Reactor Chemistry: Key Concepts and Industrial Applications
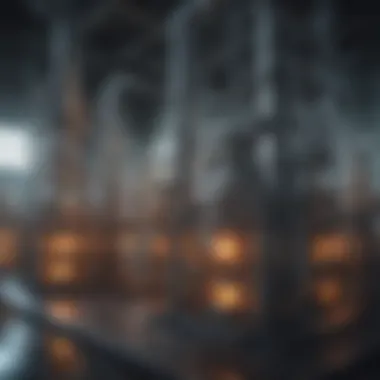
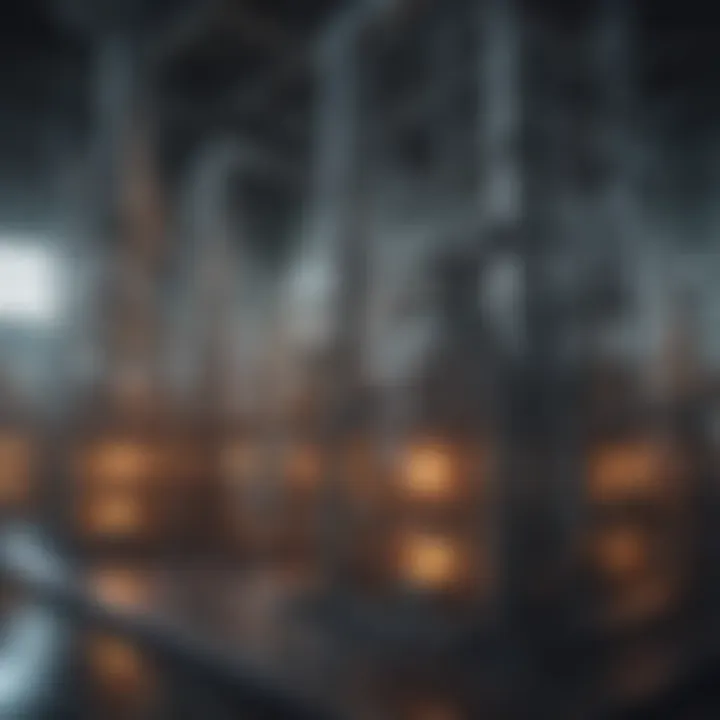
Intro
Reactor chemistry stands as a cornerstone within the realms of chemical engineering and industrial processes. The landscape of chemistry has seen remarkable advancements, and at the heart of it all is the understanding of how reactions unfold in various reactor settings. Recognizing the dynamics at play is not just an academic exercise but a critical component of developing efficient, safe, and sustainable chemical processes.
The essence of reactor chemistry lies in the intricate web of reaction mechanisms, kinetics, and thermodynamic principles. Each reaction behaves uniquely depending on a variety of factors—temperature, pressure, concentration, and even the type of catalyst used. Being attuned to these variables is crucial for professionals looking to optimize processes and enhance yield, minimize waste, and improve on economic and ecological fronts. Through this guide, we will explore these fundamentals and their practical applications, providing valuable insights tailored for students, researchers, educators, and professionals engaged in the ever-evolving field of chemical production.
Overview of Research Topic
Brief Background and Context
Understanding reactor chemistry encompasses delving into a rich history of scientific exploration. For instance, the advent of the Haber-Bosch process revolutionized the way ammonia is produced and laid the groundwork for modern fertilizers. In industrial settings, the manipulation of reaction parameters can lead to vastly different outcomes, impacting productivity and safety. The importance of reactor design can’t be overstated, as it dictates how raw materials are transformed into end products, serving a pivotal role in various industries such as pharmaceuticals, petrochemicals, and even food production.
Importance in Current Scientific Landscape
Today, the significance of reaction dynamics is magnified amidst rising global demands for energy efficiency and greener chemical processes. Researchers and engineers are continually seeking new methodologies that align with sustainability goals while ensuring economic viability. Moreover, with the integration of advanced technologies and modeling software, understanding the behavior of reactions has never been more critical. This makes knowledge of reactor chemistry not just relevant but essential in today's fast-paced scientific and industrial environments.
“The future of industrial chemistry hinges on our ability to innovate within the confines of existing knowledge about reactor behavior.”
In light of these considerations, a thorough examination of reactor types—batch, continuous, and plug flow—is warranted as they present unique advantages and limitations. Each design comes with its own set of challenges regarding scalability, control, and maintenance. In turn, these factors play a fundamental role in determining the economic feasibility of chemical processes.
Summary
As we progress through this article, we will engage with the various concepts surrounding reactor chemistry, providing a comprehensive guide that emphasizes the intricate balance between theory and practical application. By pulling together insights from across fields, the objective is to offer a well-rounded perspective that contributes to a deeper understanding of how to optimize chemical manufacturing for the benefit of society.
Prologue to Reactor Chemistry
Reactor chemistry stands as a cornerstone of the chemical engineering field, wherein the art and science of facilitating chemical reactions flourishes under controlled conditions. The dynamics at play inside various reactors directly influence not only the efficiency but also the quality of the chemical products produced. When one takes a step back and reflects on the broader implications, it’s clear that mastering reactor chemistry is fundamental for driving innovation in industries ranging from pharmaceuticals to energy production.
Understanding Reactor Chemistry means delving into an intricate web of reaction mechanisms, kinetics, and thermodynamics. This section lays the groundwork required to tackle complex problems that arise in real-world applications. What’s more, it brings forth an appreciation of the careful considerations that must be addressed while designing and operating reactors, ensuring processes are both safe and sustainable.
Definition and Scope
The term reactor chemistry encompasses the study of chemical reactions taking place within a designated reactor system. This includes defining the range of reactors utilized in both lab settings and large-scale industry, along with understanding their specific operational mechanisms. By delving into the scope of reactor chemistry, we can identify various types, such as batch and continuous flow reactors, each fitting its intended purpose like a glove.
On a more specific level, reactor chemistry examines:
- Reaction pathways: How reactants transform into products through various steps.
- Kinetics: The rate at which these transformations occur and the factors influencing these rates.
- Thermodynamics: Associated energy changes and their impact on reaction spontaneity.
From these elements, researchers can tailor chemical processes to achieve optimal results, be it higher yield or reduced cost.
Historical Overview
Looking back, the journey of reactor chemistry is as fascinating as the subject itself. The concept of conducting chemical reactions in controlled environments can be traced to the early days of science, where rudimentary methods were employed to facilitate reactions. For example, ancient alchemists played around with basic distillation and fermentation processes, often without the rigorous frameworks we have today.
