Ultrasonic Monitoring Equipment: Principles and Applications

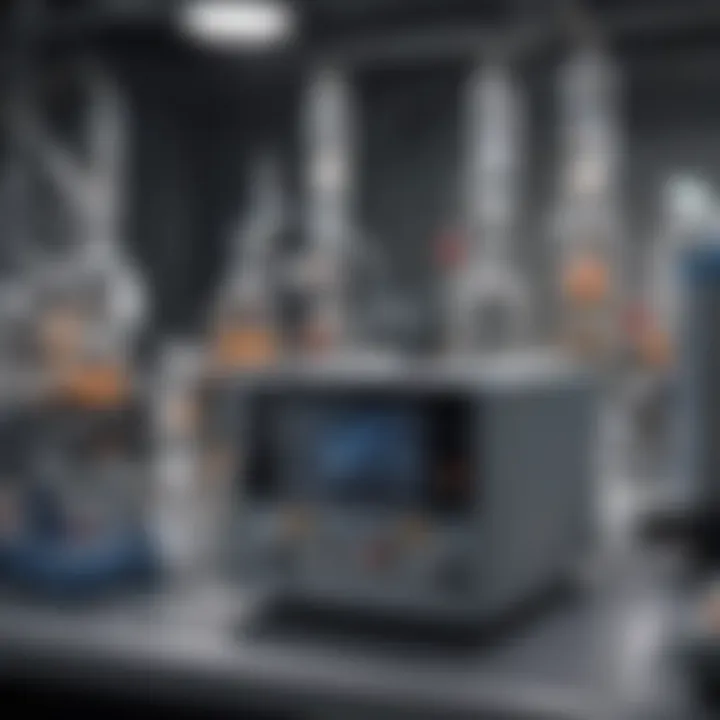
Overview of Research Topic
Brief Background and Context
Ultrasonic monitoring equipment, a blend of artful engineering and cutting-edge technology, has evolved dramatically over the years. Originally, it found its roots in sonar technology used by submarines and ships for navigation and detection. However, its applications have since expanded well beyond the ocean's depths, penetrating realms as varied as medical diagnostics, structural engineering, and manufacturing processes.
As we march further into the era of automation and data-driven decision-making, the reliance on accurate monitoring solutions becomes increasingly vital. This is where ultrasonic technology shines with its ability to provide insight into systems that are often cloaked from view.
Importance in Current Scientific Landscape
The significance of ultrasonic monitoring cannot be overstated. Industries today are clamoring for equipment that ensures precision and reliability without the need for invasive measures. In settings like hospitals, ultrasonic devices allow for visualization of internal body structures without surgery, a key advantage for both diagnostic purposes and patient safety.
Moreover, in engineering and civil applications, ultrasonic testing helps detect flaws and inconsistencies in materials, which can be the difference between a safe structure and potential disaster. The ability to monitor conditions in real time opens up new doors to preventative maintenance, ultimately saving time and resources.
"Ultrasonic technology plays a pivotal role in ensuring quality and safety across multiple sectors, making it indispensable in our modern world."
Methodology
Research Design and Approach
This exploration unfolds through a qualitative lens, harnessing case studies, expert interviews, and academic literature to provide a holistic understanding of the ultrasonic monitoring landscape. By weaving together diverse threads of research, including engineering principles and user experiences, one can appreciate not just how these devices work but also their failures and successes in practical applications.
Data Collection Techniques
Data for this study was gathered through various channels:
- Academic Journals and Publications: Dive into the depths of research that illuminates new findings in ultrasonic technology.
- Interviews with Industry Experts: Real-world insights give clarity to theoretical concepts; conversations with engineers and healthcare professionals reveal application nuances.
- Field Observations: Case studies from manufacturing plants and hospitals showcase the effectiveness of ultrasonic equipment in action.
Together, these approaches present a well-rounded body of knowledge, shining a light on both the intricacies and implications of ultrasonic monitoring systems.
Prologue to Ultrasonic Monitoring
In a world that increasingly relies on precise measurements and real-time data, ultrasonic monitoring has carved out a niche that is both unique and vital. It's not just about sound; it's about harnessing the power of acoustics to monitor everything from material thickness in bridges to the flow rates in medical applications. Its significance lies in the ability to offer non-invasive insights that are often crucial for safety and efficiency in various industries.
Definition and Importance
Ultrasonic monitoring involves detecting and analyzing sound waves that are above the frequency range of human hearing, typically above 20 kHz. This methodology provides a versatile approach to monitoring and evaluating a range of conditions and components. For instance, ultrasonic thickness gauges help engineers check for corrosion without touching the material itself, while ultrasonic flow meters allow for the safe measurement of liquids without disruption.
The importance of this technology is underscored by its application across multiple domains:
- Safety and Assessment: Regular monitoring can prevent catastrophic failures in structures, potentially saving lives.
- Operational Efficiency: Accurate flow measurements can optimize processes in manufacturing and healthcare, reducing waste and saving costs.
- Environmental Monitoring: Ultrasonic technology plays a key role in assessing and minimizing the environmental impact of various industrial activities.
Thus, understanding the fundamentals of ultrasonic monitoring is not merely academic; it’s vital for informed decision-making in sectors such as engineering, healthcare, and environmental science.
Historical Development
The roots of ultrasonic monitoring can be traced back to the early 20th century, primarily linked with advancements in sonar technology. Initially developed for naval applications during World War I, these sound wave technologies have come a long way since then. The evolution of ultrasonic devices gained momentum in the mid-20th century when researchers began aligning them with non-destructive testing methods, allowing for material inspection without causing damage.
During the late 1960s and 1970s, manufacturers started to recognize the broader applications of ultrasonics in industries like aerospace, automotive, and even healthcare. This period was marked by significant innovations, including the development of portable ultrasonic testing devices, which enabled engineers and technicians to perform assessments on-site, rather than relying solely on laboratory conditions.
