear, impacting measurement accuracy. This aspect should always be considered when selecting profiling techniques for sensitive applications.
Advantages and Disadvantages
Stylus profilometry offers significant advantages, such as high accuracy and the ability to measure a wide range of surfaces. Its precision makes it a popular method among professionals who need consistent results, especially in quality control settings. However, the contact nature of the technique carries certain disadvantages. For example, the stylus can be disturbed by surface irregularities, leading to potential measurement errors.
Additionally, stylus methods may not be suitable for very soft materials due to the potential for damage during measurement. Thus, it's essential to weigh these factors when considering stylus profilometry for specific applications.
Contact Probe Methods
Measurement Techniques
Contact probe methods serve as another traditional contact-based technique for assessing surface roughness. These methods usually involve various types of probes that physically touch the surface and measure roughness parameters. Key among these techniques is the use of mechanical probes, which are versatile and can be adapted to measure different surface types and conditions.
One of the reasons these measurement techniques are prevalent is their ease of use and straightforward operation. However, the contact nature of these techniques also presents challenges, such as surface damage and limitations on sensitive materials. It is important for users to be mindful of these potential issues when selecting measurement approaches.
Calibration Procedures
Calibration procedures are essential for ensuring the accuracy of contact probe methods. Proper calibration involves establishing a reference standard against which measurements can be compared. This process typically requires specific calibration tools and adherence to standard protocols.
A significant aspect of calibration is its consititution in maintaining measurement integrity over time. Regular calibration ensures that any inherent errors are minimized, thus delivering reliable data. Nonetheless, calibration processes can be time-consuming and may require additional training for personnel. These considerations are important to factor in during the planning phases of implementing contact probe methods for surface roughness measurement.
Non-Contact Surface Measurement Methods
Non-contact surface measurement methods have gained prominence due to their ability to assess surface roughness without physical interaction with the sample. This is particularly important in preserving the integrity of delicate surfaces or soft materials. These methods utilize various principles, including optical and laser technologies, which provide precise measurements without the risks of wear or damage. By employing non-contact methods, industries can achieve greater efficiency, reduce machine downtime, and improve the accuracy of surface analysis. The ability to analyze samples in real-time also enhances decision-making processes in quality control.
Optical Profilometry
Optical profilometry stands at the forefront of non-contact measurement techniques, using light to map surface profiles with high resolution.
Interferometry
Interferometry is a technique that analyzes the interference patterns generated by light waves reflecting off a surface. This method is noted for its sensitivity and ability to provide measuring capabilities in the nanometer range. One key characteristic of interferometry is its capability to produce highly detailed three-dimensional surface maps. This has made it a beneficial choice for researchers and industries looking for precision measurements.
The unique feature of interferometry is its ability to work with various wavelengths of light, allowing for adaptability to different materials. While this is advantageous, some disadvantages include the complexity of setup and potential environmental factors like vibrations affecting accuracy.
Confocal Microscopy
Confocal microscopy employs focused laser beams to generate high-resolution images by capturing multiple slices of a sample. This method is integral in providing detailed surface information in a non-invasive manner. Confocal microscopy is distinguished by its ability to eliminate out-of-focus light, leading to sharper images compared to conventional microscopy techniques. This quality underscores its popularity in fields like materials science and biology.
A unique aspect of confocal microscopy lies in its versatility, allowing for both surface topography and subsurface analysis without sample preparation. However, one must consider its limited depth of field, which can complicate the analysis of very rough surfaces or features that vary greatly in height.
Laser Scanning Techniques
Laser scanning techniques utilize focused laser beams to scan the surface and measure height variations precisely. The technology is not only quick but also provides dense data sets essential for advanced analysis.
Principle of Operation
The principle of operation in laser scanning involves directing a laser beam onto the surface, which reflects back to sensors. This method captures real-time data, providing high-resolution topographical maps. A primary advantage of this technique is its speed; it can rapidly process large samples. This efficiency makes laser scanning a popular choice for industries with high throughput needs.
However, the unique feature of laser scanning is its adaptability; it can be used on various surfaces, including rough and uneven materials. Nonetheless, one must be mindful of limitations regarding reflective surfaces, which might lead to erroneous readings due to inadequate laser reflection.
Applications in Industry
Applications in industry are vast for laser scanning techniques, ranging from automotive to aerospace and even architecture. The ability to create detailed surface models assists in engineering and design processes.