Fast forward to the 19th century, scientists like Henry Cavendish and Dmitri Mendeleev laid the groundwork for contemporary chemistry through their discoveries and methodologies. The industrial revolution marked a turning point, prompting the need for more efficient chemical processes and leading to those initial designs of reactors we now rely upon. Innovations flourished in the 20th century, particularly with the advent of catalysis, which altered reaction rates dramatically, enhancing yields and reducing by-products.
Today, as we stand upon the shoulders of these giants, what's evident is not just the evolution of reactor technology but also the constant drive towards optimizing processes to align with modern-day sustainability goals. These changing paradigms make it vital for students, researchers, and professionals to grasp the fundamentals of reactor chemistry—to not only understand but to rethink the practices that shape our industries today and in the future.
Types of Reactors
Understanding the different types of reactors is essential when delving into reactor chemistry, as it lays the foundation for industrial processes and research applications. Each type of reactor is designed with specific reactions in mind, influencing the efficiency, safety, and economic viability of chemical production. Choosing the right reactor type often hinges on various factors such as the nature of the reactants, desired products, and operational conditions.
Batch Reactors
Batch reactors are perhaps the most traditional form of reactors, commonly used in the chemical industry. In these systems, reactants are loaded into the reactor at the outset, and the reaction proceeds for a set period before products are removed.
These reactors offer several advantages:
- Flexibility: They can handle a variety of reactions without the need for extensive modifications. This makes them ideal for small-scale operations and varied product lines.
- Simplicity: Easy to operate with straightforward control systems.
- Cost-Effective: Typically lower initial investment compared to continuous reactors, making them suitable for less frequent production.
However, they do come with downsides. The time it takes to load and unload can lead to lower production rates, which can be a significant drawback if high throughput is a priority. Moreover, scaling up processes from batch to larger systems may present challenges due to variations in reaction behavior at different scales.
Continuous Flow Reactors
Continuous flow reactors are designed for uninterrupted chemical processes, allowing reactants to flow into the reactor while products are simultaneously withdrawn. This continuous operation mode is highly beneficial for several reasons:
- Higher Efficiency: With reactants constantly fed into the system, the reaction conditions can be maintained steadily over time, leading to consistent product quality and increased production rates.
- Improved Safety: The ability to control reaction rates better and minimize the risk of unwanted side reactions generally enhances safety during operations.
- Easier Automation: Continuous processes are often easier to automate; something that industries strive for in today’s market.
Nonetheless, adopting a continuous flow system is not without its challenges. The design and operational complexities can be a hurdle, and the initial investment tends to be higher than that of batch reactors. Thorough understanding of the chemical processes involved is necessary to manage the potential scaling issues that might arise.
Semi-Batch Reactors
As the name suggests, semi-batch reactors hold characteristics of both batch and continuous reactors. In these systems, one of the reactants is added continuously, while others remain in a batch format. This hybrid approach offers several benefits:
- Enhanced Control: This reactor type allows for optimal control over reaction conditions, which can be particularly useful when dealing with hazardous materials.
- Improved Reaction Rates: The continuous addition can help drive the reaction forward more effectively than in traditional batch settings, improving yield under certain conditions.
- Flexibility: Like batch reactors, they also provide flexibility in process design and product strategy.
However, careful management and monitoring are essential with semi-batch systems. Balancing the addition of reactants and managing the overall reaction time can be complex.
"Choosing the right reactor is as crucial as the chemistry itself. It’s the heartbeat of any chemical process."
Whether you’re a scholar, industry professional, or just someone fascinated by the science behind chemical reactions, grasping these concepts is vital.
Reaction Mechanisms
Understanding reaction mechanisms is fundamental to reactor chemistry. They are the backbone of how reactions proceed, detailing the sequence of steps that lead to product formation. By dissecting these mechanisms, chemists can grasp why certain conditions optimize yields while others don’t. In the realm of industrial chemistry, knowing the precise steps within a reaction mechanism allows for improved reactor designs, enhancing efficiency and safety.
In essence, reaction mechanisms can be viewed as the map guiding the reaction journey from reactants to products. They elucidate factors such as reaction intermediates, transition states, and the energy changes associated with each step. Through this lens, one can see how thermodynamic and kinetic properties interplay, ultimately impacting the reactor's design.
Elementary Steps
Elementary steps are the fundamental reactions that occur within a larger mechanism. Think of them like the individual strokes of an artist creating a masterpiece. Each step is distinctive and pivotal, often transitioning through a series of intermediates before reaching the final product. For instance, consider the combustion of methane, where individual steps include the breaking of bonds in methane and oxygen, forming intermediate radicals before yielding carbon dioxide and water.
This can be summarized in several key features:
- Simplicity: Each elementary step represents a basic reaction rather than a complex series of steps.
- Single Transition State: Each step has a specific transition state that correlates with an energy barrier.
- Rate Determining Step: Often, one of these steps dictates the overall reaction rate, known as the rate-determining step. This insight is critical in optimizing process variables to align with industrial goals.
Understanding these elementary steps helps chemists predict how varying conditions—like concentration or temperature—might influence the overall reaction rate.
Complex Mechanisms
When delving into complex mechanisms, things become more intricate. Here, multiple elementary steps connect in a convoluted pathway. This layer of complexity is what mimics real-world reactions, where multiple interactions occur simultaneously. Take the example of photosynthesis in plants. Many steps are involved, all contributing to glucose's production from carbon dioxide and water, facilitated by light energy.
One of the intriguing aspects of these mechanisms lies in their multi-faceted nature:
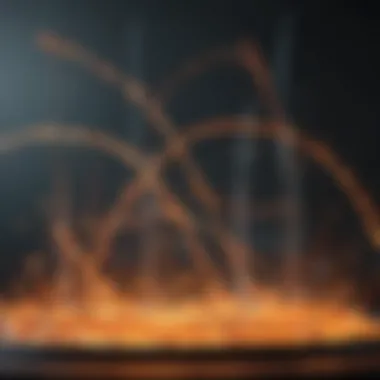
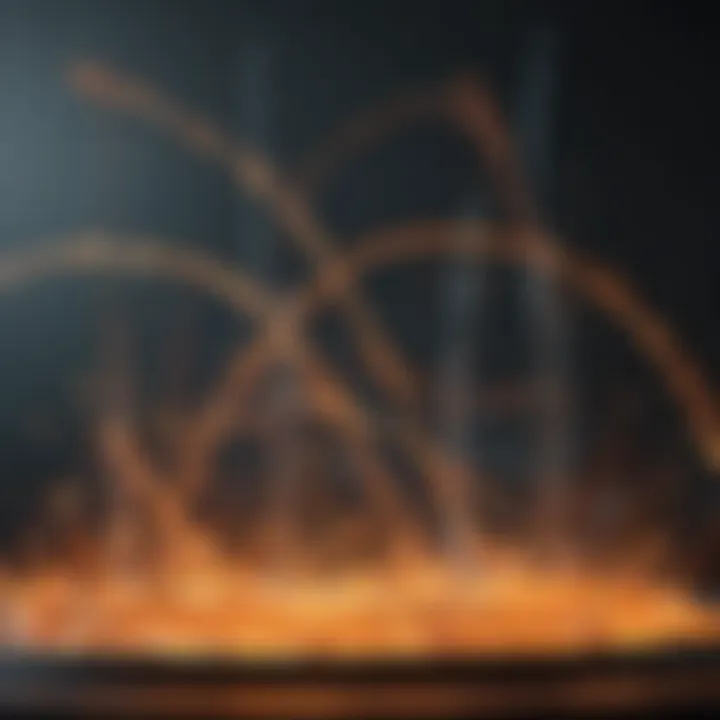
- Intermediates: Unlike elementary steps, complex mechanisms often involve various intermediates, each with its own characteristics and lifetimes.