Fast forward to the 21st century, advancements in digital technology and miniaturization have propelled ultrasonic monitoring to new heights. Today, devices are more sophisticated, incorporating features like Internet of Things (IoT) connectivity and data analytics capabilities. This evolution not only enhances reliability but also expands the potential applications, making ultrasonic monitoring an indispensable tool in modern industry.
"The journey of ultrasonic technology reflects humanity's continuous quest for precision and safety in an increasingly complex world."
Fundamental Principles of Ultrasonic Technology
Understanding the fundamental principles of ultrasonic technology is essential as this forms the bedrock upon which all ultrasonic monitoring equipment operates. This section digs into the mechanics behind sound wave behavior, its characteristics, and how these factors contribute to the efficacy of ultrasonic technology in various applications.
Sound Wave Propagation
Sound waves are vibrations that travel through different mediums such as air, liquid, or solid materials. The ability to manipulate these waves effectively is one of the cornerstones of ultrasonic technology. The propagation of sound waves can vary significantly depending on the medium through which they travel.
For instance, in air, ultrasonic waves dissipate much more quickly compared to water. This is because water provides greater density, allowing ultrasonic waves to travel further without losing energy.
Moreover, sound waves travel at varying speeds in different materials; for example, in steel, sound waves can travel at about 5,960 meters per second, while in water, the speed is approximately 1,480 meters per second. Such differences are not merely technical details but play a crucial role in applications such as ultrasonic thickness measurement or flow detection. Knowing how sound waves propagate can significantly influence the choice of equipment for specific tasks.
Frequency and Wavelength Relations
Frequency and wavelength are tightly interlinked concepts in ultrasonic monitoring. The frequency of a sound wave determines its pitch, while wavelength refers to the distance between successive peaks of the wave. In practical terms, higher frequency generally means shorter wavelengths. This relationship can be summarized in the equation:
[ \textSpeed of Sound = \textFrequency \times \textWavelength ]
In ultrasonic applications, frequencies typically range from 20 kHz to several MHz. Higher frequencies provide better resolution and sensitivity, which is vital in applications like medical imaging or precision industrial measurements.
However, a trade-off exists. Higher frequency waves have shorter wavelengths and require careful calibration for effective penetration into materials. For instance, while a high-frequency ultrasonic thickness gauge may provide precise measurements on thin materials, lower frequencies are better suited for thicker sections. Understanding these concepts is essential for anyone involved in ultrasonic technology to ensure correct applications.
Doppler Effect in Ultrasonics
The Doppler Effect is a remarkable phenomenon that occurs when there is relative motion between a sound source and an observer. It results in a change in the frequency of the sound waves depending on whether the source is moving towards or away from the observer. This effect can have significant implications in the context of ultrasonic monitoring.
In many applications, such as flow metering, the Doppler Effect is utilized to measure the speed of moving fluids. When ultrasonic waves are transmitted into a flowing medium, the waves bounce back to the sensor, but the frequency of these returning waves will vary based on the velocity of the fluid.
This change in frequency can be calculated and then translated into speed, providing real-time data on the flow characteristics of the medium under examination:
- Moving Towards: Frequency increases
- Moving Away: Frequency decreases
By employing the Doppler Effect, industries can gain critical insights into fluid dynamics, whether it be in wastewater management or within pipelines.
In summary, diving into the fundamental principles of ultrasonic technology reveals how intertwined sound propagation, frequency and wavelength relations, and the Doppler Effect are with the various applications that rely on this technology. For professionals and scholars alike, these foundational concepts not only inform the operational efficacy of the equipment but also pave the way for further innovations in the field.
Types of Ultrasonic Monitoring Equipment
Understanding the types of ultrasonic monitoring equipment is essential for grasping how this technology serves various industries. Different applications require specific functionalities, and thus, the devices that utilize ultrasonic technology cater to these diverse needs. Knowing what each type of equipment does, its benefits, and how they contribute to operational efficiency helps in selecting the appropriate tool for a task. This section offers a detailed look at three primary types: Ultrasonic Thickness Gauges, Ultrasonic Flow Meters, and Ultrasonic Level Sensors. Each plays a vital role in enhancing measurement accuracy, ensuring safety, and improving productivity across different fields.
Ultrasonic Thickness Gauges
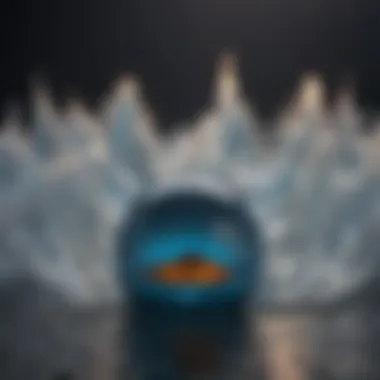
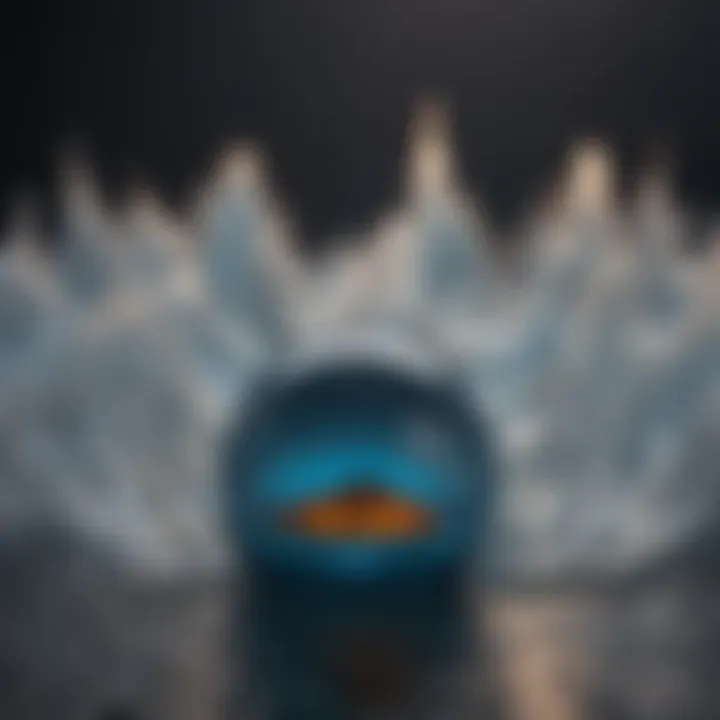
Ultrasonic thickness gauges are indispensable in industries such as construction, manufacturing, and pipeline maintenance. These devices reliably measure material thickness, ensuring structural integrity in applications that depend on precise data. They work by sending high-frequency sound waves through a material and measuring the time it takes for the echoes to return. This method is non-invasive, making it a preferred choice in environments where traditional measurement techniques may damage surfaces.