The key feature of these applications is their contribution to automation and quality control, which enhance production efficiency. Industries benefit from the rapid prototyping capabilities that laser scanning provides, translating to faster product development cycles.
While its advantages are clear, challenges persist, such as equipment costs and requirements for skilled operators to interpret the data properly.
"Non-contact measurement techniques not only streamline production but also preserve the quality of the materials analyzed."
In sum, non-contact surface measurement methods present a valuable alternative to traditional techniques. By understanding their principles and applications, users can choose the best methods for their specific needs.
Emerging Technologies in Surface Roughness Measurement
Emerging technologies in surface roughness measurement are revolutionizing assessment methods in various industries. These advancements enhance the accuracy and efficiency of measurements. With market demand for precision increasing, adopting new techniques is crucial. Innovations such as 3D measurement and applications of machine learning represent significant strides forward. Each method addresses previous limitations observed in traditional techniques.
3D Surface Measurement Techniques
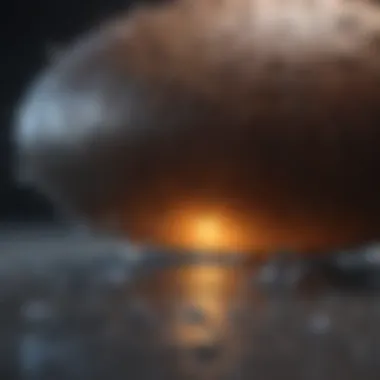
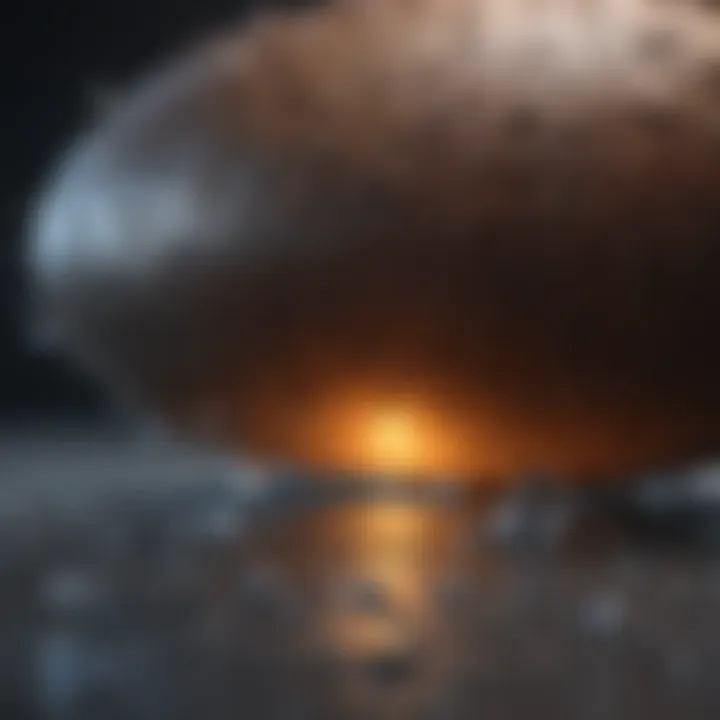
Principles of 3D Measurement
3D surface measurement techniques are based on the principle of analyzing surfaces in three dimensions rather than two. This multidimensional approach allows for a comprehensive evaluation of surface features. Key characteristics include the ability to capture intricate details that are not visible in flat assessments. Such precision makes these techniques highly beneficial in sectors like manufacturing and aerospace. On the other hand, this technology requires substantial computational power, which may limit accessibility for some users.
Software for Data Analysis
The software for data analysis is intrinsic to the effectiveness of 3D surface measurement. It processes complex datasets generated by the measurement tools, translating raw data into understandable formats. The key characteristic of such software is its ability to perform sophisticated algorithms, which optimize data interpretation. It is a popular choice because it enables real-time analysis, fostering faster decision-making. Yet, the challenge lies in the learning curve associated with such advanced tools, which can hinder new users.
Impact of Machine Learning on Measurement Techniques
Machine learning is significantly altering surface roughness measurement techniques. This technology uses algorithms to interpret data, improving accuracy through pattern recognition and predictive analysis. As machine learning systems learn from data inputs, their performance improves over time. In this context, its integration with measurement tools enables smarter analyses that can adapt to varying conditions. However, reliance on technology raises concerns about data privacy and system errors that need careful management.