- Multiple Pathways: Reactions may proceed through different pathways, creating a variety of products under unique conditions, which can be exploited in industrial settings to maximize desired outputs.
- Kinetic Models: Understanding these mechanisms often requires sophisticated models that can accommodate multiple variables and interactions.
A relevant quote to consider is:
"The most potent weapon in the hands of the oppressor is the mind of the oppressed." — Steve Biko
This emphasizes how knowledge of reaction mechanisms is a powerful tool for chemists, allowing them to manipulate and control reactions at an atomic level.
In summary, a profound understanding of reaction mechanisms, encompassing both elementary steps and complex pathways, equips chemists with the tools to innovate and optimize in the field of reactor chemistry.
Kinetics of Reactions
Kinetics of reactions is a cornerstone of reactor chemistry. Understanding how fast reactions occur is crucial for maximizing efficiency, safety, and productivity in chemical processes. Kinetics isn’t just about measuring speed; it's a window into the underlying mechanisms of reactions. By comprehulating these factors, researchers and engineers can design reactors that function optimally while minimizing unwanted by-products. Thus, the importance of kinetics cannot be overstated; it's essential for guiding practical applications, scaling up processes, and addressing challenges in reactor chemistry.
Rate Laws and Orders
Rate laws encapsulate the relationship between the concentration of reactants and the rate of a reaction. A rate law expresses this connection mathematically, typically formulated as:
Rate = k[A]^m[B]^n
where -
- k represents the rate constant,
- [A] and [B] are the concentrations of the reactants, and
- m and n are the reaction orders with respect to each reactant.
The reaction’s order can be determined experimentally and indicates how sensitive the reaction rate is to changes in concentration. For example, a first-order reaction means that a doubling of the reactant concentration will double the rate. In contrast, a second-order reaction has a squared dependency on the concentration, meaning increased complexity in how conditions influence the reaction.
"Understanding rate laws allows us to predict how changes in reactant concentrations can influence production rates, which is critical in any industrial setting."
Temperature Dependence
Temperature significantly impacts reaction kinetics. The famous Arrhenius equation:
k = A e^(-Ea/RT)
where -
- k is the rate constant
- A is the pre-exponential factor,
- Ea is the activation energy,
- R is the universal gas constant, and
- T is the absolute temperature
demonstrates how temperature affects reaction rates. As temperature increases, the kinetic energy of the molecules also rises, generally leading to an increased likelihood of effective collisions resulting in reactions.
Moreover, it is critical to observe how temperature not only affects the speed of the reaction but can also alter the reaction mechanism itself. Certain reactions might proceed via different pathways at higher temperatures, introducing different products due to variability in kinetic factors.
Pressure Effects
Pressure impacts kinetic behavior predominantly for gaseous reactions. According to Le Chatelier's principle, increasing pressure favors the side of the equilibrium with fewer moles of gas. The effect of pressure on reaction rates can also be elucidated through changes in concentration. If you pack gas molecules into a smaller volume, they collide more frequently, which typically raises the reaction rate. By understanding these pressure effects, engineers can better design reactors to optimize yield.
- For example, in synthesizing ammonia via the Haber process, increasing pressure is key to achieving a desirable equilibrium.
- Likewise, in gas-phase reactions, the rate increases significantly at elevated pressures, leading to faster production rates.
In summary, the study of kinetics surroundings provides insights that are necessary for innovation and efficiency in chemical manufacturing. Understanding the nuances like rate laws, temperature's dance with reaction rates, and how pressure plays its part equip professionals with the tools needed to fine-tune reactor operations effectively.
Thermodynamics in Reactor Chemistry
The role of thermodynamics in reactor chemistry cannot be overstated. It serves as the backbone for understanding how energy changes influence chemical reactions within reactors. This foundational concept helps chemists and engineers optimize processes, ensuring reactions occur under conditions that maximize yield while minimizing waste. By studying thermodynamic principles, one gains insight into how variables like temperature and pressure affect reaction outcomes. Ultimately, thermodynamics provides a lens through which the efficiency and viability of various chemical processes can be assessed, contributing to sustainable practices in industrial settings.
Enthalpy and Entropy Considerations
Enthalpy and entropy are two crucial thermodynamic concepts that govern the behavior of chemical reactions. Enthalpy, often denoted as (H), is a measure of the total heat content of a system. It reflects the energy required to break bonds and form new ones during chemical transformations. For example, in an exothermic reaction, where heat is released, the enthalpy change is negative, indicating that the products are more stable than the reactants. Conversely, an endothermic reaction absorbs heat, making enthalpy change positive.
Entropy, represented by (S), pertains to the degree of disorder or randomness in a system. A common saying in thermodynamics is "Nature prefers disorder." This implies that reactions tend to progress towards states of higher entropy. For instance, if a chemical reaction produces gas from solids, the increase in disorder drives the reaction forward.
Understanding the interplay between enthalpy and entropy is pivotal. They figure into the Gibbs free energy equation:
[ G = H - TS ]
where (T) is temperature in Kelvin. A reaction is spontaneous when Gibbs free energy is negative, which relates back to both enthalpic and entropic contributions.
Gibbs Free Energy and Spontaneity
Gibbs free energy plays a vital role in determining whether a chemical reaction will occur spontaneously under a given set of conditions. The concept of spontaneity refers not only to whether a reaction can happen but also how far it will go, meaning if it will produce a significant amount of product or stall out. When we look at the equation ( G = H - TS ), we see that spontaneity is driven by the tendency of systems to reach lower energy states, which correlates to the increase in randomness.