One of the standout benefits of ultrasonic thickness gauges is their ability to penetrate various materials, including metals and plastics. For instance, in pipeline monitoring, they help to identify potential corrosion or wear before it leads to critical failures. The reliability of these measurements can’t be overstated—it not only protects assets but also supports compliance with safety standards.
Moreover, many of today's ultrasonic gauges come equipped with digital displays and data logging capabilities, enabling easy interpretation of results and facilitating long-term monitoring strategies.
Ultrasonic Flow Meters
In the realm of fluid dynamics, ultrasonic flow meters have carved out a significant niche. These devices calculate the flow rate of liquids and gases using the principles of ultrasound, often found in environments such as water treatment plants, oil and gas facilities, and HVAC systems. Their operation usually falls into two categories: transit-time and Doppler, with each providing distinct advantages.
Transit-time flow meters are excellent for clean fluids, while Doppler meters excel in applications with particulate or bubbles. Their ability to provide accurate readings without obstructing flow—thanks to non-invasive clamp-on designs—is a noteworthy advantage.
Reasons to invest in ultrasonic flow meters include:
- Accuracy: They offer precise measurements crucial for regulatory compliance and operational efficiency.
- Versatility: Applicability spans across various industries — think food and beverage, oil and gas, or pharmaceutical sectors.
- Cost-Effectiveness: Reduced maintenance costs compared to mechanical flow meters, as they have fewer moving parts.
Ultrasonic Level Sensors
Ultrasonic level sensors are pivotal for monitoring the levels of liquids and solids in a variety of settings. They send out ultrasonic waves that detect when they bounce back off a surface, thereby determining the material's level. Commonly employed in tanks, silos, and other storage facilities, these sensors can operate under harsh environmental conditions, making them versatile and reliable.
The key features of ultrasonic level sensors include:
- Non-contact Measurement: Useful for materials that might be dangerous to approach or for environments where contact measurement could lead to contamination.
- Wide Range of Application: From wastewater treatment facilities to agricultural silos, their usability spans quite a large spectrum.
- Adaptability: Many models adapt to various conditions, such as foam, dust, and temperature variances, ensuring consistent performance.
In summary, understanding these types of ultrasonic monitoring equipment and their distinct functions enhances the ability to leverage their potential effectively. Each device not only presents unique specifications but equally offers expansive opportunities for improved processes within multiple industries.
Operational Mechanisms
The operational mechanisms of ultrasonic monitoring equipment play a pivotal role in ensuring that devices function efficiently and provide accurate measurements. Understanding these mechanisms equips users with the knowledge to select appropriate tools, enhancing their monitoring abilities, and improving decision-making processes across various applications. Delving into transducer functionality, signal processing techniques, and calibration processes offers insights into how these systems work and the considerations necessary to maintain their reliability and precision.
Transducer Functionality
At the heart of ultrasonic monitoring equipment lies the transducer. This component acts as the translator between electrical signals and sound waves. Essentially, it converts electrical energy into ultrasonic energy and vice versa, allowing for effective measurement of various parameters. The functionality of transducers is critical due to the following aspects:
- Types of Transducers: Different transducers exist for specific applications, such as contact and immersion types. Each has its unique characteristics, suitable for particular environments.
- Operational Range: The frequency range of transducers determines their effectiveness. Higher frequencies offer better resolution suitable for thin materials, while lower frequencies penetrate deeper, making them suitable for denser materials.
- Material Considerations: Transducer materials impact sensitivity and response. For instance, piezoelectric materials are common due to their favorable conversion efficiency.
Utilizing the right transducer for a task can mean the difference between accurate and flawed measurements, which underscores the necessity of comprehending their functionality.
Signal Processing Techniques
After sound waves are emitted and received, they undergo signal processing to extract meaningful information. This stage remains vital in transforming raw data into interpretable results. Various techniques are employed during this process:
- Filtering: Noise reduction enhances the clarity of signals. Different algorithms apply low-pass or high-pass filters to eliminate unwanted frequencies and enhance measurement reliability.
- Digitization: Converting analog signals into digital format allows for easier manipulation and analysis. This results in more sophisticated data handling and storage methods.
- Data Interpretation: Advanced algorithms help discern patterns or anomalies in the data, providing deeper insights that can guide operational decisions.
This phase turns what could be an overwhelming amount of data into comprehensible forms, thereby facilitating more informed choices in real-time applications.
Calibration Processes
Calibration of ultrasonic equipment is non-negotiable in maintaining measurement integrity. This process ensures the equipment yields accurate and reliable results over time. Key considerations in calibration include:
- Regular Intervals: Establishing a routine schedule for calibration helps maintain accuracy. Environmental factors can shift the performance characteristics of the equipment over time.
