Understanding Air Vacuum Chambers: Design and Uses
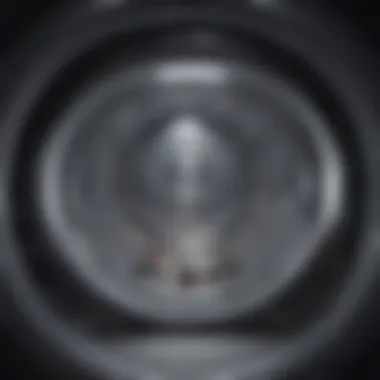
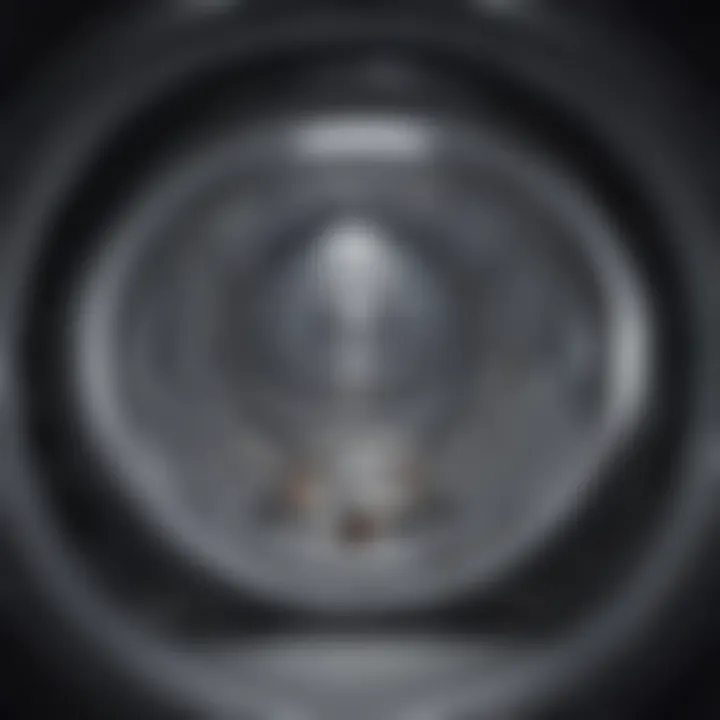
Intro
Air vacuum chambers serve as a pivotal element in various scientific and industrial applications. Understanding their functionality not only unveils fundamental principles of vacuum technology but also presents a wide spectrum of uses across multiple domains. The efficiency and precision that vacuum chambers bring to experimentation and manufacturing are nothing short of transformative.
Overview of Research Topic
Brief Background and Context
Vacuum chambers date back to the early experiments in physics, particularly in the study of gases and pressure variations. Over the years, advancements in technology have promoted the development of more sophisticated vacuum systems, enhancing their usability in laboratories and industrial settings. A vacuum chamber is essentially a sealed environment from which air has been removed, creating low-pressure conditions. This environment is crucial for various applications, including material testing, electron microscopy, and biological preservation.
Importance in Current Scientific Landscape
In contemporary research, air vacuum chambers play a significant role. Their ability to eliminate air leads to improved accuracy in experiments, especially in fields such as materials science, semiconductor production, and surface analysis.
"Vacuum systems are not merely tools; they are fundamental enablers of innovation in science and industry."
This quote underlines the essence of vacuum technology, as it continues to propel advancements in scientific endeavors and industrial processes. For professionals and researchers, understanding the functionality of air vacuum chambers is therefore not just an academic exercise; it is a gateway to harnessing their full potential in various applications, from creating high-purity environments to facilitating ultra-high vacuum conditions.
Methodology
Research Design and Approach
The examination of air vacuum chambers involves both theoretical and practical perspectives. Researchers often implement structured methodologies to analyze the design and functioning of these systems. The approach includes a thorough review of existing literature, experimental setups, and performance evaluation of various vacuum technologies.
Data Collection Techniques
Data collection methods typically encompass:
- Analytical studies of vacuum chamber designs
- Experimental trials to assess operational efficiency
- Surveys to gather insights from users in various industries
This combined methodology fosters a comprehensive understanding of how air vacuum chambers function and their broad applications in real-world scenarios.
Prelude to Air Vacuum Chambers
Air vacuum chambers are integral tools used in diverse fields such as scientific research and various industries. Understanding their functionality provides insight into how they enhance efficiency and reliability in processes that involve the manipulation of environments. They are especially vital in applications requiring precise conditions, where exposure to atmospheric pressures would alter results or compromise product integrity.