When evaluating a reaction, if the change in Gibbs free energy (\Delta G) is negative, the reaction is spontaneous. If it's positive, the reaction is non-spontaneous without additional input. This is especially crucial in designing reactors. Understanding these dynamics allows scientists to fine-tune conditions, such as pressure and temperature, to shift a reaction towards favorability. For instance, at higher temperatures, entropy's influence can promote spontaneity, even if the reaction is endothermic. On the other hand, colder temperatures might favor exothermic reactions where enthalpy is more significant.
Key Takeaways
- Thermodynamics, through concepts like enthalpy and entropy, lays the groundwork for understanding reaction dynamics in reactor chemistry.
- Enthalpy assesses energy changes in reactions, while entropy evaluates disorder, both guiding the feasibility and optimization of chemical processes.
- Gibbs free energy determines spontaneity, offering critical insight for effective reactor design.
"Thermodynamics plays the role of a gatekeeper in the kingdom of chemical reactions, deciding which pathways are favorable and which remain locked away."
Through these considerations, it's clear that thermodynamics is not merely a set of rules but a fundamental aspect of reactor chemistry that influences everything from design to application in real-world processes.
Catalysis in Reactors
Catalysis plays a pivotal role in the field of reactor chemistry. It significantly influences the rates and pathways of chemical reactions, leading to enhanced efficiencies in various processes. Understanding both homogeneous and heterogeneous catalysis is crucial for optimizing reactor design and operation. The benefits of incorporating catalysis in reactors are manifold. They include improving reaction rates, increasing product yields, and enabling selective transformations that might otherwise be challenging or even impossible under non-catalytic conditions. In the competitive landscape of the chemical industry, utilizing catalysts can mean the difference between a viable product and a costly failure.
Moreover, there's an element of sustainability tied to catalysis. By promoting reactions at milder conditions and reducing energy input, catalysts can lead to more environmentally friendly processes. Therefore, the insights garnered from studying catalysis within reactor systems are integral to advancing both industrial practices and academic research in chemistry.
Homogeneous Catalysis
Homogeneous catalysis involves catalysts that are in the same phase as the reactants—usually a liquid phase. This type of catalysis is beneficial because it allows for uniform distribution of the catalyst throughout the reaction medium, which can lead to enhanced reaction rates. A classic example is the use of sulfuric acid as a catalyst in the esterification reactions, where the acid helps in the formation of esters from alcohols and carboxylic acids.
Some specific advantages of homogeneous catalysis include:
- Ease of monitoring: Since the catalyst and reactants are equally mixed, it becomes simpler to analyze the reaction kinetics.
- Recyclability: In certain cases, catalysts can be recovered and reused without significant loss of activity.
- Selectivity: Homogeneous catalysts often provide high selectivity for desired products, reducing by-product formation.
However, there are some considerations to keep in mind:
- The catalyst may be challenging to remove from the final product, especially in multi-step syntheses.
- The fate of the catalyst can also complicate the design of reactors, particularly when considering scale-up.
Heterogeneous Catalysis
In contrast to homogeneous catalysts, heterogeneous catalysis involves catalysts in a different phase than the reactants, typically solid catalysts reacting with gaseous or liquid substrates. This arrangement can provide distinct advantages, particularly in industrial applications. An example of this is the Haber-Bosch process for ammonia synthesis, where iron serves as a solid catalyst to facilitate the reaction between nitrogen and hydrogen.
Heterogeneous catalysis comes with its own set of benefits:
- Easier separation: Since the catalyst is in a different phase, it can be easily separated from the reaction mixture, simplifying product purification.
- Stability: Solid catalysts are often more robust and can withstand harsher conditions without degrading.
- Longer lifespan: They tend to have longer operational lifespans compared to homogeneous catalysts due to lower susceptibility to deactivation.
Nonetheless, it’s important to address some of the challenges:
- Limited active sites: Not every catalyst particle may be available to contribute effectively to the reaction, which can lead to mass transfer limitations.
- Temperature and pressure dependencies: Heterogeneous reactions can be heavily influenced by external conditions, which necessitates precise environmental control.
Heterogeneous catalysts can indeed transform our approach to reaction engineering, enabling larger scale processes while maintaining high efficiency.
Reactor Design Principles
Reactor design principles form the backbone of effective reactor chemistry. These principles not only guide the selection of reactor types for specific applications but also determine how well reactions can be optimized in terms of yield and efficiency. As industries rely on chemical processes for various products, understanding design principles becomes absoltely paramount. It allows researchers and professionals to tailor conditions based on the reaction's needs, thus maximizing productivity while minimizing waste. The design of the reactor is entwined with several fundamental elements that influence various aspects such as safety, efficiency, and cost-effectiveness of chemical production.
Key considerations in reactor design include:
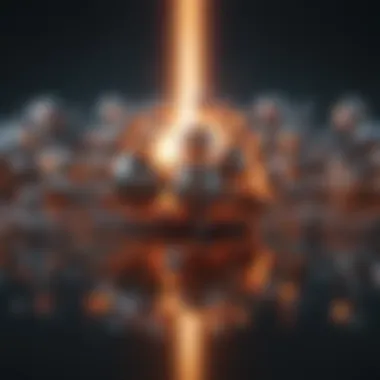
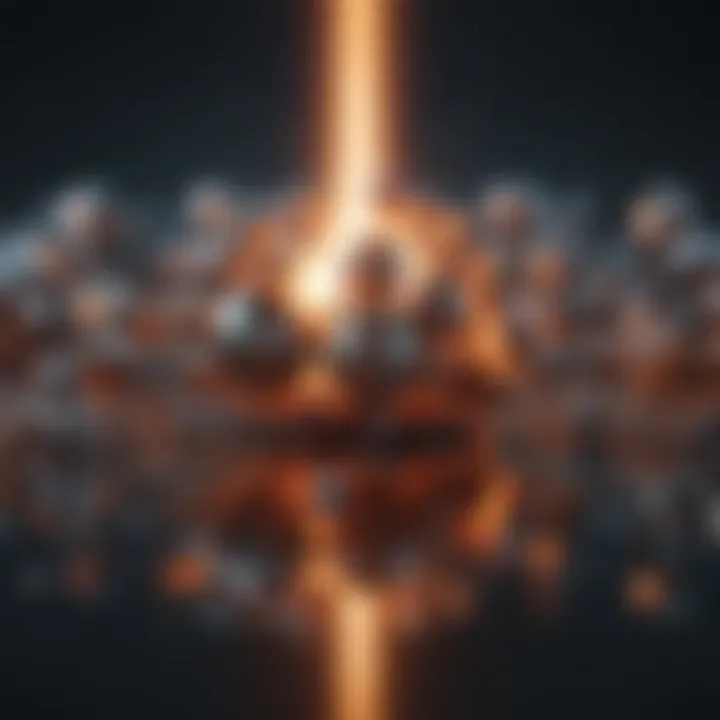
- Reaction Conditions: The temperature, pressure, and concentration can profoundly affect reaction rates and outcomes. Adjusting these conditions can lead to a significant shift in product yields.