- Reference Standards: Utilizing known standards during calibration allows for precise adjustments. Calibration can involve comparison against trusted references to validate measurements.
- Documentation: Keeping meticulous records of calibration results, procedures, and intervals aids in traceability and accountability. This documentation can be invaluable when auditing or troubleshooting systems.
Calibration serves as a crucial foundation for the efficacy of ultrasonic monitoring systems, greatly impacting their performance and reliability.
By investing attention in understanding transducer functionality, implementing sound signal processing techniques, and adhering to rigorous calibration protocols, one can significantly improve the performance and reliability of ultrasonic monitoring equipment. This understanding ultimately contributes to achieving superior accuracy and effectiveness in various applications across industries.
Applications of Ultrasonic Monitoring Equipment
The applications of ultrasonic monitoring equipment are vast and varied, impacting multiple sectors. Understanding its significance is crucial to appreciate how it enhances operational efficiency, safety, and environmental sustainability. This section highlights three main areas where ultrasonic technology shines: industry, healthcare, and environmental monitoring. By delving into these specific applications, one can grasp how the technology fits within modern exigencies and the benefits it offers.
Industrial Applications
In the industrial sector, ultrasonic monitoring plays a pivotal role in ensuring operational efficacy. One notable instance is in the realm of ultrasonic thickness measurements. Here, the equipment provides a reliable method to assess the thickness of materials such as metals and composites, which is essential for maintaining structural integrity. This is particularly vital in industries like oil and gas, where pipelines undergo routine inspections to prevent catastrophic failures. Regular ultrasonic checks can detect corrosion and wear, preventing costly downtime.
Moreover, ultrasonic flow meters offer a precise way to measure fluid flow in various configurations. The ability to provide real-time data makes it simpler to manage resources and streamline production processes. In addition, its non-intrusive nature means that installations can be made without interrupting ongoing operations, which is a clear boon for busy industrial sites.
Healthcare and Medical Diagnostics
Moving into healthcare, ultrasonic monitoring isn’t just beneficial; it’s often essential. The best-known application lies in diagnostic imaging, where ultrasound is utilized for a range of internal examinations. Healthcare professionals use ultrasonic devices to create images of soft tissues, organs, and even blood flow, making it invaluable for prenatal examinations and cardiac assessments.
An innovative application in this field is the use of ultrasonic therapy, where sound waves are applied to promote healing. This method can help in reducing inflammation and increasing circulation, making it a popular choice for physiotherapy. The speed and effectiveness of ultrasonic technology in medical diagnostics continue to pave ways for improved patient outcomes.
Environmental Monitoring
The environmental arena benefits greatly from ultrasonic technology as well. For instance, ultrasonic level sensors are widely adopted for monitoring water levels in rivers and lakes. The accurate readings they provide aid in flood prevention measures, which are becoming increasingly vital in our changing climate. By measuring ultrasonic signals reflected off the surface of the water, these devices offer continual data flow that supports timely decision-making.
In additional contexts, ultrasonic technology has found pathways into pollution monitoring, offering real-time data on gas emissions in industries. This ensures adherence to environmental regulations, ultimately promoting a cleaner and safer planet. The flexibility of applying ultrasonic methods across diverse environmental factors showcases its adaptability and critical nature.
In the landscape of technology, ultrasonic monitoring equipment stands tall, not only for its diverse applications but the immense impact it has on enhancing safety, efficiency, and sustainability across various domains.
Summary
In summary, the applications of ultrasonic monitoring equipment provide substantial benefits across industrial, healthcare, and environmental sectors. These tools not only enhance productivity but also contribute significantly to safety and well-being in society. As technology evolves, it will be fascinating to observe how these applications continue to expand, driving innovation and improvement in numerous fields.
Advantages of Ultrasonic Monitoring Systems
Ultrasonic monitoring systems have carved out a significant niche due to their distinctive benefits over traditional monitoring techniques. Understanding these advantages is pivotal, especially as industries push for enhanced efficiency and accuracy. Let's explore the core benefits these systems bring to the table.
Non-invasive Nature
One of the hallmark features of ultrasonic monitoring is its non-invasive nature. This means that while these systems are gathering vital data, they do not disturb the object or environment being monitored. For instance, in industrial applications, ultrasonic thickness gauges can measure how much material is left in a tank without needing to penetrate the surface. This is invaluable in industries where maintaining integrity is crucial, such as oil and gas, where even a small disturbance can lead to significant safety risks or operational downtime.
Moreover, in medical diagnostics, the use of ultrasound for imaging is well-known; it allows for the examination of organs without the need for invasive procedures. This attribute not only enhances patient comfort but also minimizes risk. Through its non-invasive capabilities, ultrasonic monitoring stands out as a preferred method across various sectors.