Definition and Purpose
An air vacuum chamber is defined as an enclosed space from which air and other gases have been removed, creating a vacuum environment. This process typically involves the use of vacuum pumps to expel air, resulting in lower pressure levels. The primary purpose of a vacuum chamber is to facilitate experiments and processes that need controlled atmospheres, free from contaminants that might interfere with outcomes. The applications can range from the testing of materials to the preservation of sensitive products.
In laboratories, vacuum chambers support sample preparation, allowing researchers to handle volatile substances or sensitive specimens. In industrial settings, they play a crucial role in manufacturing processes that require precision, such as in electronics production or material treatment. They can help maintain high-quality standards, reduce waste, and increase productivity, making them an essential asset in modern technology.
Historical Development
The development of air vacuum chambers traces back to the early advancements in vacuum technology. Initially, the idea of creating a vacuum originated from the studies of natural philosophers and inventors in the 17th century. Notably, scientists such as Evangelista Torricelli and Otto von Guericke contributed significantly to our understanding of vacuums by demonstrating that air has weight and can be removed from a space.
As the understanding of vacuum technology progressed, so did the designs of vacuum chambers. By the 19th century, with the advent of industrialization, systems began to evolve to cater to various applications, including scientific research and manufacturing. With the increasing need for controlled environments, advancements in materials and sealing techniques became crucial for ensuring the integrity of vacuum chambers.
Today, air vacuum chambers reflect sophisticated engineering, integrating technology that ensures optimal performance through specific designs and components tailored to meet varying requirements in both scientific and industrial contexts.
"The evolution of vacuum technology underscores its critical role in enhancing scientific discovery and industrial innovation."
Principles of Vacuum Technology
The principles of vacuum technology play a crucial role in the functionality and applications of air vacuum chambers. Understanding these principles is essential as it helps in grasping how vacuum systems operate and the benefits they provide across various fields. A well-designed vacuum system not only enhances experimental outcomes but also improves the efficiency of industrial processes.
Understanding Vacuum Levels
Vacuum levels are a key aspect of vacuum technology. They indicate how much the atmospheric pressure has been reduced within a chamber. The primary measurement of vacuum is in Torr or Pascals. The vacuum scale ranges from low vacuum to ultra-high vacuum, with each level having specific applications.
- Low Vacuum: This level has pressures above 1333.22 Pa (10 Torr) and is typically used in processes like drying and vacuum packaging.
- Medium Vacuum: It ranges from 133.3 Pa (1 Torr) to 100 microTorr (1/10,000 Torr). This level is common in laboratory environments.
- High Vacuum: In this category, pressures are lower than 100 microTorr but higher than 10^-9 Torr. Applications involve materials science and semiconductor manufacturing.
- Ultra-High Vacuum: This level has pressures lower than 10^-9 Torr. It is mainly used in research fields such as surface science and particle physics.
Understanding these levels helps in selecting the correct vacuum technology for specific applications. Vacuum levels also dictate the types of vacuum pumps and materials used in vacuum chambers.
Thermodynamics and Vacuum
Thermodynamics is equally important when discussing vacuum technology. Under vacuum conditions, changes in temperature and pressure significantly impact material behavior and chemical reactions.
- Gas Behavior: In a vacuum, the behavior of gases follows the ideal gas law. This law states that when the volume of gas increases, pressure decreases, given a constant temperature. As such, achieving a certain vacuum level requires understanding gas dynamics.
- Temperature effects: When air is removed from a chamber, the remaining gas molecules experience fewer collisions. This drop in pressure can lead to a decrease in temperature, depending on the material properties involved. Cooling can affect reactions in many scientific applications, such as creating stable environments for sensitive materials.
- Phase transitions: The behavior of substances under varying vacuum conditions can also affect phase transitions. For instance, water can boil at room temperature in very low-pressure conditions.
In summary, understanding thermodynamics in relation to vacuum technology is essential for optimizing processes and ensuring desired outcomes in both research and industrial applications.
Components of Air Vacuum Chambers
Understanding the components of air vacuum chambers is crucial for their effective utilization. The performance, safety, and efficiency of vacuum systems depend heavily on the design and quality of their components. Each part plays a specific role in achieving and maintaining the desired vacuum levels. This section explores the primary components, emphasizing their importance.
