Exploring Reciprocating Motors: Functionality and Trends
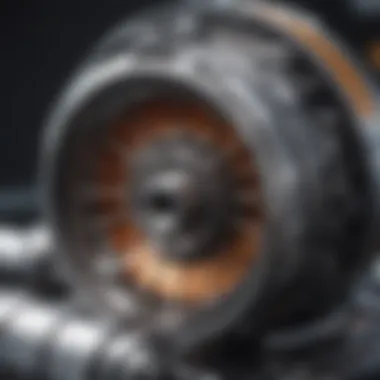
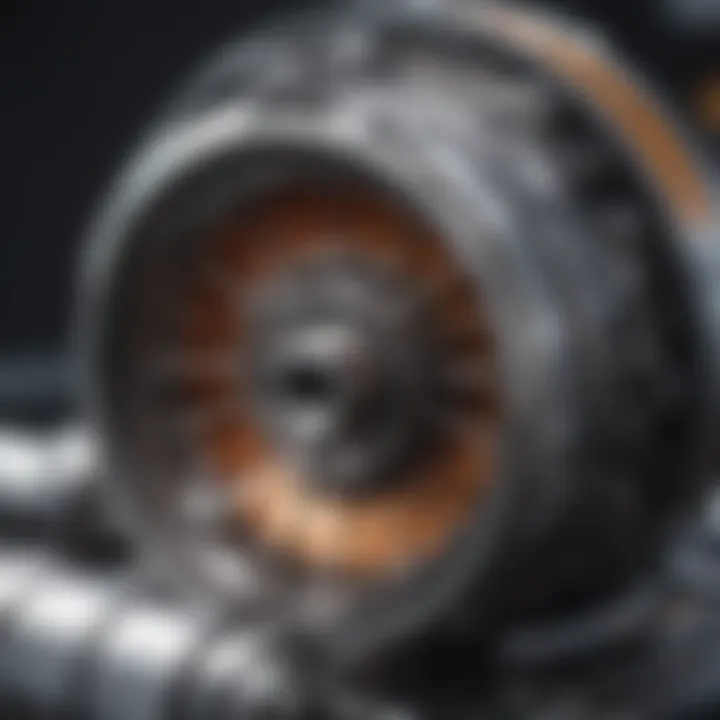
Overview of Research Topic
Brief Background and Context
Reciprocating motors, often referred to as piston engines, hold a significant place in the history of mechanical engineering. These devices are fundamentally designed to convert linear motion into rotational force, allowing them to drive various machinery and vehicles. Originating in the 17th century with the advent of steam engines, the principles behind reciprocating motion have evolved, yet the core concept remains largely the same. The efficiency and versatility of these motors have made them indispensable in numerous sectors including automotive, aviation, and power generation.
Importance in Current Scientific Landscape
As industries increasingly pivot toward sustainability, the relevance of reciprocating motors cannot be overstated. They are often at the forefront of discussions regarding energy efficiency and emissions. With recent innovations integrating advanced materials and control systems, the potential for these motors to meet the stringent demands of modern engineering is promising. Furthermore, their ability to run on a variety of fuels—from traditional gasoline to biofuels—makes them an essential player in the transition towards greener energy solutions.
Methodology
Research Design and Approach
The exploration of reciprocating motors requires a comprehensive approach that intertwines theoretical research with practical applications. This study synthesizes literature from various scientific journals, technical reports, and industry analyses. By examining both historical and contemporary use cases, insights into operational efficiencies and technological developments are drawn. Consideration is also given to comparative analyses with other motor types, providing a well-rounded view of their position within the mechanical landscape.
Data Collection Techniques
Data for this examination is gathered from various reputable sources including:
- Peer-reviewed journals on mechanical and automotive engineering.
- Industry reports that outline the latest trends and innovations.
- Technical specifications from manufacturers detailing key performance metrics.
- Academic databases such as JSTOR and IEEE Xplore for research articles that delve deeper into specific aspects of reciprocating motors.
Through a combination of qualitative and quantitative research methods, this article aims to provide a robust understanding of reciprocating motors, accentuating their principles, applications, and the innovations reshaping their future.
"The development of reciprocating motors serves as a testament to human ingenuity in engineering, reflecting both our challenges and triumphs in harnessing energy."
By illuminating the nuances of these motors, this article endeavors to engage students, researchers, educators, and professionals, ultimately contributing to the ongoing dialogue around mechanical innovation and sustainability.
Preface to Reciprocating Motors
Understanding reciprocating motors is indispensable for anyone engaged in modern mechanical design and engineering. These devices are fundamental in converting energy into mechanical work, giving life to a wide array of applications—be it in automobiles, industrial machinery, or even aviation. With the constant evolution of technology, there is a pressing need to grasp their principles, uses, and the innovations that are shaping their future. This section will provide a pathway into the world of reciprocating motors, emphasizing the core concepts that underpin their operation.
Definition and Basic Concepts
At their essence, reciprocating motors transform linear motion into rotational motion. This is achieved by a system of components that includes pistons, cylinders, and crankshafts. The pistons move in and out of cylinders, driven by the combustion of fuel, which generates pressure. This pressure pushes the pistons, which ultimately turns the crankshaft, creating rotational energy. The simplicity of their basic operation belies the intricacy involved in their design and execution. To put it plainly, reciprocating motors leverage the power of controlled explosions to produce useful work.