- Reactor Type: Depending on the chemistry at play, a batch reactor might suffice, or it may require a continuous flow setup. Each type has its distinct advantages and limitations.
- Material Compatibility: Reactors need to be constructed from materials that can withstand corrosive substances without degrading over time. Selecting the right material is crucial to enhance the reactor's lifespan and operational reliability.
- Heat Management: Reactions that either release or absorb heat need careful thermal management. This is because temperatures that go awry can lead to uncontrolled reactions or affect product quality.
Effective reactor design also includes considerations for automation and scalability, allowing processes to be adjusted seamlessly from laboratory scale to large production units. This adaptability is essential in today’s fast-paced industrial landscape. As a part of a comprehensive understanding of reactor design principles, a continuous evaluation and improvement cycle fits in perfectly to identify possible enhancements in yield and safety.
Design Parameters
When diving deeper into design parameters, it is essential to recognize that these guide the functional aspects of a reactor. This includes factors such as:
- Volume and Surface Area: Reactor dimensions directly impact reaction rates and heat and mass transfer. A cleverly designed surface area can facilitate better mixing and greater exposure of reactants.
- Mixing Efficiency: In many reactions, keeping components well-mixed can significantly enhance reaction rates by ensuring that reactants meet uniformly.
- Flow Patterns: Understanding how fluids move in reactors is key to optimizing performance. Whether laminar or turbulent flow is needed often influences reactor shape and design.
Incorporating all these parameters involves a delicate balance. It’s akin to walking a tightrope where even small miscalculations can lead to costly operational hiccups. For instance, too much heat might result in runaway reactions, whereas inadequate mixing could lead to incomplete reactions.
Scaling Up Processes
Successfully scaling up processes from lab to production levels presents its own set of challenges. The ideal lab conditions often fall short in a larger production setup.
Some common hurdles include:
- Kinetics Scaling: A reaction that behaves ideally in a small batch might show unexpected kinetics when scaled. Different volumes can lead to varying heat transfer or mass transport phenomena that weren’t present previously.
- Economics: The cost to produce larger quantities often doesn’t scale linearly. Factors like increased raw material expenses and the necessity for larger infrastructure can inflate budgets.
- Quality Control: Maintaining product quality from small to large-scale production requires meticulous planning. Variability can crop up in reactions that become more pronounced at scale.
It's essential for chemists and engineers to engage in iterative testing during the scale-up phase. They should carefully analyze data, assess potential pitfalls, and arm themselves with alternative strategies—like adjusting reaction times, stick to shorter reaction pathways, or modifying the catalyst used.
In summary, reactor design principles involve an intricate mesh of operational factors. Each aspect must be finely tuned to yield success in commercial applications while ensuring that safety and efficiency remain top priorities.
Process Optimization
Process optimization in reactor chemistry deals with tailoring the conditions and design of chemical reactors to achieve maximal efficiency in production. This process is crucial for any facility aiming to enhance output or reduce resource wastage. The main goal is to find that sweet spot where yields are maximized while keeping costs low. Through effective optimization, plants can attain substantial improvements in productivity and environmental sustainability.
Central to process optimization is the understanding of variables that impact reaction dynamics. These can include:
- Temperature: Often, just a few degrees can make a considerable difference in reaction rates.
- Pressure: For reactions involving gases, increasing the pressure can shift equilibrium positions favorably.
- Catalyst selection: Choosing the right catalyst can lower activation energy, promoting the reaction without the need for extreme conditions.
Investing time and resources into optimizing processes yields several benefits:
- Enhanced Yield: By fine-tuning the conditions, manufacturers can significantly boost the quantity of desired product.
- Cost Efficiency: Minimizing the input of energy and raw materials directly impacts the bottom line.
- Environmental Impact: Optimized processes often generate fewer by-products and waste, aligning production with greener principles.
All these aspects underscore the relevance of optimization in reactor chemistry. It is not merely a technical exercise; it embodies a strategic initiative crucial for any modern chemical manufacturing.
Maximizing Yield and Selectivity
Maximizing yield and selectivity is a cornerstone of any successful chemical reaction system. Yield refers to the quantity of product obtained from a reaction, while selectivity is the preference for a reaction to produce a desired product over undesired ones. Balancing these two attributes can be a tightrope walk, as optimizing for one can sometimes compromise the other.
When targeting maximum yield, several factors come into play:
- Reaction Time: Extending the duration can often lead to better outcomes, but with caution to avoid side reactions.
- Reactant Concentrations: Higher concentrations can accelerate reaction rates but may enforce equilibrium limits.
- Temperature Profiles: Adjusting temperature gradients can sometimes nudge a reaction toward producing more of the desired product.
On the other hand, improving selectivity often requires a deeper dive into not just the substances involved but also the mechanism at play. Key considerations include:
- Opting for Specific Catalysts: Some catalysts favor certain pathways that enhance selectivity while maintaining good yield.
- Controlled Reaction Conditions: Fine control over temperature and pressure, as mentioned, can direct the reaction toward favored pathways.
In summary, by balancing these elements, chemists and engineers can significantly improve process efficiency, leading to better commercial outcomes.
Minimizing By-products
Minimizing by-products during chemical reactions is another essential aspect of process optimization. By-products not only reduce overall yield but also complicate downstream processing and increase costs related to purification and waste management. The challenge lies in understanding how to tailor reaction mechanisms to restrict the formation of these unwanted substances.
To mitigate by-product formation, companies should consider:
- Thorough Mechanistic Study: Understanding reaction pathways and stages can help identify why side products form, thus allowing strategic interventions.
- Reaction Condition Adjustments: Like a chef adjusting recipe quantities, fine-tuning parameters such as temperature, pressure, and reactant ratios can significantly shift product distributions.
- Feedback Control Systems: Implementing real-time monitoring of reaction conditions can prompt immediate adjustments, keeping by-product levels in check.
Overall, minimizing by-products contributes to a more efficient process, less waste, and a cleaner production line, aligning with sustainability objectives.
In the long run, the rigors of optimization establish a foundation for continuous improvement, leading to enhanced performance in reactor operations.