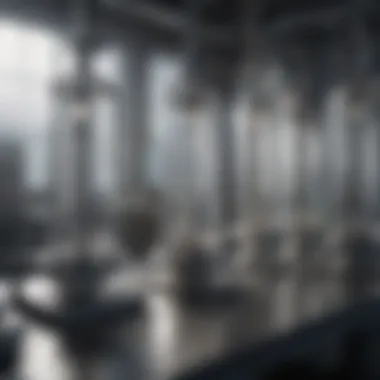
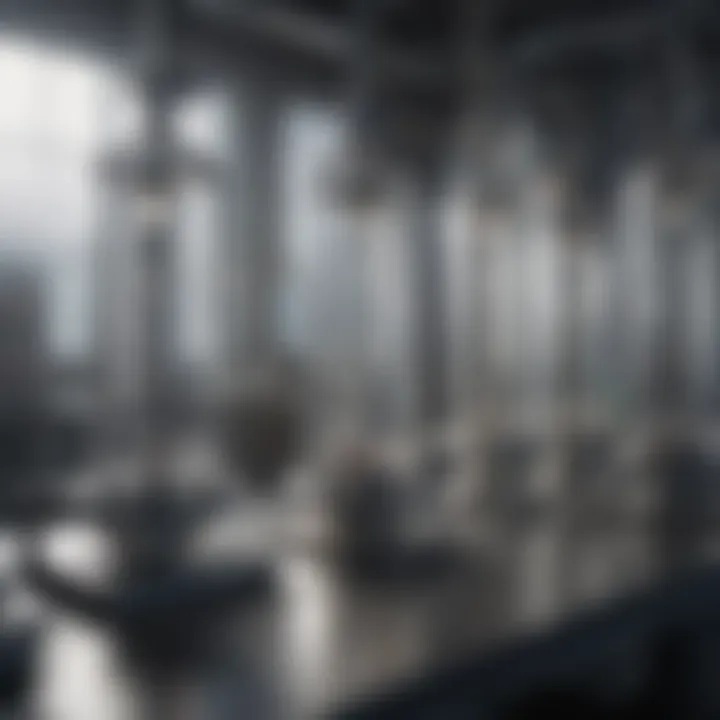
Chamber Design
Chamber design is foundational to the functionality of air vacuum chambers. The materials and structure determine how well the chamber can sustain a vacuum without leakage. Common materials used include stainless steel for its corrosion resistance and durability. The thickness of chamber walls also plays a role in preventing deformation under vacuum pressure.
A well-designed chamber should minimize dead space. Dead spaces are areas that do not effectively contribute to the sample environment. Their presence can lead to inconsistent results in experiments. Consequently, a streamlined design helps to enhance both measurement accuracy and processing efficiency.
Key Considerations for Chamber Design:
- Material Selection: Ensuring resistance to chemicals and physical stress is vital.
- Geometric Configuration: Shapes that enable easy access for equipment and samples also enhance functionality.
- Surface Finish: The smoothness of internal surfaces can affect the behavior of gases and samples within the chamber.
Vacuum Pumps
Vacuum pumps are essential in creating and maintaining the vacuum environment inside chambers. These devices actively reduce the amount of air and other gases from the chamber to achieve desired pressure levels. There are several types of pumps, and each has its own applications. For instance, rotary vane pumps are commonly used for rough vacuum applications, while turbo molecular pumps can reach much lower pressures.
Proper integration of vacuum pumps into the system is important. Their compatibility with the chamber and the required vacuum levels affects the overall system performance. Additionally, maintenance and operational efficiency of these pumps are critical for sustained performance. A failed pump can lead to contamination or inadequate vacuum levels, which disrupts experiments or industrial processes.
Types of Vacuum Pumps:
- Rotary Vane Pumps: Reliable for rough vacuum levels.
- Diaphragm Pumps: Ideal for low to medium vacuum applications.
- Turbo Molecular Pumps: Excellent for high vacuum conditions.
Sealing Mechanisms
Sealing mechanisms ensure the integrity of the vacuum environment within the chambers. Any breach in the seal can result in pressure loss, which in turn compromises the experiments or processes being conducted. Various sealing techniques are utilized in air vacuum chambers, including elastomer seals, metal seals, and welded seams.
The selection of sealing methods depends on several factors. These factors include the working environment, temperature fluctuations, and chemical exposure. For instance, elastomer seals are commonly used for their flexibility and ability to conform to surfaces. However, they may not withstand extreme conditions as effectively as metal seals.
Considerations for Sealing Mechanisms:
- Material Durability: Ensuring seals withstand operational conditions.
- Chemical Compatibility: Selecting appropriate seal materials that don't degrade in the presence of specific chemicals.
- Ease of Maintenance: Choosing seals that allow for easy replacement and maintenance can enhance functionality.