Understanding a few key terms is crucial:
- Piston: The moving component that creates compression within the cylinder.
- Crankshaft: This part converts the linear motion of the piston into rotational energy.
- Cylinders: Encasements that house the pistons and dictate their movement.
These components work together to form a cycle of intake, compression, power generation, and exhaust, set out in a sequential manner that underlines the operational efficiency of these motors.
Historical Development
The journey of reciprocating motors traces back to the 17th century, a timeline peppered with experimentation and innovation. One of the early prototypes was the atmospheric engine, developed by Thomas Newcomen in the early 1700s. This was a significant leap, harnessing steam to drive a piston. Following this, in the 19th century, Nikolaus Otto invented the four-stroke engine, which revolutionized motor design, leading to wide-scale adoption in various industries.
The evolution continued with advancements in fuel type and technology, such as the introduction of diesel engines by Rudolf Diesel. Over time, these engines became more efficient and reliable, adapting to the demands of the automotive industry. The historical trajectory of reciprocating motors reveals not only technological progress but also the changing needs and challenges faced by engineers throughout the ages.
"Innovation in reciprocating motors has always mirrored the pace of societal and industrial change—driving forward our understanding of energy use and efficiency."
In summary, the history of reciprocating motors underscores their importance in modern society, showcasing a timeline filled with ingenuity and practical application. Each step in this evolution has shaped the motors we rely on today, making it crucial for professionals in the field to remain informed of these developments.
Operational Mechanism
Understanding the operational mechanism of reciprocating motors is crucial as it lays the foundation for their functionality and efficiency. These machines convert fuel energy into mechanical energy, relying on a well-orchestrated series of movements and processes. By delving into the specifics of each component and the cycles they undergo, we can appreciate how intricate engineering principles can yield substantial power output while grappling with challenges like efficiency and environmental impact.
Basic Components
Piston
The piston in a reciprocating motor serves as a critical component, forming the main part of the combustion chamber. It undergoes rapid movement within the cylinder, driven by the energy release from fuel ignition. A key characteristic of the piston is its ability to withstand high pressure and temperature environments without deforming. This durability makes aluminum alloys a common choice for manufacturing pistons, offering a favorable weight-to-strength ratio.
However, a unique feature of pistons is their necessity for precise fit in the cylinder to prevent leaks and ensure optimal performance. While there is clear advantage to using lightweight materials, a misfit can lead to increased wear and lead to performance drop-offs. Hence, the meticulous alignment during assembly is paramount.
Cylinder
The cylinder provides the fixed environment where the combustion process occurs. Its importance can't be overstated as it directly influences the volume of air-fuel mixture available for combustion. Typically crafted from cast iron or steel, cylinders are designed to handle the thermal stresses of repeated cycles. A major characteristic is often their bore diameter; larger bore can lead to increased power, but may also introduce complexity in terms of cooling.
The unique aspect of cylinders is their designs, such as square or oversquare configurations, which affects engine performance. Each configuration offers its own set of advantages, like enhanced power delivery or torque characteristics, making the choice critical based on the intended motor application.
Crankshaft
The crankshaft is another structural cornerstone of reciprocating motors, converting the linear movement of the piston into the rotational motion required to drive various machinery. A strong yet lightweight material like forged steel is typically used, contributing to a key characteristic of durability while ensuring efficient energy transfer.
An important feature of crankshafts is their design variations depending on the engine type, such as counterweighted designs aiding in smoother operation at higher speeds. However, crankshafts can face significant stress during operation – particularly in high-performance engines – which can lead to failures if not properly engineered.
Connecting Rod
The connecting rod links the piston and crankshaft, transforming the linear piston motion into rotational power. Its design can influence the overall efficiency and responsiveness of the motor. A notable characteristic is its length; longer rods can help reduce side loads on pistons which may extend their lifespan.
It's interesting to note that aluminum alloy connecting rods are gaining traction for their lighter weight, but they can pose some limitations under high-stress scenarios, potentially leading to fatigue over time. So, the choice of connecting rod material and design has to align with the engine's performance goals, balancing durability and weight carefully.
Thermodynamic Cycles
Otto Cycle
The Otto Cycle is a predominant thermodynamic cycle used in gasoline engines, crucial for understanding how reciprocating motors achieve power generation. A vital aspect of this cycle is its efficiency as it employs a constant volume process, maximizing energy extraction from the fuel. This cycle typically has a significant compression ratio, allowing for more power to be harnessed from less fuel, making it a popular choice in light automotive applications.
What sets the Otto Cycle apart is its smooth power delivery resulting from the continuous nature of the combustion process. However, the downside is the sensitivity to fuel octane levels; lower quality fuels can lead to knocking which hampers performance and efficiency.