Applications of Reactor Chemistry
Reactor chemistry is not merely an academic pursuit; it plays an integral role in countless industrial applications that shape modern society. As chemical processes become increasingly complex and tailored to meet specific demands, understanding the applications of reactor chemistry is paramount. This section illuminates the significance of reactor applications, focusing on how they push the boundaries of efficiency and innovation, while also addressing various considerations that affect their implementation in real-world scenarios.
Chemical Industry Processes
In the chemical industry, reactors serve as the heart of production facilities. From large-scale petrochemical plants to specialty chemical makers, reactors facilitate a multitude of reactions crucial for synthesizing products that meet everyday needs.
The design and operation of reactors in this sector are finely tuned to maximize output. Below are some key aspects of chemical industry processes that highlight the relevance of reactor chemistry:
- Versatility: Different types of reactions, whether exothermic or endothermic, can be accommodated within various reactor designs. This flexibility allows for tailored processes that meet diverse product specifications.
- Safety Protocols: The importance of rigorously designed reactors cannot be overstated. Proper vessel construction and reaction protocols mitigate risks such as explosion and uncontrolled reactions, safeguarding both personnel and the environment.
- Economic Considerations: Optimizing reactor design translates into reduced operational costs. For instance, continuous flow reactors often yield superior productivity relative to batch processes, making them an attractive choice for large-scale manufacturing.
A specific example of reactor applications is in the production of ammonia via the Haber-Bosch process. Through careful control of temperature, pressure, and reactant ratios, this process exemplifies efficient reactor design that has had a profound impact on agriculture and food production.
Pharmaceutical Manufacturing
The field of pharmaceutical manufacturing is where reactor chemistry meets intricate scientific need. In this context, precision and control are of utmost importance, as the efficacy and safety of drugs hinge on robust chemical processes.
Pharmaceutical reactors are specially engineered to ensure consistent quality and reliability. Key considerations in this sector include:
- Regulatory Compliance: The pharmaceutical industry is heavily regulated. Hence, the reactors must be designed to meet strict guidelines that ensure the safety and efficacy of the produced drugs.
- Scale-Up Challenges: Transitioning from laboratory-scale synthesis to full-scale production can present unique challenges. The reaction environment often changes, and thus, reactor designs must adapt to maintain reaction efficiency and product quality.
- Innovation in Delivery Systems: Today, there's an increasing demand for personalized medicine. Hence, the application of novel reactors that enable rapid synthesis of diverse drug formulations is critical. For example, microreactors allow for fast screening of reaction conditions, significantly speeding up the drug development process.
Moreover, continuous reactors are becoming more popular in pharmaceutical manufacturing as they offer enhanced control over reaction conditions, ultimately leading to improved selectivity and reduced by-product formation.
"In the intricate tapestry of modern manufacturing, reactor chemistry weaves together the threads of innovation and efficiency, impacting not just industries, but society as a whole."
The applications of reactor chemistry are vast and critical to ensuring that both chemical industries and pharmaceuticals meet the demands of an ever-evolving world. By continuing to harness the principles of reactor design and operation, significant contributions can be made toward sustainability, efficiency, and safety in industrial processes.
Environmental Considerations
In the present-day landscape of chemical manufacturing, environmental considerations have risen to paramount importance. As the impacts of industrial activities on the ecological system become increasingly apparent, stakeholders across the board—be it scientists, policymakers, or educators—are beginning to craft strategies that ensure sustainability within reactor chemistry. This isn't just about adhering to regulations; it’s about embracing a broader responsibility toward minimizing ecological footprints while still delivering high-quality chemical output.
One significant facet of environmental considerations in reactor chemistry is the necessity of adopting sustainable practices. This involves integrating methods that either reduce environmental harm or enhance ecological sustainability within chemical reactions. For instance, many industries are shifting towards renewable energy sources to power reactors, thus lessening their reliance on fossil fuels, which will diminish overall carbon emissions.
Sustainable Practices
Sustainable practices encompass a wide array of methodologies and innovations designed to minimize the environmental impact of chemical processes. By employing green chemistry principles, reactors can be optimized to operate efficiently under conditions that require fewer harmful substances while maximizing resource utilization. Some of the sustainable strategies include:
- Use of Renewable Feedstocks: Selecting raw materials that are sustainably sourced can drastically lower environmental impact. For example, using plant-based substrates reduces dependency on limited non-renewable resources.
- Energy Efficiency Improvements: Technologies that allow reactors to operate at lower energy inputs must be prioritized. This includes implementing heat recovery systems or utilizing more efficient reaction pathways.
- Biocatalysis: By leveraging biological catalysts, reactions can often occur under milder conditions, which minimizes energy consumption and hazardous waste.
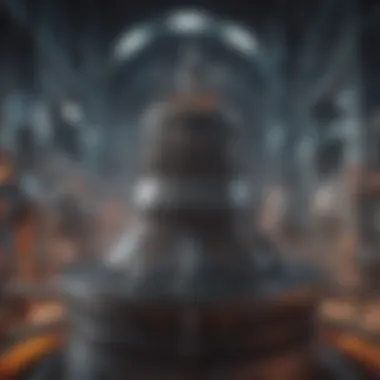
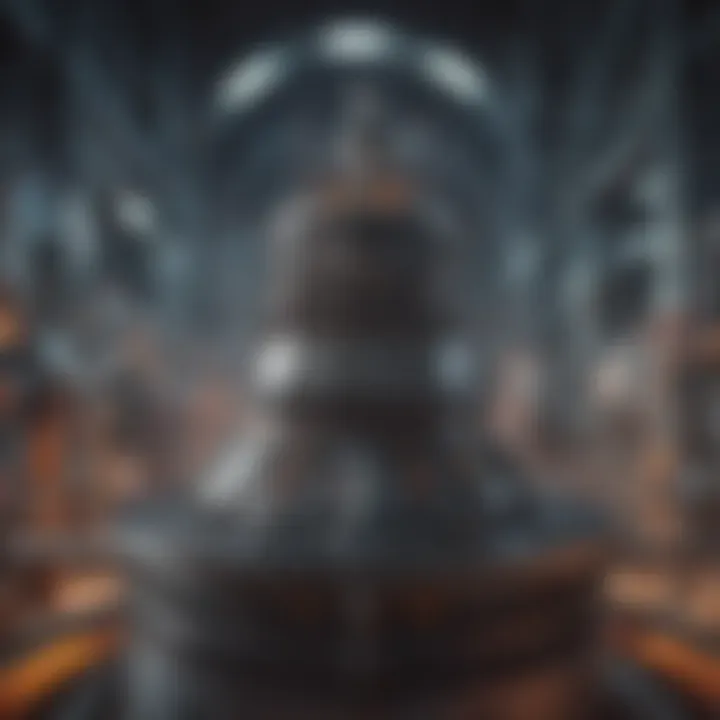
These sustainable practices not only help in reducing the carbon footprint but also often lower operational costs, proving that eco-friendliness and efficiency can go hand-in-hand.