Selecting the Right Measurement Technique
Selecting an appropriate surface roughness measurement technique is critical for achieving reliable results. The choice of technique influences the accuracy and effectiveness of surface assessments. Different techniques serve various purposes, and their selection depends on multiple factors, including the specific nature of the surface and the precision required. This article examines the primary factors influencing these choices.
Factors Influencing Technique Choice
Surface Type
Surface type plays a significant role in the selection process for measurement techniques. Each surface type, whether it is metallic, polymeric, or ceramic, has distinct characteristics that affect how roughness is assessed. For instance, metallic surfaces might require different approaches compared to softer materials like plastics. The key characteristic of surface type is its texture—smooth surfaces may not require intricate analyses, while rough surfaces need precise methods to capture variations effectively.
One beneficial aspect of considering surface type is the ability to achieve reliable measurements tailored to that specific surface. A unique feature of rough surfaces is their propensity for increased friction and wear, making their accurate measurement essential in fields like manufacturing and material science. However, one disadvantage could be the additional costs associated with advanced techniques required for certain surfaces like ceramics, which may not be necessary for metals.
Required Accuracy
Required accuracy is another crucial aspect that influences the selection of measurement techniques. The need for precise data often dictates the choice of method. In applications such as aerospace and medical devices, higher accuracy is non-negotiable due to safety and performance standards.
A key characteristic of required accuracy is the measurement tolerance; how much deviation from a standard is acceptable. High accuracy metrics assure stakeholders that surfaces meet defined criteria. A unique feature of high-accuracy techniques is their use in controlled environments, ensuring minimal interference during measurement. This can lead to more reliable data. However, using techniques that require such high precision often entails higher costs and extended time for setup and analysis, which can be seen as a challenge in fast-paced industries.
Comparative Analysis of Techniques
To comprehensively understand the right measurement technique, a comparative analysis is necessary. Different methods offer unique advantages and disadvantages in how they assess surface roughness. This analysis can often reveal unexpected insights. For example, traditional contact methods yield high accuracy but might not be suitable for soft or delicate surfaces due to potential damage. In contrast, non-contact methods like optical profiling offer versatility and ease of use but might lack the same level of accuracy.
Factors like cost, setup time, and required maintenance also play significant roles in this assessment. By analyzing how each technique addresses key factors, informed decisions can be made. Ultimately, the successful measurement of surface roughness hinges on recognizing the balance between the method's capabilities and the specific requirements of the task.
Standardization and Compliance in Surface Measurement
Standardization and compliance in surface measurement are not merely administrative necessities; they are integral to ensuring reliability and consistency in surface roughness assessments. The complexity of modern manufacturing and scientific research demands precise measurements that adhere to established standards. These standards serve as a backbone for comparability across different labs, industries, and research studies. When measurements are standardized, stakeholders can trust that a roughness value reported by one party can be understood and utilized by another without ambiguity.
Standardization is crucial for a variety of reasons. First, it enhances reproducibility. When researchers and engineers follow the same measurement protocols, the data produced can be replicated reliably. This is essential in both academic settings—where experiments need verification—and in industry, where quality control is vital. Moreover, standardized methods facilitate communication among professionals. They create a common language for describing surface characteristics, which is necessary for interdisciplinary collaboration and communication of results.
Benefits of Standardization:
- Enhances Reproducibility: Reliability and consistency across studies and applications.
- Improves Communication: Standardized reporting makes it easier to share findings among researchers and practitioners.
- Ensures Compliance: Aligns measurement techniques with industry regulations and requirements.
While standardization is essential, compliance also plays a critical role. Compliance involves adhering to established standards set by governing bodies or industry groups. Following these regulations ensures that measurements are not only accurate but also accepted in legal and commercial contexts. Compliance provides assurances that products meet required safety and performance criteria, which is particularly prevalent in sectors such as aerospace and automotive industries. Regular audits and reviews are often needed to maintain compliance, establishing a culture of quality assurance and accountability.
Compliance with international standards is crucial for maintaining product safety and performance in various industries.
International Standards for Measurement
The significance of international standards in surface roughness measurement cannot be overstated. Organizations such as the International Organization for Standardization (ISO) develop widely recognized guidelines that dictate methods for measuring surface texture. These standards outline the principles behind various measurement techniques, acceptable tolerances, and reporting requirements.