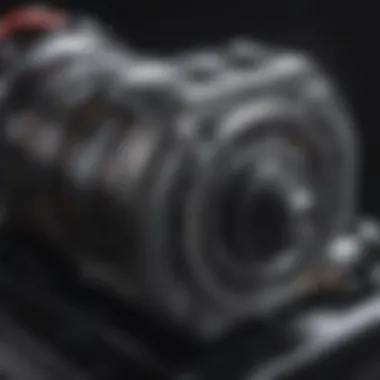
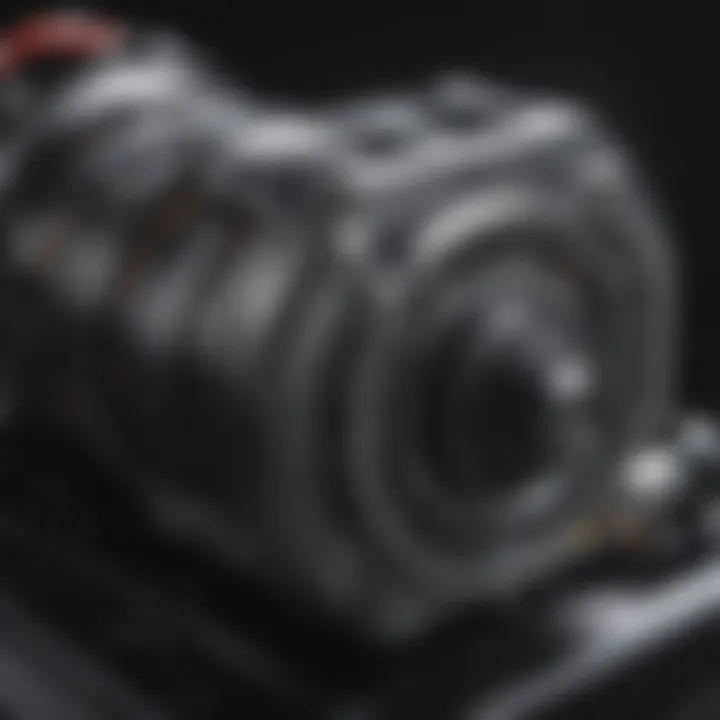
Diesel Cycle
The Diesel Cycle, predominant in many heavy-duty applications, operates on a principle that favors compression ignition. This cycle is noteworthy due to its inherently higher thermal efficiency compared to the Otto Cycle, thanks in part to the higher compression ratios and the absence of spark plugs. A key characteristic of the Diesel Cycle is its fuel flexibility, allowing it to use a range of diesel fuels.
One unique aspect of the Diesel Cycle's design is the longer stroke lengths it allows, resulting in greater torque at lower RPMs. However, challenges like higher emissions and noise levels present trade-offs that must be managed, particularly in applications with stringent emissions regulations.
Operation Stages
Intake
The intake stroke marks the beginning of the cycle, where the mixture of air and fuel enters the cylinder. This stage is pivotal as it sets the foundation for combustion. A critical characteristic of the intake process is the design of the intake manifold, which can greatly affect the gas flow dynamics and, by extension, the overall engine performance.
What makes the intake stage unique is its dependence on atmospheric pressure and engine speed. At higher speeds, the intake system needs to work efficiently to ensure that enough mixture enters the cylinder, thereby necessitating careful tuning for optimal performance.
Compression
This stage compresses the air-fuel mixture, elevating its pressure and temperature, preparing it for combustion. A significant characteristic of the compression stroke is the compression ratio, which directly influences engine performance and fuel efficiency. Higher compression ratios can lead to better efficiency, but they also demand higher octane fuels to avoid knock.
The unique challenge here lies in balancing compression ratio and fuel quality. Too high a ratio may lead to pre-ignition, which can be detrimental to performance and engine longevity.
Power Stroke
The power stroke is the heart of the engine cycle, marked by the ignition and the resulting combustion. This is where the energy needed to produce work is generated. A defining characteristic of this stage is the pressure surge resulting from combustion, which pushes the piston down during this phase.
An interesting feature of the power stroke is its timing; optimizing the ignition timing can significantly impact overall power output and efficiency. However, mismanagement of this timing could lead to issues like backfiring or incomplete combustion, reducing performance efficiency.
Exhaust
Finally, the exhaust stage allows for the expulsion of burnt gases from the cylinder. A key aspect of this phase is the design of the exhaust system, as it must minimize backpressure to enhance engine performance.
One notable feature is the use of turbochargers in the exhaust system, which can harness leftover exhaust energy to improve intake airflow, thereby enhancing the overall cycle's efficiency. However, a potential disadvantage is the complexity added to the system, which can entail increased maintenance and potential points of failure.
In summation, understanding the operational mechanisms of reciprocating motors sheds light on their functionality and diverse applications. From the interplay of components to the depth of thermodynamic cycles, every stage contributes to the remarkable power they offer in various applications.
Types of Reciprocating Motors
Understanding the various types of reciprocating motors is crucial since each design caters to specific applications, optimizing performance based on the intended use. Different configurations, such as single and multi-cylinder motors, come with their own strengths and drawbacks. This section will explore each type, diving into their distinctive characteristics and appropriate uses.
Single Cylinder Motors
Single cylinder motors are straightforward and generally easier to maintain. These motors operate with one cylinder, whereby one piston is connected to a crankshaft. The lack of complexity in design contributes to lower manufacturing costs and simplicity in mechanics. A notable advantage is their lightweight, making them ideal for portable applications such as small generators and motorcycles.
However, single cylinder motors can struggle with vibrations and engine imbalance, leading to noise issues and a rougher ride in vehicles. Although they are beneficial for certain tasks, their power output is limited compared to multi-cylinder options.