High Precision and Reliability
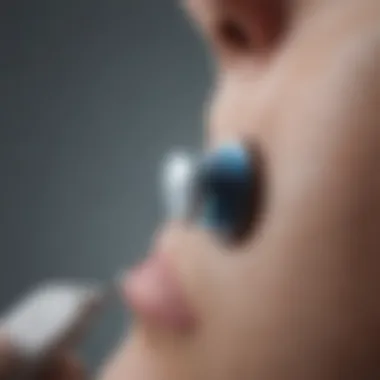
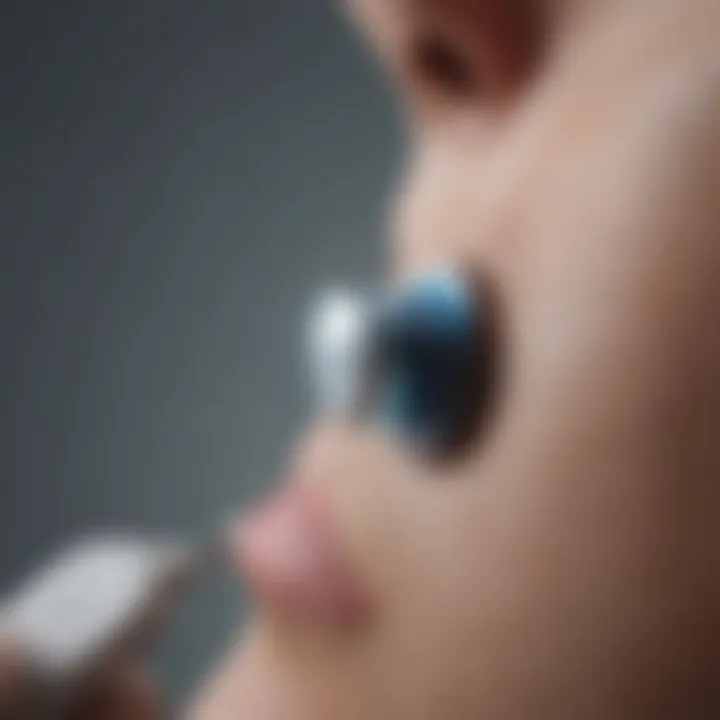
When it comes to precision, ultrasonic monitoring systems shine brightly. The technology relies on sound waves that can travel through various mediums, allowing for accurate measurements even in complex environments. For example, ultrasonic flow meters can provide precise flow rate readings in piped systems, which is instrumental for maintaining operational efficiency in manufacturing processes.
The reliability of these systems also cannot be overstated. In scenarios where consistent monitoring is necessary, ultrasonic devices often outperform their counterparts. They can function effectively in diverse temperature ranges and are less susceptible to common issues like electromagnetic interference. As a result, industries can rely on ultrasonic technology to deliver consistent and high-quality data, which is key to making informed decisions.
Cost-effectiveness in Long Term
While the initial investment in ultrasonic monitoring equipment may seem substantial, it’s essential to consider the long-term cost-effectiveness. Ultrasonic systems typically require less maintenance compared to traditional monitoring devices. Since they are non-invasive and often subject to fewer wear-and-tear issues, businesses can save significantly on both time and money in the long run.
Moreover, because of the precise data these systems provide, companies can anticipate failures before they occur, thereby reducing unexpected downtime and costly repairs. This predictive maintenance capability is particularly beneficial in sectors like manufacturing, where a lapse in operations can lead to substantial financial losses. By integrating ultrasonic technology, businesses optimize their investment and operational expenditures, making these systems not just beneficial but necessary.
"Ultrasonic monitoring systems are revolutionizing industries by providing unparalleled precision, reliability, and cost savings that traditional methods simply cannot match."
Challenges in Ultrasonic Monitoring
When diving into the world of ultrasonic monitoring, it’s crucial to acknowledge the hurdles one may encounter. These challenges often dictate the effectiveness and reliability of the ultrasonic systems in practical applications. Understanding these obstacles not only enhances the operation and implementation of these technologies but also ensures they can deliver on their promise of precision and efficiency.
Environmental Interference
Ultrasonic monitoring relies heavily on the transmission of sound waves through mediums. However, environmental factors can play a significant role in this transmission. For instance, varying temperatures and humidity can alter sound speed, leading to erroneous readings. The presence of background noise, both mechanical and natural, can interfere with the ultrasonic signals, causing inaccuracies in data collection.
Weather conditions, particularly heavy rain or snow, can also have a detrimental effect on readings from devices like ultrasonic level sensors. The sound waves might reflect off surfaces or be absorbed, misguiding the readings entirely. Addressing these potential interference issues often involves designing equipment that can filter out extraneous sound and adapt to environmental conditions, ensuring the data acquired is as accurate as possible.
Equipment Limitations
All equipment, no matter how advanced, has its limitations. In ultrasonic monitoring, these can manifest as restricted ranges or sensitivity levels based on the equipment's design and specifications. For example, ultrasonic thickness gauges are typically optimized for measuring specific materials. Using them on surfaces that produce erratic echoes can result in flawed measurements.
Furthermore, the technology may not be suitable for every type of application. In industrial settings, for instance, certain fluids or high-viscosity materials can hinder ultrasonic flow meters, leading to failure in accurate flow readings.
Another factor to consider is the need for ongoing maintenance. Regular calibration and sensitivity checks are necessary to keep the equipment functioning optimally; not doing so can leave it prone to errors due to time-dependent factors such as wear and tear or environmental changes.
Calibration Requirements
Calibration is the backbone of effective ultrasonic monitoring. Without proper calibration, even the most sophisticated systems can produce misleading or incorrect data. Each piece of ultrasonic equipment is built with precise measurements in mind; thus, neglecting calibration can lead to a range of issues from minor inaccuracies to complete operational failure.
Regular calibration ensures that devices function according to their specification, adjusting for any shifts in sensitivity or drift over time. Many ultrasonic flow meters, for example, require periodic recalibration to maintain measurement accuracy, especially in fluctuating operational conditions.
"Without a solid calibration routine, trust in ultrasonic measurements diminishes significantly—leading to inefficiencies and unforeseen complications."
To wrap things up, while ultrasonic monitoring opens doors to remarkable applications, it does not come without its challenges. By acknowledging and addressing environmental interferences, equipment limitations, and rigorous calibration requirements, users can enhance their experience and ensure they reap the full benefits of ultrasonic technology.
Recent Technological Advancements
Technological advancements in ultrasonic monitoring equipment not only enhance efficacy but also pave the way for groundbreaking developments across various fields. As industries continue to demand better efficiency with minimized downtime, the integration of cutting-edge technologies becomes vital. The following sections delve into key areas of progress in ultrasonic monitoring, particularly focusing on integration with the Internet of Things (IoT), the utilization of data analytics for predictive monitoring, and trends in miniaturization that are reshaping the landscape.