For instance, ISO 4287 establishes the parameters for assessing surface roughness, including methods for calculating Ra, Rz, and other important metrics. By employing these internationally recognized standards, companies enhance the credibility of their measurement processes while ensuring their products’ compliance with global expectations. Following ISO guidelines can also reduce the risk of disputes that may arise from differing measurement methods.
Regulatory Compliance and Testing Procedures
In addition to following international standards, regulatory compliance is specific to legal and industry-related requirements. Different sectors—such as pharmaceuticals, aerospace, and automotive—have unique regulations that dictate how surfaces must be measured and what tolerances are acceptable. Organizations often need to put in place specific testing procedures to comply with these regulations.
Testing procedures may involve detailed protocols for sample preparation, measurement execution, and data analysis. Documentation of these processes is vital for auditing and validating compliance. Regular training of personnel in relevant standards and procedures ensures a workforce that upholds the importance of accuracy and adherence to regulations. Failure to comply can lead to serious repercussions, including financial penalties and compromised product safety.
In summary, the emphasis on standardization and compliance in surface roughness measurement ensures accuracy, reliability, and acceptance across various industries. By adhering to international standards and regulatory requirements, organizations can foster a culture that prioritizes measurement quality and integrity.
Applications of Surface Roughness Measurement
Understanding the applications of surface roughness measurement adds depth to its significance in various fields. The precision in measuring surface characteristics influences the performance and longevity of products across industries. With the increasing demand for high-quality goods, the scrutiny on surface roughness has intensified. Moreover, the choice of measurement technique can markedly affect the outcomes and interpretations of surface quality. This section explores its applications in three critical domains: manufacturing, aerospace, and material science.
In the Manufacturing Industry
In the manufacturing sector, surface roughness plays a crucial role in determining product quality. Various processes, such as machining, grinding, and polishing, leave distinct surface characteristics that directly correlate with tool wear, operational efficiency, and product lifecycle. Adhering to specific roughness parameters ensures that components meet the necessary functional requirements.
- Optimizing Functionality: Components such as bearings or pistons rely on precise surface roughness measurement to minimize friction, extending their working life.
- Quality Control: Manufacturers employ surface roughness measurement as part of quality assurance protocols, ensuring every item produced conforms to industry standards.
- Cost-Efficiency: By identifying roughness-related issues early, manufacturers can reduce waste and rework, driving down production costs.
Employing methods like stylus profilometry or optical techniques in this context facilitates effective monitoring and adjustment of processes, ensuring that the desired surface quality is maintained.
In the Aerospace Sector
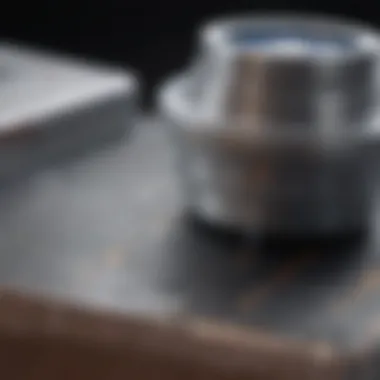
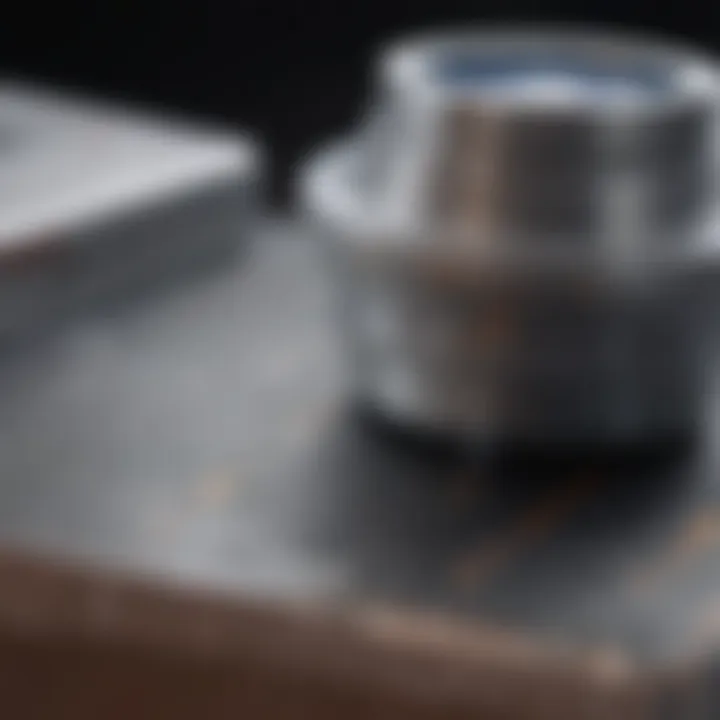
Surface roughness in the aerospace sector is integral to safety and performance. The high-stakes nature of aircraft components necessitates stringent control of surface characteristics to ensure safety and reliability during operation. Any deviations from required specifications can lead to catastrophic failures.