Waste Minimization Strategies
Equally critical to the environmental discourse is the waste minimization strategies employed during chemical reactions. Waste management is not merely an afterthought but an integral part of reactor design and operation. Reducing waste at the source is a concept that has been steadily gaining traction. Here are several effective strategies to consider:
- Reaction Optimization: Careful adjustment of reaction conditions—such as temperature and pressure—can yield higher conversion rates and lower by-products.
- Process Integration: Designing processes that allow for the recycling of materials reduces the volume of waste generated. For example, coupling separate reaction stages or reusing solvents can cut down on waste significantly.
- Product Purification: Employing techniques such as membrane filtration or chromatography at earlier stages helps in separating valuable products from waste, thereby concentrating waste streams and easing disposal.
"Waste minimization not only contributes to environmental preservation but boosts the efficiency of the reactior systems by extracting more value from the resources used."
In essence, integrating effective environmental strategies within reactor chemistry leads to a dual benefit: safeguarding ecological systems and enhancing the economic viability of chemical processes. As chemists and engineers continue to innovate in this space, the potential for a greener future becomes increasingly tangible.
Future Trends in Reactor Chemistry
As we navigate the complexities of contemporary chemistry and its applications, the future of reactor chemistry emerges as a vibrant tapestry of innovation and integration. The significance of developing future trends in this field cannot be understated. With the increased demand for sustainable practices, efficiency in production, and adaptability to new discoveries, the mechanisms by which chemicals are produced must evolve. Embracing innovative reactor technologies and intertwining them with computational methods are vital steps toward enhancing both the scientific understanding and industrial applications of chemical processes.
Innovations in Reactor Technology
The landscape of reactor technology is constantly shifting, akin to a river searching for its most effective route. New designs and methodologies are steadily being adopted to accommodate the ever-growing needs of the chemical industry. These innovations can bring forth substantial advancements, including but not limited to:
- Modular Reactor Systems: Unlike traditional fixed designs, modular reactors offer flexibility. They allow for easier scaling and customization, reducing time-to-market for new chemical processes. Such systems can be combined or altered based on shifting production needs.
- Microreactors: With the advent of microreactor technology, chemical processes can now occur on a smaller scale, with higher control over reaction conditions. This leads to lower consumption of hazardous materials and energy, ultimately enhancing safety and efficiency.
- Continuous-flow Processes: These systems provide an unending stream of reactants, which contrasts sharply with batch reactors. The result is a consistent and predictable output, minimizing downtime and optimizing production rates. Industries utilizing this transition have reported significant boosts in output and reduced energy consumption.
"Innovation distinguishes between a leader and a follower." — Steve Jobs
Each of these innovations contributes towards a vision of reactor systems that are not only more efficient but also designed with sustainability at their core. This focus enables industries to comply with environmental regulations while enhancing profit margins.
Integration with Computational Chemistry
Exploring the intersection of reactor chemistry with computational chemistry represents another promising horizon. As we gain more computational prowess, the potential for predictive modeling in reactor design and operation becomes increasingly apparent. By harnessing advanced algorithms and data analysis techniques, scientists can forecast reaction pathways, optimize conditions, and minimize trial-and-error approaches inherent in experimental setups.
Some pivotal aspects of this integration include:
- Simulation of Reaction Dynamics: Using computational tools, researchers can simulate the behavior of reactors under varying conditions. This aids in understanding fundamental reaction mechanisms without the need for extensive laboratory experiments.
- Data-Driven Decision Making: Machine learning techniques can analyze vast datasets to identify patterns and correlations in reactions. This capability can guide adjustment of parameters to enhance yields and minimize unwanted by-products.
- Streamlined Design Processes: Combining computational models with experimental data fosters an iterative design process. This way, reactor designs can be continuously improved based on real-time feedback, promoting a culture of innovation and responsiveness.
Such an approach not only saves time and resources but also opens up avenues for novel discoveries. The synergy between computational and reactor chemistry enables scientists to push boundaries previously thought insurmountable. As we look ahead, the combination of innovative reactor technologies and computational methods promises to reshape the future of chemical synthesis, making it increasingly efficient, safer, and environmentally friendly.
Challenges in Reactor Chemistry
In the intricate field of reactor chemistry, facing challenges is not just a common occurrence; it’s almost an expected part of the process. As more industries rely on chemical reactions for production, understanding these challenges becomes essential. The significance of addressing scalability, safety, and efficiency impacts not just laboratory settings, but also large-scale industrial operations. Reactors designed to optimize chemical reactions must be continually assessed to ensure they meet changing demands and technological advancements. This section delves into two critical challenges: scalability issues and safety considerations.
Scalability Issues
Scaling a chemical reaction from the laboratory to the industrial level presents a myriad of hurdles. What may work perfectly on a small scale in a controlled lab environment can turn into a different beast when applied to a larger reactor. Factors to consider include:
- Reaction Kinetics: The rate at which reactions occur can change significantly during scale-up. Laboratory conditions often differ in temperature, pressure, and concentration at larger scales, leading to unexpected slowdowns or even halts in the reaction process.
- Heat Transfer: Effective heat management is crucial. In small reactors, heat removal might be straightforward, but in a larger setup, managing heat to avoid hotspots that's key to reaction efficiency can become challenging. Issues with thermal uniformity can lead to side reactions that reduce yield or create hazardous by-products.
- Mass Transfer Limitations: At smaller scales, materials can move in and out of the reactor efficiently, but as scale increases, the diffusion rates become critical. Insufficient mixing or slow mass transfer can hinder reaction efficiency.
Efforts to tackle these scalability issues involve detailed modeling and simulation techniques. Helping predict performance before physical implementation provides valuable insights. Computational tools have significantly advanced our capabilities in scaling reactions, but each new facility still requires careful examination to meet specific operational demands.
Safety Considerations
Safety in reactor chemistry cannot be overstated. The potential for chemical spills, explosions, or toxic releases can pose significant risks to workers and the environment alike. Addressing safety must be integral to reactor design and operation. Here are some essential aspects to consider:
- Reaction Exothermicity: Many reactions release a lot of heat. If not adequately managed, this energy can lead to dangerous escalation in reaction rates – think runaway reactions. Understanding the thermal profiles of reactions is paramount.