Multi-Cylinder Motors
Multi-cylinder motors enhance performance by having more than one cylinder, enabling greater power output while distributing the workload. This type can be further divided into three main configurations: inline, V-type, and opposed.
Inline
Inline motors are one of the most popular types in the automotive world. They feature cylinders arranged in a straight line, promoting efficient use of space. A key characteristic of inline engines is their ability to provide smooth power delivery and good fuel efficiency. Additionally, the design simplifies the manufacturing process, which often leads to lower costs and easier repairs.
A unique aspect of inline motors is how they allow for a longer stroke length. This can contribute to better torque at lower RPMs, making them ideal for everyday vehicles. However, a disadvantage includes a longer and potentially heavier engine configuration, which may not be suitable for all designs, particularly in compact cars.
V-Type
V-type engines stand out due to their compact design where cylinders are arranged in two banks at an angle, typically forming a "V" shape. This configuration provides a strength-to-weight advantage, allowing for powerful engines that fit into more compact spaces. The performance of V-type engines is generally more robust, making them popular in high-performance vehicles and racing applications.
Nevertheless, one must consider that V-type engines can have a more complex design, leading to potentially higher maintenance costs. Cooling and lubrication also require more attention, as these engines generate considerable heat, making periodic checks essential to ensure longevity.
Opposed
Opposed engines, sometimes called boxer engines, have their cylinders arranged horizontally, opposite from each other. This unique arrangement offers a lower center of gravity, which improves overall vehicle stability and handling – a key factor for sports cars and performance vehicles. The symmetrical layout leads to balanced operation, and vibrations are often minimized compared to inline engines.
A specific feature of opposed engines is their efficiency, especially noted in vehicles like Subaru models and certain Porsche vehicles. Despite their advantages, challenging aspects involve a more intricate construction process, as well as limited space for some designs, which can hinder various application scopes.
Rotary Engines
Rotary engines differ significantly from traditional reciprocating designs. Instead of pistons, they use a triangular rotor that moves through a fixed housing. This design results in fewer moving parts, ultimately contributing to lighter weight and fewer vibrations. The compact nature suits this type for specialized applications, such as in certain Mazda vehicles. However, rotary engines can face challenges regarding fuel consumption and engine heat. Their unique design may be better for specific scenarios but can struggle with widespread applications compared to conventional motors.
Applications of Reciprocating Motors
The role of reciprocating motors extends far beyond their basic mechanical principles, resonating through various sectors that drive our modern world. Understanding where these motors find their utility illuminates their significance in engineering and technology. Not only do they provide essential power, but their diverse applications highlight their adaptability and innovation over the years.
Automotive Industry
One prominent domain for reciprocating motors is the automotive sector. As the heartbeat of countless vehicles, reciprocating engines power everything from compact cars to heavy-duty trucks. Engine design in this field typically showcases multi-cylinder configurations, allowing for optimized power delivery and efficiency. The familiar sound of an engine revving evokes a sense of excitement, and that’s because reciprocating motors enable rapid acceleration and smooth handling.
Key Benefits:
- Fuel Efficiency: These motors can be finely tuned for fuel performance, adapting to various driving conditions.
- Versatility: Whether gasoline or diesel, reciprocating motors cater to different fuel types, offering flexibility for manufacturers and consumers alike.
Additionally, the motors' design allows for easy maintenance and repairs—an essential aspect considering the millions of vehicles on the roads. It’s no surprise that as technology advances, automakers are also exploring hybrid models that merge traditional reciprocating engines with electric systems, aiming for reduced emissions and better environmental performance.
Aerospace Sector
In the aerospace sector, reciprocating motors exhibit their prowess through applications in smaller aircraft and general aviation. While turbofans and turbojets often dominate commercial aviation, reciprocating engines are particularly noteworthy in light aircraft and drones, where their power-to-weight ratio becomes advantageous.
Considerations:
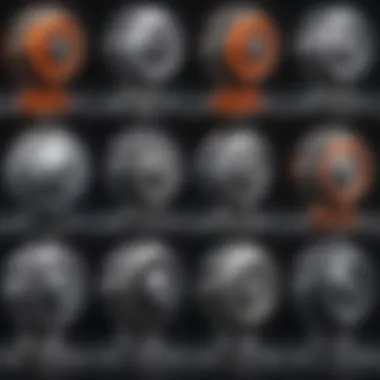
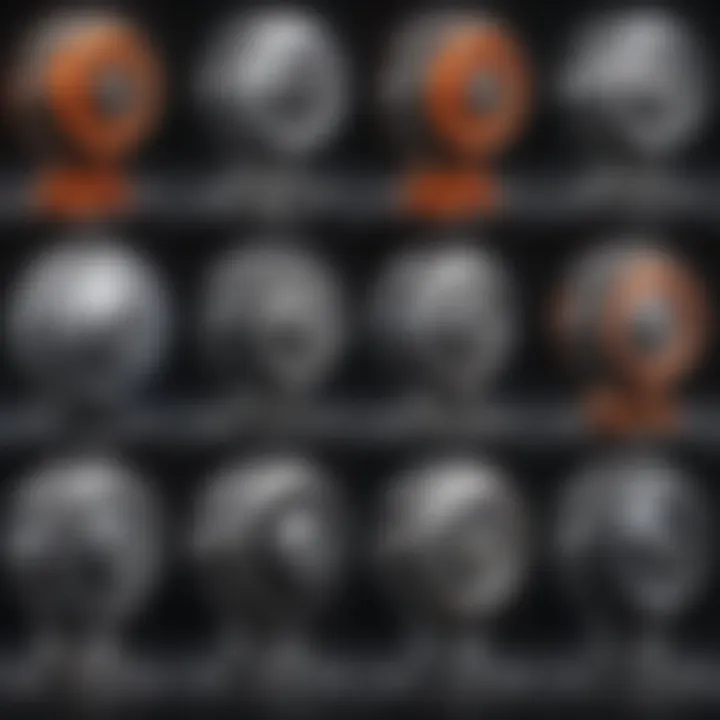
- Reliability: The simplicity of reciprocating motors translates into fewer components, which enhances reliability—a crucial aspect when safety is non-negotiable.