Key considerations include:
- Aerodynamic Efficiency: Roughness can influence airflow over aircraft surfaces. Smooth surfaces help achieve better aerodynamic properties, enhancing fuel efficiency and performance during flight.
- Weight Reduction: Materials with optimized surface roughness can lead to weight savings, as surface treatments can replace heavier components without sacrificing strength or performance.
- Surface Treatments: Aerospace components often undergo coatings and treatments that necessitate precise roughness measurements for adhesion and performance verification.
Additional techniques like laser scanning can provide a comprehensive assessment of surface uniformity, ensuring that every component works optimally.
In Material Science Research
Material science research heavily relies on surface roughness measurement as it directly impacts material properties and behaviors. Understanding how surface characteristics influence phenomena such as adhesion, friction, and wear can yield significant insights into new material applications and innovations.
Relevant aspects include:
- Interfacial Properties: Surface roughness affects how materials interact with others, influencing adhesion at micro and macro levels.
- Surface Engineering: Advances in coatings and treatments require precise roughness data to ensure the effectiveness of innovations.
- Experimental Procedures: In studying new materials, uniform and reproducible roughness is essential for conducting meaningful experiments.
Techniques such as atomic force microscopy allow researchers to analyze materials at a nanoscale, providing detailed profiles that inform material development strategies.
"A thorough understanding of surface roughness is crucial for advancing technology in manufacturing, aerospace, and material sciences."
By recognizing the diverse applications of surface roughness measurement, researchers and professionals can better appreciate its importance in achieving superior product performance and innovation.
Challenges in Surface Roughness Measurement
Surface roughness measurement is crucial for ensuring quality and performance in various industries. However, challenges persist that can affect accuracy and reliability. Understanding these challenges is essential for researchers and professionals aiming to implement effective measurement strategies.
Sources of Error in Measurements
Errors in measurements can arise from several sources. Firstly, instrument calibration is vital. If the tools used for measurement are not calibrated correctly, results can be significantly skewed. Environmental factors also play a role. Vibration, temperature fluctuations, or ambient light can impact measurement outcomes, especially in sensitive non-contact techniques.
Inadequate setup can introduce errors too. For instance, improper alignment of the measurement device can lead to inaccurate data. Measurement speed is another consideration. If it is too rapid, the device may not gather enough information for a precise reading, thus compromising the surface quality assessment. Small surface irregularities can also lead to sampling errors, particularly if the roughness features are below the resolution capabilities of the measurement device.
Limitations of Current Techniques
Current surface roughness measurement techniques have inherent limitations. Contact methods, such as stylus profilometry, can disrupt the surface being measured. This interaction may alter the roughness characteristics, particularly in softer materials. Additionally, contact methods often struggle with very small or complex geometries.
Non-contact methods, while eliminating surface damage, can be less reliable in capturing minute details. For example, optical techniques may struggle with clear readings on surfaces that are highly reflective or absorb light. Furthermore, the resolution of measurements is closely linked to the technology used. Some methods may not be able to capture fine surface details, resulting in inadequate assessments for high-precision applications.
Future Directions in Surface Roughness Measurement Research
The field of surface roughness measurement is evolving rapidly, influenced by ongoing advancements in technology and the expanding requirements of industries. As products become more complex and demanding, the precision of surface characterization becomes increasingly critical. Understanding the future directions of research in surface roughness measurement is essential for professionals and researchers aiming to stay ahead in this competitive landscape. This section explores innovative approaches, emerging technologies, and the integration of new methodologies that promise to enhance measurement accuracy and efficiency.
Innovative Approaches and Advancements
Recent years have seen significant innovations in surface roughness measurement techniques. Traditional methods are being complemented or replaced by new solutions that offer enhanced capabilities. Some key advancements include:
- Optical Techniques: The advent of advanced optical techniques such as Structured Light Scanning has proven more effective in capturing surface details. This approach allows for rapid imaging of larger surface areas, thus reducing inspection times.