Proper attention to the components of air vacuum chambers ensures the desired performance, enhancing both experimental and industrial processes.
Understanding these components is essential for students, researchers, and professionals who employ vacuum technology across various applications. The effectiveness of vacuum chambers hinges not only on the technology itself but also on careful considerations of their individual elements.
Types of Air Vacuum Chambers
Understanding the different types of air vacuum chambers is crucial for anyone involved in scientific research or industrial applications. Each type serves specific purposes and possesses unique characteristics. Recognizing these distinctions enables users to select the appropriate chamber that meets their specific requirements. This section highlights three prominent types of air vacuum chambers: standard vacuum chambers, custom vacuum chambers, and high-precision chambers.
Standard Vacuum Chambers
Standard vacuum chambers are the most common type in laboratories and industrial settings. These chambers are designed to achieve a specific vacuum level suitable for various applications. They come in several sizes and shapes, accommodating different experimental and operational needs. Standard vacuum chambers typically consist of simple designs that include effective sealing mechanisms and robust materials to withstand the stresses of operation.
The key benefits of standard vacuum chambers include their reliability and ease of use. They often integrate seamlessly with commonly used vacuum pumps, making the setup process straightforward. Their cost-effectiveness also plays a significant role, allowing many researchers and companies to access vacuum technology without excessive investment.
However, it is essential to consider that while standard vacuum chambers serve general purposes effectively, they may not always meet the demands of specialized applications. Users must assess their specific needs before opting for this type.
Custom Vacuum Chambers
Custom vacuum chambers cater to unique requirements that standard chambers may not fulfill. These chambers are designed specifically to meet the precise needs of a particular operation or experiment. Custom vacuum chambers may vary in complexity, size, and additional features depending on their intended application.
The advantage of custom vacuum chambers lies in their versatility. Users can specify dimensions, materials, and integrated technologies to optimize performance. For instance, a research team studying sensitive materials might require chambers made from non-reactive and low-outgassing materials to preserve sample integrity.
Despite their tailored nature, custom vacuum chambers may come with higher costs and longer lead times. It is also vital to ensure that the customization does not compromise structural integrity or vacuum performance. A thorough evaluation of the expected outcomes versus costs should take place before committing to a custom solution.
High-Precision Chambers
High-precision chambers are engineered for applications requiring stringent control of environmental conditions. These chambers minimize variations in temperature, pressure, and contamination levels to ensure accurate results. They are often used in high-stakes research and specialized manufacturing where precision is critical.
The characteristics of high-precision chambers include advanced monitoring and control systems that allow for real-time adjustments. This makes them suitable for experiments in fields such as semiconductor fabrication, material science, and pharmaceutical development. Their design often features multi-layered sealing systems and advanced vacuum pumps for reduced fluctuations and improved stability.
However, the use of high-precision chambers involves a trade-off. They tend to be more expensive due to their sophisticated features and careful manufacturing processes. Users must also have adequate training to operate these systems efficiently, as improper use can lead to significant errors in experiments.
"Choosing the right type of vacuum chamber plays a crucial role in the success of your applications. Each type offers distinct benefits that must align with your specific objectives."
In summary, understanding the various types of air vacuum chambers helps stakeholders make informed decisions. Standard vacuum chambers suit general needs, while custom solutions cater to specific requests. High-precision chambers excel in controlled environments. A clear comprehension of these categories is vital for optimizing research and industrial processes.
Applications in Scientific Research
Air vacuum chambers play a crucial role in scientific research. They provide an isolated environment where variables can be precisely controlled. This is essential in experiments where maintaining specific conditions is vital for accurate results. The use of vacuum technology opens up unique methodologies which are not possible under normal atmospheric conditions. Moreover, it enhances the reliability of data collected from different types of research.
Sample Preparation
In many scientific fields, effective sample preparation is foundational to the success of experiments. Air vacuum chambers enable researchers to remove gases and moisture from samples without altering their properties. This process is particularly important in chemistry and materials science. By preparing samples under vacuum, researchers can ensure that the materials they are working with are free from contaminants that could affect the experiment's outcomes. For instance, in the case of fresh chemical analyses, vacuum-sealed environments can prevent oxidation, thereby preserving the integrity of reactive substances.
"Sample preparation under controlled vacuum conditions limits contaminations and preserves material properties for precise experimentation."