Integration with IoT
The Internet of Things is fundamentally transforming how ultrasonic monitoring equipment functions. By connecting devices to the internet, real-time data can be collected and analyzed, providing insights that were previously unattainable.
- Remote Monitoring: This capability allows operators to check system statuses from almost anywhere. For instance, a manufacturing plant can monitor machinery health without needing personnel on-site.
- Interactivity: IoT-integrated devices can communicate with each other, enabling automated responses to certain conditions, such as adjusting settings based on measured values to optimize operations.
- Data Collection: Continuous monitoring generates a wealth of data that can improve predictive maintenance strategies. Instead of waiting for a piece of equipment to fail, companies can analyze patterns to anticipate issues before they arise.
Due to these benefits, the synergy between ultrasonic monitoring systems and IoT technologies illustrates a promising direction for both efficiency and innovation.
Data Analytics and Predictive Monitoring
With the advent of big data, data analytics is becoming an indispensable ally for ultrasonic monitoring systems. Analyzing large datasets can uncover trends and anomalies that manual inspection might overlook.
- Predictive Maintenance: Using machine learning algorithms on data collected from ultrasonic sensors, companies can predict when equipment requires maintenance. This shifts the focus from reactive to proactive strategies, significantly lowering costs linked to equipment failures.
- Enhanced Decision Making: Real-time analytics support quick decision-making processes, safeguarding operations against delays.
- Continual Improvement: The feedback loop created through continuous learning allows industries to refine their monitoring processes and calibrate their equipment more effectively.
In essence, data analytics becomes the backbone of decision-making in environments where precision and reliability are paramount.
Miniaturization Trends
Product sizes getting smaller might initially seem trivial, but in the realm of ultrasonic monitoring, it signifies major breakthroughs.
- Compact Devices: Minimized size means these devices can fit into areas that previously would have posed challenges for traditional equipment. This is critical in industries like healthcare, where space is often limited.
- User Experience: Smaller designs can lead to simplified installation and maintenance processes. This directly affects the operational efficiency of businesses when integrating new equipment.
- Lower Costs: With advancements in technology reducing the cost of production for miniaturized devices, companies see significant cost benefits while maintaining performance levels.
Miniaturization not only facilitates versatility but also enhances accessibility, allowing more sectors to incorporate advanced ultrasonic monitoring solutions.
The rapid evolution of ultrasonic monitoring technologies marks a shift towards more intelligent, efficient, and flexible solutions, benefitting every layer of industry.
With these advancements, ultrasonic monitoring equipment continues redefining standards and streamlining processes across various domains. The path ahead promises even more innovations waiting to unfold.
Future Directions in Ultrasonic Monitoring
The field of ultrasonic monitoring is at a fascinating intersection of technology and evolving industrial needs. As industries strive for higher efficiency and sustainable practices, the potential for ultrasonic equipment to adapt and expand seems limitless. Looking ahead, the advancements in this technology open doors for various exciting applications and methodologies that could redefine standard operating procedures in multiple sectors.
Emerging Applications
One of the most significant trends is the expansion of ultrasonic monitoring into new sectors. Traditionally found in manufacturing and healthcare, its use is now being identified in areas like agriculture, where ultrasonic devices can help monitor soil moisture levels efficiently.
Moreover, in smart cities, these devices are expected to play a role in traffic and infrastructure management. For instance, ultrasonic sensors can be deployed to measure the flow of traffic or the condition of roadways, thus facilitating timely maintenance and enhancing safety. Another notable application is in the realm of renewable energy—specifically, wind turbine monitoring. Here, ultrasonic technology can assess blade integrity, ensuring optimal performance while preventing failures that might otherwise lead to outages.
Continuous Improvement in Sensor Technology
The evolution of sensor technology is another key element driving the future of ultrasonic monitoring. With developments in micro-electromechanical systems (MEMS), sensors are becoming smaller and more sensitive, allowing for better detection and resolution.
There is also an increasing integration of smart technology features, enabling sensors that can connect and communicate with other devices via the Internet of Things (IoT). This capability is revolutionary; it permits real-time data collection and remote monitoring, which is particularly valuable in preventative maintenance. For example, industries can use data analytics to predict equipment failures before they happen, saving time and costs associated with unscheduled downtime.
Role in Sustainable Practices
With environmental concerns overarching in today’s discourse, ultrasonic monitoring stands poised to support sustainable practices across various sectors. The technology’s non-invasive nature and precision in measurement make it ideal for applications aimed at reducing waste and improving resource management.
For instance, in the energy sector, ultrasonic flow meters can help in carrying out more effective energy audits, revealing areas where energy can be saved. Additionally, their application in environmental monitoring is invaluable, as they can track emissions levels in real time, allowing for immediate corrective actions.