- Cost-Effectiveness: For pilot training and recreational flying, the lower operating costs associated with reciprocating engines make them a favored choice.
Some aircraft, such as the Cessna 172, showcase the benefits of these power plants with proven performance records, invaluable in training scenarios. Thus, the aerospace industry continues to appreciate the contributions of reciprocating motors, primarily emphasizing their desirability in niche markets.
Industrial Machinery
The industrial landscape also benefits significantly from reciprocating motors ranging from small-scale operations to large manufacturing facilities. In these settings, these motors drive complex machinery essential to production lines and manufacturing processes. From pumps to compressors, reciprocating designs excel in various applications that require varying pressure and flow rates.
Notable Uses Include:
- Compressors: Often used in refrigeration and air conditioning systems, reciprocating compressors efficiently compress gases, helping to maintain ideal temperature conditions.
- Pumps: Hydraulic and pneumatic pumps with reciprocating designs enable precise fluid movement necessary in many industrial processes.
The robustness and durability of these motors in harsh working environments are unmatched, often leading to prolonged operational lifespans and reduced downtimes.
Marine Applications
In marine engineering, reciprocating motors shine in several applications, particularly in small boats and some large vessels where their reliability and performance are unparalleled. These motors power everything from fishing boats to yachts, providing the thrust needed to navigate both calm and rough waters.
Advantages in Marine Use:
- Ease of Repair: Given that marine engines work in highly corrosive environments, the simplicity of reciprocating motors can make them easier to repair and maintain during seasonal check-ups.
- Fuel Economy for Long Voyages: The efficiency of reciprocating motors contributes to better fuel management, a critical factor for long-distance marine travel.
Furthermore, diesel engines in marine settings often employ reciprocating designs, given their robust performance in high-stress conditions and substantial torque characteristics, making them well-suited for heavy-load operations.
"Reciprocating motors, while not the headline stars of our machinery, are undeniable workhorses, supporting a wide array of industries with their flexibility and improved efficiency."
In summary, the applications of reciprocating motors span various critical sectors, reinforcing their value beyond mere functionality. Each industry capitalizes on specific characteristics, fostering continued advances in design and efficiency, thus cementing their legacy in the machinery world.
Performance Metrics
In the assessment of reciprocating motors, performance metrics provide a crucial lens through which engineers and designers can evaluate their functionality and efficiency. An understanding of these metrics is not just academic; they inform practical decisions in design and application, enhancing the motor's overall effectiveness. Specific elements of performance metrics can have a significant impact on longevity, cost, and energy consumption, all of which resonate in various industrial applications. By meticulously analyzing these metrics, one can determine the best choice for specific operational demands, leading to improved outputs and lower environmental impact.
Power Output
Power output is one of the central metrics in evaluating the effectiveness of a reciprocating motor. This figure represents the motor's ability to perform work. It's calculated based on both the torque produced and the speed at which the motor operates. When one thinks of a sports car zooming down the highway, the relationship between power output and performance becomes crystal clear. High output often correlates with better acceleration and operational speed, which is why it is such a prized attribute in automotive applications and machinery.
The measurement of power output isn't just about sheer numbers; it translates into real-world capability. For instance, a construction machine that can generate substantial power output can complete tasks faster than its less powerful counterparts, saving time and cost on projects. Proper calibration and regular maintenance of the motor can also result in optimized power output. Failure to address these needs may lead to diminished performance over time.
Efficiency Ratings
Efficiency ratings play a pivotal role in determining how effectively a reciprocating motor converts fuel or energy into useful work. A motor with high efficiency ratings consumes less fuel while still delivering the required power output. This efficiency has substantial implications for operational costs, particularly in fields like transportation where fuel expenses are a significant concern.
Consider, for example, a diesel engine used in long-haul trucking. The efficiency of the engine directly affects fuel costs over the lifespan of the vehicle. A motor that achieves better efficiency can extend operation durations between refueling, ultimately improving logistical effectiveness and reducing environmental emissions. The metrics that underpin efficiency ratings include thermal efficiency and mechanical efficiency, making these assessments essential in both design and operation.
Torque Characteristics
Torque characteristics illuminate how well a reciprocating motor can perform under various loads and conditions. Torque refers to the rotational force produced by the engine and is essential for moving heavy loads or climbing hills. In practical terms, consider a truck loaded with goods; having a motor with adequate torque characteristics allows it to start moving smoothly from a standstill, even under heavy load.