- Nanotechnology: As materials enter the nanoscale domain, it becomes critical to develop measurement techniques capable of detecting very small variations in surface roughness. New methodologies are being developed to achieve measurement resolution at this scale.
- Artificial Intelligence: The integration of artificial intelligence into measurement systems is a promising direction. Machine learning algorithms can analyze data more effectively, optimize measurement processes, and predict performance outcomes based on surface characteristics.
- Hybrid Systems: Combining contact and non-contact methods can yield comprehensive results. Hybrid systems allow for a detailed analysis where contact methods can measure profile traits, while non-contact methods assess larger surface features.
These innovations not only improve the accuracy of measurements but also provide flexibility in different operational environments, catering to varying material and component specifications.
Integration of Technologies
The integration of diverse technologies is becoming increasingly important in surface roughness measurement. Multiple factors drive this convergence, including:
- Data Fusion: By merging data from different measurement methods, a more complete picture of the surface can be achieved. This fusion helps in understanding how various surface parameters interact, which can be critical in applications such as coatings and composites.
- Automation: Modern manufacturing and industrial processes require highly automated systems. Integrating surface roughness measurements with automated assembly lines enhances efficiency and quality control. Automation in measurement techniques can ensure consistency, reduce human error, and increase throughput.
- Real-time Monitoring: Incorporating real-time measurement systems into production lines allows for immediate feedback. This capability can lead to prompt adjustments in machining processes, thus minimizing defects and ensuring product quality.
- Collaborative Platforms: The growing trend towards open platforms enables collaboration among researchers and industries. Sharing methodologies, data, and findings can improve measurement techniques universally, promoting better standards and practices.
The future of surface roughness measurement research is bright, driven by innovation and integration. Keeping pace with these advancements will be crucial for professionals aiming to enhance measurement accuracy and application in various fields of science and engineering.
"Continuous improvement and adaptation are the laws of nature, and in the competitive landscape of surface roughness measurement, they are imperative for success."
By focusing on these evolving technologies and exploring innovative approaches, researchers can develop strategies that not only optimize surface quality assessment but also align with the advancing needs of modern industries.
Culmination
In the realm of surface roughness measurement, understanding the concluding elements is pivotal. This article highlights essential themes regarding the techniques of measuring surface roughness, serving not just as a summary but as a foundation for further exploration in this significant area of research and industry application. The methods discussed range from traditional contact-based techniques to innovative non-contact options, each with unique advantages and limitations.
Summary of Key Points
The article articulates several key points:
- Technological Diversity: Various measurement methods exist, catering to a range of applications in different sectors. Techniques like stylus profilometry and optical profilometry are covered, showcasing their operational principles and inherent benefits.
- Importance of Selection: Choosing the appropriate surface roughness measurement technique is critical, depending on the material and desired precision. Factors such as surface type and required accuracy play a decisive role in this selection process.
- Emerging Technologies: The article emphasizes how advancements, especially in machine learning and 3D measurement techniques, are reshaping the landscape of surface roughness assessment. These technologies promise more accurate and efficient measurement capabilities.
- Challenges and Compliance: It reflects on the challenges faced, including measurement errors and compliance with international standards, providing a realistic view of current limitations in the industry.
Implications for Future Research and Industry Practices
The implications of this study stretch far into future research and industry practices. Here are some considerations:
- Enhanced Techniques: As technology evolves, research should continue to focus on refining and optimizing both contact and non-contact measurement methods. This includes integrating machine learning algorithms for predictive accuracy.
- Standardization Efforts: There is a pressing need for further standardization across measurement techniques to simplify comparison and compliance across industries. Harmonization with international standards can enhance reliability in measurement outcomes.
- Human Factors: Future research should also address the human factors in the measurement process. Training and skill development are vital for professionals operating these sophisticated instruments.
"Embracing innovation in surface roughness measurement techniques is essential for maintaining competitiveness in a rapidly developing technological landscape."
- Interdisciplinary Approaches: Collaboration among various fields, such as material science, engineering, and data analytics, can lead to improved measurement methodologies and innovative solutions for existing challenges.
In summary, a thorough understanding of surface roughness measurement techniques not only enriches academic discourse but also enhances practical applications in industries ranging from manufacturing to aerospace. The contributions of this article provide valuable insights that can guide future endeavors in this crucial area of study.