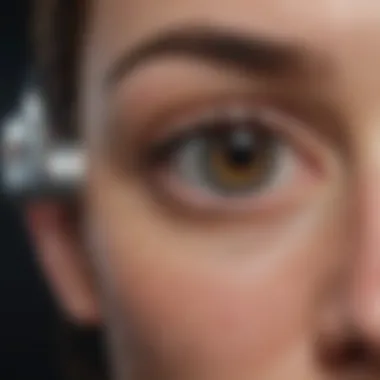
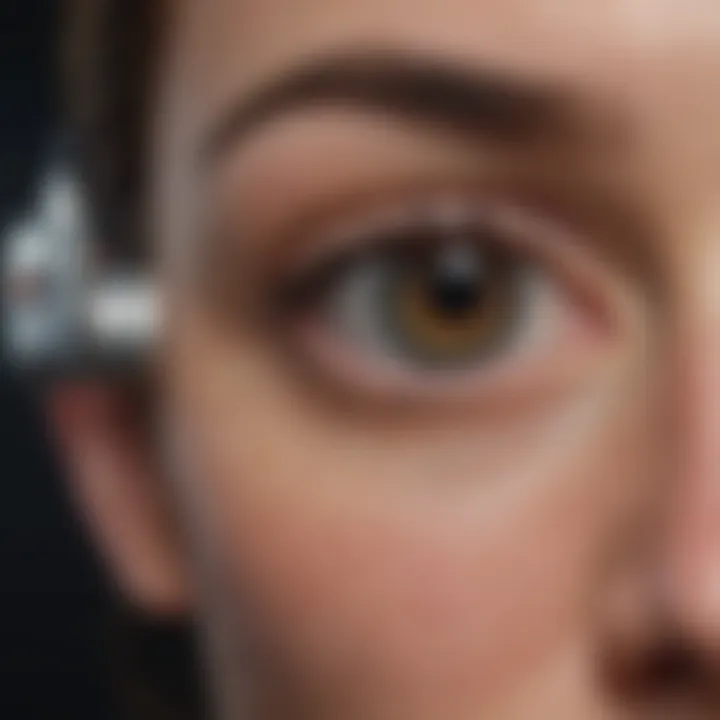
As a noteworthy example, companies that adopt ultrasonic monitoring technology to optimize resource use not only become more efficient but can also improve their public image by demonstrating a commitment to environmental stewardship.
"As ultrasonic monitoring evolves, its contributions could reshape industries toward a more sustainable future while enhancing efficacy and safety."
Comparison with Other Monitoring Technologies
In the rapidly advancing field of monitoring technologies, it’s crucial to explore how different methods stack up against one another. Ultrasonic monitoring equipment is increasingly making its mark but is it really the best option? A careful comparison can reveal its strengths and weaknesses relative to other technologies, and provide insight into practical applications across various domains.
Ultrasonic vs. Laser Monitoring
When we pit ultrasonic monitoring against laser monitoring, a few key distinctions are worth noting.
- Measurement Principles: Ultrasonic devices operate by sending high-frequency sound waves through a medium and measuring their return times. This method is particularly effective for non-invasive thickness gauging or flow measurement. In contrast, laser monitoring utilizes light beams to measure distance or detect movement, yielding high resolution and accuracy over longer distances.
- Application Scenarios: Ultrasonic equipment excels in environments where tangible materials are involved, which makes it a preferred choice in industries like manufacturing and construction for detecting flaws or weaknesses in materials. Laser monitoring, however, shines in precise distance and speed measurements, making it ideal for high-speed operations or long-range surveys, such as in geological studies or remote sensing of structures.
- **Limitations: ** One downside of ultrasonic monitoring is its dependency on the nature of the medium it interacts with. For instance, it may struggle in low-density environments or gases. On the other hand, laser systems, while quite precise, can be more affected by environmental factors like dust, fog, or rain, which can scatter or obstruct the laser beam.
In choosing between the two, one’s decision may come down to specific use cases. It’s like comparing apples and oranges; both have their merits but suit different tastes.
Ultrasonic vs. Electromagnetic Monitoring
Electromagnetic monitoring, which encompasses technologies like radio frequency identification (RFID) and electromagnetic flow meters, provides an alternative to ultrasonic methods. Here’s how they compare:
- Principle of Operation: Ultrasonic systems rely on sound waves while electromagnetic devices use electromagnetic fields. If the application requires measuring flows in conductive liquids, an electromagnetic flow meter can provide greater accuracy compared to ultrasonic measurement.
- Adaptability: One of the standout features of ultrasonic monitoring is its versatility in diverse environments. In contrast, electromagnetic systems might face challenges in non-conductive or lightweight materials where they yield poor results. This often limits electromagnetic technologies to specific applications in industries like oil and gas, where only conductive media is involved.
- Cost Considerations: Generally, ultrasonic equipment can be more cost-effective in terms of initial investment and maintenance over time compared to electromagnetic systems, particularly in scenarios requiring extensive monitoring capabilities.
Each technology has its own particular set of advantages. The choice often hinges on logistical and environmental considerations, as well as the specific parameters to be measured.
"In the world of technology, the best tools are those that suit the task at hand. Making an informed decision requires understanding not solely how these systems work, but wherein lies their respective strengths and limits."
A thoughtful evaluation of these monitoring methodologies allows industrial professionals and researchers alike to select the optimal technology for their specific needs and conditions.
Understanding Regulations and Standards
Understanding regulations and standards in the field of ultrasonic monitoring equipment plays a crucial role in ensuring that devices perform their intended functions reliably and safely. As industries increasingly rely on this technology, it becomes imperative to adhere to guidelines that define best practices for operation and design. Not only do these regulations improve the credibility of manufacturers, but they also bolster consumer confidence by guaranteeing that equipment meets certain performance benchmarks.
Industry Standards Overview
Several industry standards guide the development and implementation of ultrasonic monitoring systems. Organizations such as the International Organization for Standardization (ISO), American National Standards Institute (ANSI), and various national bodies set regulations that dictate the manufacturing processes, quality control, and testing procedures for these devices. Here are some key standards:
- ISO 9001: This standard focuses on quality management systems, ensuring consistent quality in products and services.
- ISO 3382: Pertaining specifically to acoustics, this standard provides measurement techniques for the evaluation of auditory environments, which is key for ultrasonic monitoring.
- ASNT SNT-TC-1A: This guideline is applicable to ultrasonic testing and lays out the qualifications required for personnel involved in non-destructive testing.
These standards not only ensure the accuracy and reliability of ultrasonic equipment but also streamline compatibility and interoperability between different technologies used across industries.
Safety Regulations in Usage
Safety regulations are another critical aspect when considering ultrasonic monitoring systems. Operators must be informed about safe practices to mitigate risks associated with ultrasonic exposure and equipment functioning. Key considerations include:
- Operator Training: Personnel should be trained in proper equipment handling and maintenance to avoid accidents.