Moreover, evaluating torque at different RPMs (revolutions per minute) can offer insights into how the motor behaves in diverse scenarios. For instance, peak torque may be needed for initial acceleration, while steady torque is crucial for maintaining speed. This makes a comprehensive understanding of torque characteristics vital when designing engines for specific applications, whether for racing, agriculture, or marine engines.
"Understanding performance metrics can be the difference between an engine that underperforms and one that consistently meets or exceeds expectations."
Challenges and Limitations
The role of reciprocating motors in various industries is undeniable. However, it's important to navigate the challenges and limitations that accompany their use. These hurdles not only affect performance and reliability but also define their suitability for certain applications. Addressing these challenges is essential for enhancing the longevity and efficiency of these motors, making it a vital topic for students, researchers, and professionals alike.
Maintenance Requirements
Reciprocating motors, with their intricate designs, come with a set of maintenance requirements that cannot be overlooked. Keeping these engines in prime condition necessitates a regular check-up routine. Engine oil must be changed at specific intervals to avoid wear and tear on the piston rings and cylinder walls. Another crucial element is the tightening and adjustment of various bolts and nuts that secure key components.
A common problem arises with the need to periodically replace moving parts, such as the connecting rod bearings, which can wear out due to friction and heat. Ignoring these issues can lead to more severe complications, potentially crippling the motor's performance. Thus, the recommendation is to implement a preventive maintenance schedule based on the manufacturer's guidelines, ensuring that operations run smoothly. This way, the key benefits of durability and performance are maintained, significantly reducing the risk of unexpected downtime.
Environmental Considerations
In an era where environmental consciousness is paramount, the impact of reciprocating motors on nature can't be brushed under the carpet. These motors often rely on fossil fuels, which contribute to greenhouse gas emissions. This is a significant concern, especially as industries face increasing pressure to minimize their carbon footprints.
Efforts are being made to integrate cleaner technologies with traditional motors. For instance, the use of biofuels is gaining traction. However, while biofuels appear to be a greener alternative, the transition still faces headwinds, such as land use implications and energy conversion efficiency.
Furthermore, noise pollution generated by these engines is another environmental drawback. In urban settings, the loud rumble of a gasoline engine can be bothersome. Therefore, engineers are continuously working on noise reduction technologies which can mitigate this issue, contributing to a more sustainable operation of these motors.
Performance Under Different Conditions
Reciprocating motors are designed to perform optimally in specific conditions, but they can struggle when those conditions shift. Factors such as temperature, altitude, and fuel quality can have significant effects on motor efficiency.
For example, at higher altitudes, the air density is lower, which influences the air-fuel mixture entering the cylinders. This leads to reduced power output, often leaving the engine feeling sluggish, especially in single-cylinder configurations. To counter this, motor tuning becomes essential. Tuning can adjust the fuel-air mix, but not all motors allow for such modifications.
Similarly, extreme temperatures can affect the viscosity of lubricants, making it harder for components to move smoothly. In cold weather, motor fluids thicken, causing increased wear during startup. Careful consideration of engine oil viscosity and the selection of appropriate fluids for the operating environment is crucial.
"Understanding the limitations of reciprocating motors helps in planning efficient and sustainable operations."
In summary, recognizing the challenges associated with reciprocating motors provides a foundation for improvement. Whether through regular maintenance practices, addressing environmental concerns, or acknowledging performance fluctuations, being proactive can make a world of difference. For those engaged in this field, these insights not only enhance knowledge but also inspire innovation.
Technological Innovations
In the realm of reciprocating motors, the advances in technology have not just added bells and whistles; they've fundamentally shifted the paradigms of efficiency and functionality. These innovations are essential to understanding how these motors can be utilized more effectively, as well as how they can be adapted to meet modern demands. Each technological leap brings with it promising benefits while raising vital considerations that deserve attention.