Chemical Reactions Under Vacuum
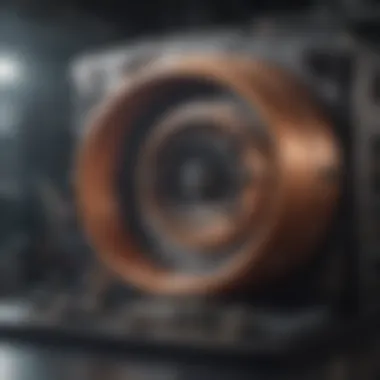
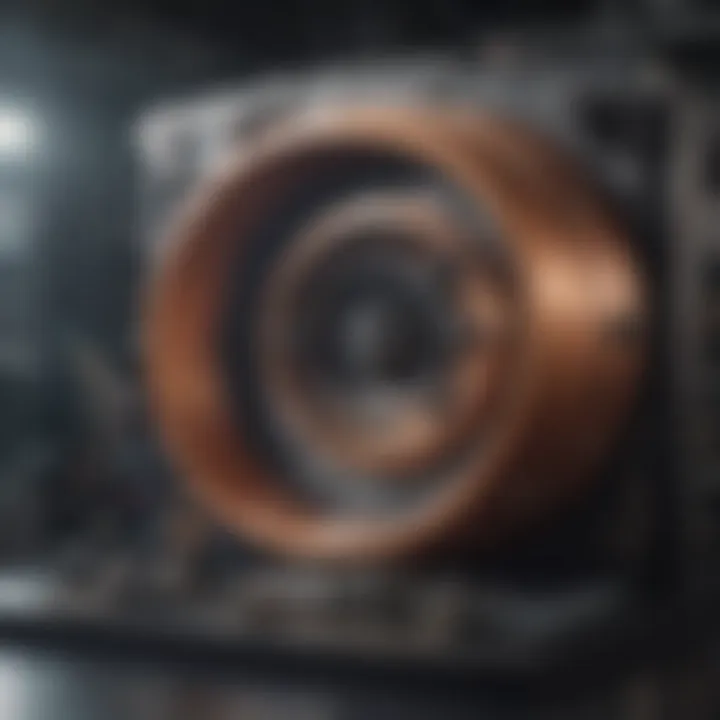
Chemical reactions that occur in a vacuum can lead to unique results, different from those at atmospheric pressure. The reduced presence of air allows certain reactions to proceed without interference from unwanted gases. For example, undesirable byproducts, such as water vapor in gas-phase reactions, can be effectively minimized. This is especially valuable in synthetic organic chemistry, where the establishment of high purity in reactants significantly impacts yield and quality.
Performing reactions under vacuum also contributes to the quality of products by enabling higher reaction rates and better formation of intermediates. \nMoreover, reactions that typically require high temperatures can often be carried out at lower temperatures in a vacuum, which further protects sensitive components and reduces energy consumption.
Material Characterization
Material characterization is another essential aspect of scientific research where air vacuum chambers are utilized. Techniques such as scanning electron microscopy (SEM) and transmission electron microscopy (TEM) require samples to be in a vacuum to prevent scattering of electrons. When materials are analyzed under vacuum, researchers can obtain precise insights regarding the material properties, such as composition, structure, and surface morphology.
This methodology is applicable in various fields, including nanotechnology and metallurgy, where understanding the properties of materials at a microscopic level is critical. Furthermore, characterizing materials under vacuum can unveil defects, phase transitions, and interaction mechanisms that would otherwise be obscured in normal atmospheric conditions.
Industrial Applications
The role of industrial applications of air vacuum chambers is significant across various sectors. Vacuum chambers facilitate processes that demand controlled environments. They assist in optimizing quality, efficiency, and safety in manufacturing, food processing, and pharmaceuticals. Understanding these applications helps industries enhance their operations.
Manufacturing Processes
In manufacturing, air vacuum chambers serve multiple functions. They support processes like vacuum forming and degassing. These processes are essential in creating high-quality products. For example, in plastic manufacturing, vacuum forming uses heat and vacuum to shape materials accurately, reducing defects significantly.
Vacuum chambers also play a key role in surface treatment. Techniques like coating or plating require a vacuum environment for better adhesion and quality. This process minimizes oxidation and contamination, resulting in superior finishes.
- Key advantages in manufacturing:
- Improved product quality
- Reduced production defects
- Enhanced material properties
Food Preservation
Air vacuum chambers revolutionize food preservation methods. They remove air around food products, thus inhibiting the growth of spoilage organisms. Vacuum packaging extends shelf life significantly while maintaining freshness and flavor. This is done by minimizing oxidation and moisture loss. Foods like meats, cheeses, and vegetables benefit especially from vacuum preservation.
Additionally, vacuum chambers allow for better controlled storage conditions. This helps in keeping food products safe for longer periods.