- Personal Protective Equipment (PPE): Depending on the operational environment, specific PPE might be necessary, such as hearing protection if exposure levels are deemed excessive.
- Regular Maintenance: Adhering to manufacturers’ guidelines for regular maintenance and calibration helps ensure that the equipment operates correctly, safeguarding against malfunctions that could lead to hazardous situations.
Implementing these safety measures not only protects staff but also enhances the overall effectiveness of ultrasonic monitoring systems, ensuring they serve their purpose without undue risk.
"Standards and regulations are the backbone of reliability in ultrasonic monitoring, providing a roadmap for safe and effective implementation."
By understanding and adhering to these regulations and standards, organizations can leverage ultrasonic monitoring equipment with greater confidence, ensuring optimal performance while safeguarding their personnel and investments.
Case Studies of Ultrasonic Monitoring Implementations
Exploring case studies of ultrasonic monitoring implementations sheds light on real-world applications and outcomes, illustrating how this technology shapes industries in practical ways. By diving deep into specific examples, stakeholders can understand not just the technology's potential but also its tangible benefits and considerations when integrating such equipment into their operations.
Engineering Sector Applications
The engineering sector has been a forerunner in adopting ultrasonic monitoring technologies. Its applications range widely, from infrastructure health to manufacturing processes. For instance, let’s consider the monitoring of bridge integrity. Engineers utilize ultrasonic thickness gauges to measure wall thicknesses of key structural components.
- Benefits of Ultrasonic Monitoring in Engineering
- Early Detection of Defects: Ultrasonic methods can spot internal flaws long before they lead to catastrophic failures.
- Cost-Effective Maintenance: Regular monitoring using ultrasonic devices allows for planned maintenance instead of reactive repairs.
- Non-Destructive Testing (NDT): The non-invasive nature means there’s minimal disruption to ongoing operations.
A notable case involved the monitoring of a water treatment facility's piping system. Using ultrasonic flow meters, engineers monitored flow rates to identify areas where sediment buildup might occur, potentially preventing clogs and ensuring the system operates smoothly. The ultrasonic flow meters provided real-time data that enhanced operational efficiency and extended the lifespan of the equipment.
Healthcare Implementations
In the healthcare sector, ultrasonic monitoring is pivotal for diagnostics and patient care. Ultrasonography, primarily used for imaging and monitoring internal body structures, has transformed early disease detection and treatment follow-ups.
For example, a prominent case in ultrasound technology is in prenatal care. Expectant mothers undergo routine ultrasounds to monitor fetal development. This practice not only reassures parents but also helps healthcare providers catch potential abnormalities early on.
- Impact on Patient Care:
- Enhanced Diagnostic Precision: High-resolution ultrasound images allow for accurate assessments.
- Safety: As a non-invasive method, it minimizes risk to both mother and fetus compared to other imaging techniques.
- Real-time Feedback: Physicians can provide immediate insight during consultations.
One interesting implementation studied the usage of ultrasound in vascular health. A specific hospital integrated ultrasonic Doppler devices to assess blood flow in patients with vascular diseases. This approach led to improved diagnosis and treatment plans by delivering timely results, which were crucial for effective interventions.
"Ultrasonic monitoring in healthcare isn't just about technology; it's about enhancing human life and well-being."
Through these case studies, it becomes apparent that ultrasonic monitoring equipment serves crucial roles across diverse fields, enabling industries to become more efficient, cost-effective, and proactive. The real-world implications are profound, painting a picture of the future where such technologies become standard practice across various applications.
Culmination
The conclusion of this article weaves together the threads of various discussions, reinforcing the significance of ultrasonic monitoring in multifarious industries. This technology is not only pivotal in enhancing efficiency and accuracy but also plays a crucial role in safety and sustainability initiatives. Its inherent advantages, such as non-invasive assessment and high precision, have cemented its place as a vital tool for today’s demands in various sectors, from manufacturing to healthcare.
Summarizing Key Insights
To recap, the exploration delved into crucial facets of ultrasonic monitoring equipment, revealing several key insights:
- Diverse Applications: This technology finds application in various fields, ranging from industrial settings to medical diagnostics. Understanding the specific use cases helps professionals identify the most suitable equipment for their needs.
- Operational Mechanisms: A solid grasp of how ultrasonic devices function gives clarity to their effectiveness. The article detailed the transducer functionality and signal processing techniques that underpin these devices.
- Technological Advancements: Recent trends like IoT integration and predictive analytics indicate a promising future, expanding the horizon for potential applications.
- Importance of Regulations: Following industry standards and safety regulations ensures the reliability of ultrasonic monitoring equipment, safeguarding not only the devices themselves but also the environments in which they operate.
These reflections serve as a foundation for both new entrants and seasoned professionals in understanding and leveraging the benefits of ultrasonic monitoring technology.
Call for Future Research
Looking ahead, there’s an apparent need for continued exploration and innovation within the realm of ultrasonic technology. Notable areas for future research include:
- Improvement in Sensor Sensitivity: Developing sensors capable of detecting smaller anomalies could expand the applications of this technology even further.
- Integration with Advanced Data Analytics: As data-driven decisions become commonplace, enhancing the analytical capabilities associated with ultrasonic equipment could help derive deeper insights.
- Sustainability Practices: Exploring how ultrasonic monitoring can contribute to environmental sustainability will be instrumental. This involves assessing material usage and energy efficiency in developing these devices.
By pursuing these avenues of research, we can harness the full potential of ultrasonic technology to meet future challenges across diverse industries. The collective efforts in innovation and application can forge a new frontier, ensuring that ultrasonic monitoring not only evolves but continues to provide unmatched reliability and precision for various needs.