Fuel Type Diversification
One of the key innovations in the field of reciprocating motors is the diversification of fuel types. Traditional motors often ran solely on gasoline or diesel, leading to limited options for energy users. However, advances have led to the development of motors capable of using a slew of alternatives such as biofuels, compressed natural gas (CNG), and even hydrogen. This flexibility allows for:
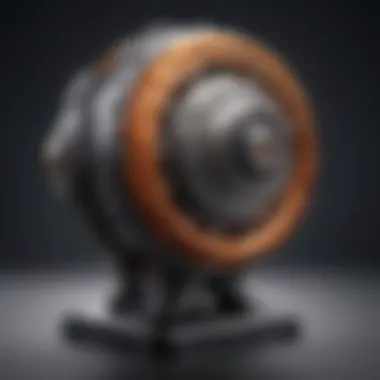
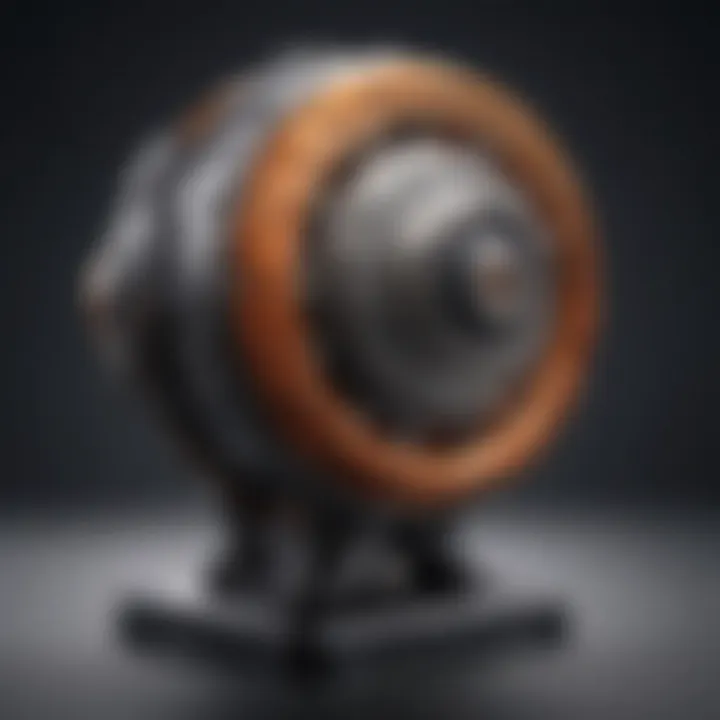
- Enhanced Efficiency: Different fuels carry varying energy densities, meaning motors can be optimized for performance based on fuel choice.
- Environmental Benefits: Utilizing cleaner fuels decreases emissions significantly, a major win for environmental sustainability.
- Economic Advantages: As fuel sources diversify, costs may stabilize, giving consumers and industries more options and reducing reliance on volatile oil markets.
However, fuel diversification comes with its own set of challenges. Engine design must adapt to different combustion properties, which can complicate the manufacturing process.
Hybrid Systems
Hybrid systems represent another significant stride toward innovation. Combining traditional reciprocating motor technology with electric propulsion can lead to a new breed of efficiency and power management. These systems allow for:
- Improved Fuel Economy: By utilizing electric power during low-demand phases, these systems drastically cut fuel consumption.
- Reduced Emissions: Hybrid engines often produce fewer harmful pollutants, making them an attractive option for urban settings where clean air is a priority.
- Greater Versatility: Adaptable to various applications, hybrid systems can cater to both heavy-duty and lightweight demands.
However, hybrid systems also introduce complexity. Not only do they require new types of maintenance, but they also necessitate a careful balance between the reciprocating engine and electric components to maximize performance.
Smart Technologies
Finally, the integration of smart technologies into reciprocating motors can't be overlooked. This involves incorporating Internet of Things (IoT) capabilities, real-time data analytics, and advanced monitoring systems. The benefits include:
- Predictive Maintenance: Sensors integrated into the system can offer insights on when parts may need replacement, reducing downtime and unexpected failures.
- Enhanced Performance Monitoring: Real-time feedback on engine performance can guide operational decisions, translating to better fuel management and route optimization.
- User Experience: Smart interfaces allow greater interaction, enabling operators to fine-tune settings based on current needs or conditions.
Despite these benefits, deploying smart technologies requires investment in both infrastructure and training. Operators need to be well-versed in these systems to effectively leverage the technology.
"With every technological leap, we not only enhance performance but also redefine what urban mobility means for future generations."
Comparison with Other Motor Types
Understanding the differences between reciprocating motors and other types of engines is vital. This section serves not only to highlight the unique aspects of reciprocating motors but also to position them within the broader context of engine technology. When you take a closer look at various motor types, it is clear that each has its own strengths and limitations. Recognizing these differences can lead one to make more informed choices based on specific applications and needs.
Reciprocating vs. Rotary Engines
Reciprocating and rotary engines each present distinct mechanics and performance characteristics.
- Mechanical Differences:
- Efficiency Considerations:
- Application Suitability:
- Maintenance and Durability:
- Reciprocating engines work by converting linear motion into rotary motion. As pistons move up and down within cylinders, the energy from combustion is translated into power.
- Rotary engines, like the Wankel type, utilize a rotary design, wherein a triangular rotor moves within an oval chamber. This unusual configuration allows for fewer moving parts.
- Reciprocating motors often have more friction due to multiple parts working in conjunction, which can lower their efficiency.
- Rotary engines generally have smoother operation and less friction, though they may experience challenges in fuel consumption.
- Reciprocating engines dominate in applications demanding high torque, such as automotive and heavy machinery. Their ability to generate power across a wide range greatly benefits it in those contexts.
- Conversely, rotary engines are more suited for compact designs requiring lightweight attributes and high-speed performance, such as in some motorcycle applications.
- Reciprocating engines typically require more frequent maintenance due to the wear caused by moving parts.
- Rotary engines, on the other hand, are known for lower maintenance needs but may face issues with longevity at high-output scenarios.
"While reciprocating motors have a longstanding history of reliability and power, rotary engines offer innovative solutions for modern demands."
Diesel vs. Gasoline Motors
Diesel and gasoline engines illustrate another interesting comparison within the realm of reciprocating motors. Although both types utilize similar engine principles, their fuel dynamics and performance vary markedly.
- Fuel Characteristics:
- Performance and Efficiency:
- Emissions and Environmental Impact:
- Cost and Applications:
- Diesel engines operate on the principle of compression ignition. Diesel fuel has a higher energy density compared to gasoline; thus, diesel motors usually produce more torque.