Advantages in food preservation include:
- Extended shelf life
- Maintained nutritional value
- Reduction in food waste
Pharmaceutical Applications
In the pharmaceutical industry, air vacuum chambers are critical for many procedures. They are involved in processes such as sterile drug formulation and packaging. The vacuum environment prevents contamination, ensuring product safety. Sterile packaging, which often employs vacuum sealing, is a standard practice for maintaining drug efficacy.
Vacuum technology also aids in lyophilization (freeze-drying). This process removes moisture from medications and biological samples, preserving their properties.
The benefits in pharmaceuticals are notable:
- Enhanced product safety
- Longer shelf life for drugs
- Reduced risk of contamination
"Air vacuum chambers are indispensable in the pharmaceutical industry for maintaining the integrity and quality of products."
In summary, the industrial applications of air vacuum chambers are vital for improving quality and efficiency across various sectors. They reduce risks, enhance safety, and ensure product reliability, contributing to better practices in manufacturing, food preservation, and pharmaceuticals.
Advantages of Using Air Vacuum Chambers
Air vacuum chambers are pivotal in numerous applications across scientific and industrial landscapes. Their functionalities bring about several advantages that can not be overlooked. This section examines the key benefits, focusing on how these chambers enhance control over environments, minimize contaminants, and improve efficiency. Each aspect not only showcases the operational merits but also their critical role in driving technological advancements.
Enhanced Control Over Environments
One of the standout advantages of air vacuum chambers is the enhanced control they offer over experimental and manufacturing environments. In many scientific endeavors, precise manipulation of factors such as pressure, temperature, and atmosphere can be crucial for valid results. By creating a controlled vacuum environment, researchers can eliminate variables that might affect their results, leading to more accurate and reproducible findings.
For instance, in materials science, testing the properties of metals or polymers under vacuum can provide insights unattainable at atmospheric pressure. This sealed environment prevents reactions with oxygen or moisture, which could alter material characteristics unexpectedly. Ultimately, enhanced control leads to superior data quality and reliability, which is fundamental for progressing research and innovation.
Minimizing Contaminants
Another significant benefit of air vacuum chambers involves their ability to minimize contaminants during various processes. In fields such as electronics, pharmaceuticals, and food preservation, the presence of contaminants can compromise product integrity and safety.
Air vacuum chambers effectively reduce the chances of oxidation, moisture contamination, and particulate infiltration. By maintaining a vacuum state, these chambers not only protect sensitive materials but also extend shelf life in food preservation applications, allowing products to maintain flavor and nutrition without the use of preservatives.
Contaminant minimization is especially important in environments where purity is paramount. For instance, the pharmaceutical industry relies on vacuum chambers during the manufacturing of sterile products. Ensuring the absence of microbial contaminants is critical for patient safety and product efficacy.
Improving Efficiency
Efficiency is another hallmark of using air vacuum chambers. These chambers facilitate faster processes by reducing reaction times and improving throughput. In manufacturing settings, employing vacuum technology can lead to quicker mold fill times in casting processes, enhancing productivity.
Furthermore, the control provided by the vacuum state can boost overall energy efficiency. When working under vacuum conditions, the energy required for certain reactions decreases, leading to lower operational costs.
In sum, the interplay of improved control, contaminant reduction, and enhanced efficiency makes air vacuum chambers indispensable in modern scientific and industrial applications. These advantages support their widespread adoption, contributing to more precise outcomes and better resource management in various fields.
"Air vacuum chambers are not merely tools; they are foundational elements that propel research and innovation forward in countless industries."