- Pressure Management: High-pressure conditions can arise, especially in continuous flow systems. Reactor vessels must be designed to withstand such stresses, and pressure-relief systems should be part of a comprehensive safety strategy.
- Chemical Handling Procedures: The more reactive or hazardous the chemicals, the more stringent the protocols must be. Ensuring proper training for personnel on safe handling, along with implementation of emergency procedures, is crucial in preventing accidents.
"The safety of chemical processes is paramount; one incident can overshadow decades of research and development."
Integration with Other Disciplines
In the realm of reactor chemistry, integrating knowledge and techniques from diverse scientific disciplines can significantly enhance both understanding and application. By overlapping fields such as biochemistry and physics, we open doors to innovative approaches that not only refine existing processes but also pave the way for groundbreaking discoveries. This multidisciplinary approach allows for a more holistic view of reactor dynamics, bringing forth a wealth of opportunities to optimize performance and mitigate challenges in chemical manufacturing.
For instance, insights from biochemistry can lend clarity to metabolic pathways involved in fermentation processes, while principles from physics can elucidate flow patterns and energy transformations within reactors. Each discipline contributes unique perspectives and tools that can enrich our overall comprehension of reactor chemistry.
Biochemistry and Reactor Design
The synergy between biochemistry and reactor design becomes instrumental, especially when discussing bioreactors that facilitate biological processes. These reactors often house microorganisms whose metabolic processes rely heavily on precise environmental conditions—pH, temperature, and substrate concentration, to name a few. Understanding the biochemical reactions occurring within these systems allows engineers to tailor reactor parameters that maximize yield and productivity.
In practical terms, a well-designed bioreactor, such as those employed in producing biofuels or pharmaceuticals, must accommodate the intricate needs of the biological agents involved. Here are some key considerations when integrating biochemistry with reactor design:
- Nutrient Supply: Constant monitoring and adjustment of nutrient concentrations ensure that the microorganisms thrive, thus driving the reaction rates.
- Mass Transfer: Effective gas-liquid or liquid-solid interactions are crucial in biophysical processes, influencing growth rates and product formation.
- Contaminant Control: Mitigating competing organisms or toxic by-products necessitates a thorough understanding of microbial behavior and kinetics.
Thus, it is evident that a robust grasp of biochemical processes is paramount for optimizing reactor design and ensuring efficiency in production pipelines.
Physics in Reaction Dynamics
Physics plays an equally vital role in shaping how we understand reaction dynamics within reactors. The flow of materials and heat transfer are phenomena grounded in physical principles, impacting the overall effectiveness of chemical reactions. For example, understanding fluid dynamics can help optimize flow rates, which directly influence the residence time of reactants and products.
Incorporating physics into reactor chemistry can lead to:
- Better Heat Management: Understanding heat transfer mechanisms helps in designing reactors that can effectively remove or add heat, maintaining ideal reaction conditions.
- Pressure Dynamics: Knowledge of gas behavior under varying pressure conditions informs reactor design, especially for those operating at high pressures where phase equilibrium is a concern.
- Transport Phenomena: A grasp of mass and energy transport is crucial for predicting how reactants mix and how products are expelled from a reactor.
By examining these physical underpinnings, researchers can design reactors with improved operational efficiency and safety.
"True innovation in reactor chemistry emerges when we consider the vast interplay between disciplines, reinforcing our capacity to tackle complex challenges in chemical production."
In sum, the integration of biochemistry and physics within reactor chemistry not only bolsters our understanding of various reactions and processes but also champions advances in design and implementation that stand to benefit many industrial sectors.
Finale and Perspectives on Reactor Chemistry
In wrapping up our exploration of reactor chemistry, it is essential to underscore the significance of understanding this field. It not only provides insights into the intricate mechanics of chemical reactions but also informs practical applications across various industries. The dialogue between chemical principles and reactor design shapes the landscape of modern scientific research and industrial processes. In the evolving world we inhabit, the ability to optimize reactions while minimizing environmental impact stands paramount.
The implications of reactor chemistry are wide-ranging. From improving the efficiency of pharmaceutical manufacturing to refining sustainable practices in the chemical industry, this field drives innovation. As professionals investigate the nuances of reaction mechanisms, integrating them with kinetic models and thermodynamic principles enhances our capacity to design better reactors. Realizing the relationship among these aspects could lead to breakthroughs in how we approach chemical manufacturing altogether.
Beyond practical applications, reactor chemistry encourages a multidisciplinary perspective. Its intersection with areas such as biochemistry and physics showcases the collaborative potential of scientific inquiry. It opens doors to diverse methodologies, allowing researchers and practitioners to leverage insights from one discipline and apply them effectively to another. This synthesis could foster innovations that transcend traditional boundaries.
“The beauty of reactor chemistry lies in its dynamic nature and adaptability to changing societal needs.”
Going forward, a commitment to continuous learning and adaptation will be vital. Fostering a culture of responsible research, utilizing computational techniques to predict reaction outcomes, and innovating reactor designs can push the envelope. Each of these endeavors not only enhances reaction efficacy but also supports sustainable development goals that resonate within and beyond the chemistry community.
Summary of Key Concepts
To distill the multitude of insights discussed throughout, here are the core concepts that embody reactor chemistry:
- Reactors are pivotal in controlling reaction conditions, including temperature, pressure, and concentration, fundamentally influencing reaction outcomes.
- Understanding reaction kinetics allows chemists to predict how fast reactions will occur, guiding them in reactor design and system optimization.
- Thermodynamics plays an essential role in assessing the feasibility of reactions, ensuring they are not just chemically possible, but also energetically favorable.
- Catalysis, whether homogeneous or heterogeneous, enhances reaction rates, reducing the energy needed, thus promoting sustainability in chemical processes.
- The interconnectedness of disciplines emphasizes a holistic approach, marrying various fields of study to solve complex problems in reactor chemistry effectively.
Outlook for Future Research
As the horizon of reactor chemistry expands, several avenues appear ripe for exploration. Emerging technologies, particularly in the realm of computational chemistry, stand at the forefront. These tools can model complex reaction dynamics allowing chemists to optimize designs before even stepping into the lab. This predictive ability has the potential to save both time and resources in the long run.
Additionally, advances in materials science can introduce novel catalyst designs that further enhance reaction efficiency. Sustainable catalysts, derived from abundant and non-toxic materials, promise to reshape the approach to chemical manufacturing toward a greener future.
Furthermore, the integration of machine learning techniques into reactor design offers opportunities for unprecedented efficiency. By analyzing extensive datasets from previous experiments, algorithms can identify patterns or suggest optimization strategies that might escape even the most seasoned researchers.