- Gasoline engines work on spark ignition and are generally more suited for high-speed applications, relying on their ability to rev quickly.
- Diesels generally provide better fuel efficiency, making them preferred in heavy-duty vehicles like trucks, where fuel economy is paramount.
- Gasoline engines, however, shine in performance at high RPMs, thus being prevalent in cars designed for speed and agility.
- Diesel engines historically emit more nitrogen oxides and particulates cold be a reason for environmental concern.
- Gasoline engines usually result in a cleaner burn but often produce more carbon dioxide on a per-gallon basis.
- Diesel engines, typically more expensive, find their niche in industrial applications and transportation owing to their robustness and longevity.
- Gasoline engines dominate the lighter vehicle market, where cost and versatility generally take precedence.
Future Perspectives
Exploring the future of reciprocating motors reveals a landscape rich with potential advancements and applications. As industries evolve and new technologies emerge, these motors demonstrate an enduring relevance, carving out crucial roles in both current and future engineering endeavors. The drive for increased efficiency, reduced emissions, and enhanced power output can significantly reshape the trajectory of reciprocating motor technology.
Emerging Trends
Several key trends are shaping the future of reciprocating motors, each contributing to their development and application.
- Electrification: The ongoing transition to electric power in various sectors has pushed manufacturers to innovate within the reciprocating motor domain. Companies are now exploring hybrid systems that leverage both electric motors and traditional reciprocating engines to optimize performance and efficiency.
- Alternative Fuels: The adoption of alternative fuels is on the rise, as industries look for sustainable avenues to decrease their carbon footprint. Hydrogen fuel cells and biofuels stand out as promising options, requiring adaptations in engine design and technology to become viable alternatives to gasoline and diesel.
- Smart Technologies: Advances in IoT and smart technology aim to enhance the operational capabilities of reciprocating motors. With the integration of real-time monitoring and predictive maintenance, motors can achieve greater reliability and performance, minimizing downtime and operational costs.
These trends underline the importance of adaptability in the design and application of reciprocating motors. As industries embrace innovation, motors must follow suit, offering not only reliability but also sustainability and responsiveness to market changes.
Research and Development Directions
The future of reciprocating motors also hinges on ongoing research and development efforts, focusing on various key areas:
- Materials Science: Innovations in materials can lead to improvements in weight, durability, and heat resistance. Developing lighter yet stronger materials can help enhance performance while reducing energy consumption.
- Efficiency Improvements: Investigating new thermodynamic cycles and combustion strategies could lead to engines that utilize fuel more effectively. The quest for higher compression ratios and optimizing intake and exhaust processes can unlock significant gains in efficiency.
- Control Systems: As autonomous technologies gain traction, developing advanced control systems that leverage artificial intelligence can lead to more responsive and efficient operations of reciprocating motors. Enhanced control systems can tailor performance based on the application, whether in automotive, aerospace, or industrial contexts.
- Regulatory Compliance: Future developments must also consider shifting regulatory landscapes aimed at reducing emissions and increasing sustainability. Ensuring that new designs meet these regulations will be critical for commercial viability.
Research and development will ultimately dictate how well reciprocating motors can adapt to future demands. The insights gained from these endeavors will not only propel reciprocating motor technologies into new territories but also assure their continued significance in modern engineering.
"Innovating in the realms of efficiency and sustainability will define the legacy of reciprocating motors in the next decades."
Ending
The examination of reciprocating motors is pivotal in understanding not only their mechanical intricacies but also their far-reaching impact on various sectors. By summarizing the significant aspects covered throughout this article, we highlight the necessity and relevance of this technology in today's engineering landscape. Reciprocating motors are more than just components in machines; they serve as a bridge connecting theory to practical application, showcasing how fundamental principles drive innovations across industries.
Summarizing Key Insights
To encapsulate the essence of reciprocating motors, here are the key insights:
- Operational Mechanism: Each motor's functionality is rooted in its basic components like pistons and crankshafts, which cooperate through defined cycles to produce movement efficiently.
- Applications: These motors find utility in diverse arenas from automotive to aerospace, illustrating their versatile design and robust performance.
- Technological Innovations: Recent advancements, such as hybrid systems and smart technologies, are progressively reshaping the way these engines operate, optimizing fuel usage and enhancing efficiency.
- Challenges: It's worth noting the inherent challenges, primarily around maintenance and environmental concerns, that shape the dialogue on their future use and development.
In summary, understanding these key points not only amplifies our appreciation for reciprocating motors but also invites ongoing dialogue about their potential in future innovations.
Final Thoughts
Reflecting on the content discussed, it becomes evident that reciprocating motors are an indispensable part of modern machinery. While they have stood the test of time, their evolving nature and integration of new technologies will likely chart a promising path ahead. As research and technological capabilities advance, the quest for more efficient, sustainable, and adaptive engines will likely intensify.
In essence, reciprocating motors are not just relics of engineering history but living components that continuously adapt to meet the challenges of modern times. The future beckons, encouraging both innovation and collaboration across disciplines to harness their full potential within an ever-evolving technological landscape. This examiniation serves not merely as a conclusion but rather as a foundation for understanding where this essential component of mechanical engineering can lead us next.