Limitations of Air Vacuum Chambers
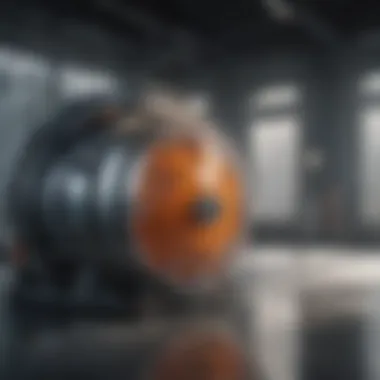
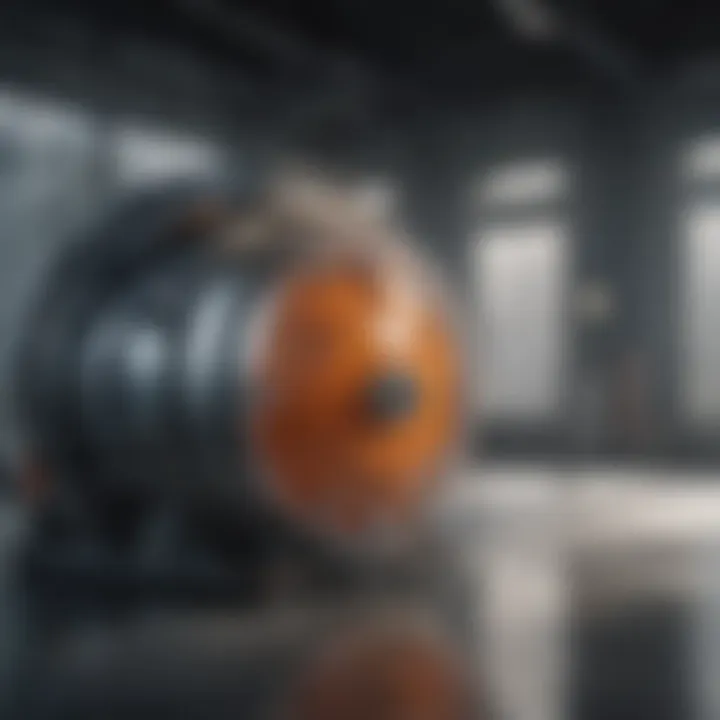
Air vacuum chambers play a significant role in various scientific and industrial applications. However, they are not without limitations. Understanding these constraints is essential for users, as it influences their effectiveness and cost efficiency. Here, we explore two critical limitations encountered in the utilization of air vacuum chambers: cost considerations and technical challenges.
Cost Considerations
Cost is a primary factor when investing in air vacuum chambers. These chambers, along with their associated equipment, can require substantial financial resources. The initial purchasing price of standard chambers is often only a part of the total cost. Additional costs may include installation, maintenance, and operational expenses. This is especially true for high-precision models that demand advanced technology and materials.
- Initial Investment: High-quality vacuum chambers, particularly high-precision ones, have a steep initial cost.
- Ongoing Maintenance: Regular maintenance is crucial and can incur additional expenses. This aspect is crucial for safeguarding the longevity and efficiency of the equipment.
- Technical Support Costs: Users may need to factor in expenses for training staff or hiring specialists knowledgeable about vacuum technology. This may lead to increased operational costs over time.
Considering these elements, organizations must weigh their budget against the benefits of utilizing air vacuum chambers.
Technical Challenges
Apart from cost, technical challenges pose significant hurdles in the operation of air vacuum chambers. Users often face various complexities that can hinder the performance of these devices.
- Leakage Issues: One of the most common challenges is chamber leakage. Small imperfections in seals or fittings can lead to pressure fluctuations, affecting the intended experimental conditions.
- Material Compatibility: Not all materials are suitable for vacuum applications. The materials used for the vacuum chambers must be compatible with the substances processed inside to prevent contamination or reactions.
- Control and Monitoring: Advanced control systems are necessary for monitoring vacuum levels accurately. Developing and maintaining sophisticated monitoring equipment can be technically demanding and costly.
"Understanding the limitations of air vacuum chambers is crucial for making informed decisions regarding their use in different applications."
Safety Considerations
Safety considerations are paramount when operating air vacuum chambers. The vacuum environment inherently poses risks that must be managed properly to ensure safe usage. Understanding these risks can help prevent accidents and equipment damage, which is critical in both scientific and industrial settings.
Pressure Management
One of the most critical aspects of safety in vacuum chambers is pressure management. Vacuum chambers operate by creating a negative pressure environment, which can lead to significant physical stresses on the chamber's structure. If these chambers are improperly designed or fail to maintain the correct pressure levels, they can collapse or implode. Regularly inspecting the integrity of the vacuum chamber is essential.
Here are key elements to consider regarding pressure management:
- Monitoring Gauge Accuracy: Ensure that the vacuum gauges are regularly calibrated and checked for accuracy. Inaccurate readings can lead to unsafe pressure levels.
- Pressure Relief Valves: These should be installed to prevent over-pressurization. In the event of a failure, they allow for controlled release of air, protecting the chamber from damage.
- Regular Maintenance: Conduct routine checks on seals, pumps, and the chamber itself to maintain proper functionality. This helps avoid sudden pressure loss or gain that can lead to dangerous situations.
Following these guidelines can significantly mitigate the risks associated with pressure fluctuations in vacuum chambers.
Material Compatibility
The compatibility of materials used in constructing and operating air vacuum chambers is equally essential for safety. Various materials can react unpredictably when exposed to the vacuum environment or the substances being tested within the chamber. Failing to consider these interactions can result in equipment failure or hazardous situations.
Important factors to assess include:
- Material Strength: The materials must withstand the forces exerted during the vacuum process without cracking or breaking.
- Chemical Reactivity: Materials should be chosen based on their non-reactivity with the substances intended for use in the vacuum chamber. Mismatches here can lead to contamination or dangerous reactions.
- Thermal Stability: Consider how materials react under extreme temperature changes, which can occur in many vacuum applications.
"Choosing the right materials is as important as managing the pressure when it comes to safe operation of vacuum chambers."
By focusing on these safety considerations, users can create a compliant and hazard-free working environment, thus ensuring successful outcomes in their applications.
Future Trends in Vacuum Technology
The landscape of vacuum technology is continually evolving. Innovations in this field present both fascinating opportunities and essential considerations for the future. As industries increasingly rely on air vacuum chambers, understanding upcoming trends is critical for staying updated with advancements that can enhance performance and efficiency in various applications. This section explores some pivotal trends, focusing on innovations in design and the growing integration with automation.
Innovations in Design
Innovations in design are redefining air vacuum chambers. Modern chambers are becoming more compact, allowing for limited space without sacrificing functionality. These designs often utilize lighter materials, which improve portability while maintaining structural integrity. Additionally, manufacturers are incorporating advanced computational fluid dynamics in the design process. This approach ensures better airflow management within the chamber, optimizing vacuum levels and reducing cycle times.
Another significant innovation is modular designs. These allow customization based on specific requirements. Researchers and industries can now modify components without needing entirely new chambers. This adaptability also enables easier upgrades, which is cost-effective in the long run. Furthermore, energy efficiency has become a primary focus. New insulation techniques and intelligent vacuum pumps minimize energy consumption, reducing operational costs and environmental impact.
"Future designs in vacuum technology will prioritize efficiency and adaptability, addressing the increasing demand for customized solutions."
Integration with Automation
The integration of automation in vacuum technology is becoming unavoidable. Automated systems control various aspects of air vacuum chambers, enhancing precision and minimizing human error. For instance, automated monitoring systems can maintain optimal vacuum levels and detect leaks promptly. This capability significantly increases the reliability of experiments and industrial processes.
Moreover, industries are embracing the Internet of Things (IoT) for real-time data acquisition and analysis. Sensors embedded within vacuum chambers transmit data to centralized systems, providing insights into performance metrics. Such information allows for predictive maintenance, ensuring that issues are identified before they cause failures.
The fusion of robotics with vacuum technology also merits discussion. Automated robotic systems can manage the chambers' loading and unloading processes efficiently. This development is especially valuable in manufacturing sectors where time efficiency is crucial. Ultimately, the blend of automation and vacuum technology is set to reshape workflows, significantly enhancing efficiency and productivity across various fields.
Closure
The conclusion of the article serves as a crucial element, encapsulating the findings and the essential insights drawn from the exploration of air vacuum chambers. It provides clarity on the function and applications of these chambers, emphasizing their role within both scientific research and industrial contexts. Understanding these applications reveals the broader significance of maintaining controlled environments, which can be critical for obtaining accurate results in experiments, ensuring product quality, and extending the shelf life of various materials.
Summary of Key Points
In summation, several key points are prominent throughout the article:
- Air vacuum chambers function by removing air, thereby creating a controlled environment.
- Their applications range from scientific research, such as sample preparation and material characterization, to industrial uses like food preservation and pharmaceutical processes.
- The advantages include enhanced control over experiments, a reduction in contaminants, and improved operational efficiency.
- However, limitations exist, such as high costs and technical challenges that must be addressed.
- Safety considerations are paramount, with concerns regarding pressure management and material compatibility highlighted.
- Finally, trends in vacuum technology suggest ongoing innovations in chamber designs and automation integration.
Final Thoughts on Air Vacuum Chambers
Air vacuum chambers represent a fusion of engineering and scientific inquiry. Their design and construction are vital for achieving vacuum levels necessary for various applications. As industries evolve and scientific understanding deepens, the importance of these chambers will continue to grow. They not only enhance our ability to conduct precise experiments but also offer practical solutions to everyday challenges, from food safety to drug manufacturing.
This article underscores the indispensable role of air vacuum chambers in progressing technology and scientific exploration. As future trends unfold, continual advancements in this field will likely lead to more efficient, automated, and user-friendly designs.
"The true power of vacuum technology lies in its ability to reshape our approach to scientific and industrial challenges."
By acknowledging their significance, we can ensure that air vacuum chambers will sustain their critical status in our laboratories and factories for years to come.