Ion Beam Etching: Techniques and Applications Explained
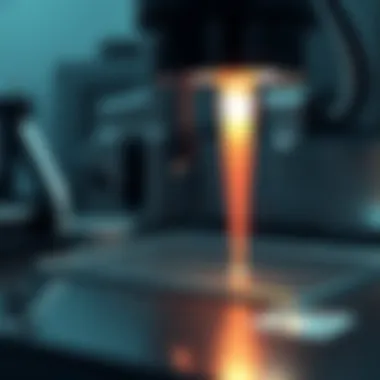
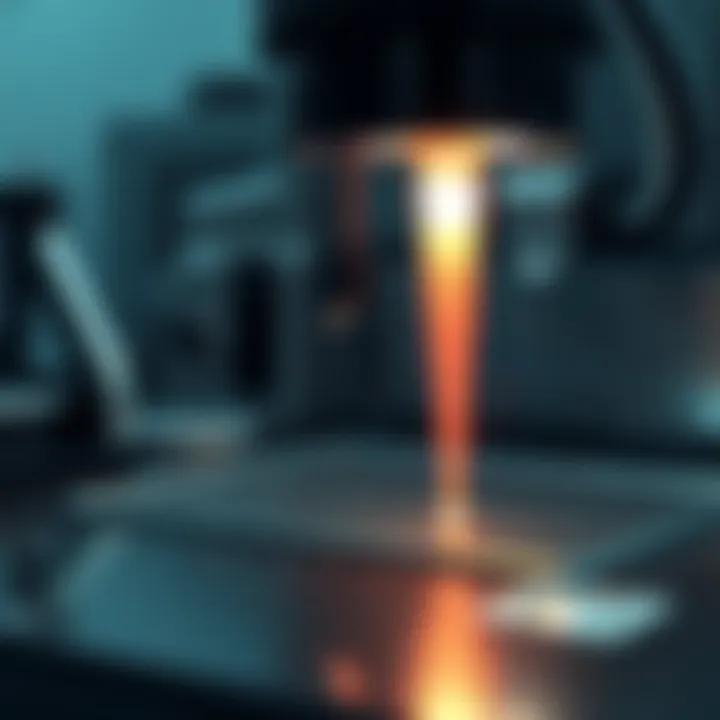
Overview of Research Topic
Brief Background and Context
Ion beam etching (IBE) is a sophisticated technique that has transformed the landscape of materials fabrication, especially in fields that depend significantly on precision micron and nanoscale structuring. The process utilizes accelerated ions to etch specific materials, offering outstanding control over the depth and resolution of the patterns created. This ability is invaluable in microelectronics, where even the slightest modifications can impact performance dramatically.
Understanding IBE requires a look into its foundation, which is rooted in ion optics, plasma physics, and surface science. The method arose from a need for high-resolution patterning that surpasses conventional etching techniques, particularly in semiconductor manufacturing where the demand for miniaturization has never been greater. As technology continues to advance, the integration of IBE in various applications, from circuit fabrication to nanotechnology, emphasizes the method's relevance and importance.
Importance in Current Scientific Landscape
In todayās rapidly evolving technological environment, the significance of ion beam etching cannot be understated. It is a cornerstone in the development of devices that power our digital world. Through IBE, researchers and engineers can create intricate microstructures necessary for innovative applications, like advanced sensors, photonic devices, and even quantum computing elements.
The ongoing innovations in IBE technology, such as improvements in beam parameters and automation, further reinforce its critical role. Furthermore, as industries strive for higher performance and lower costs, IBE provides a pathway toward achieving these goals, establishing its importance in both research and practical applications. The versatility of IBE allows it to slip neatly into different sectors, thus acting as a catalyst for novel technological advancements.
"As the electronics market evolves, ion beam etching stands at the forefront of enabling tomorrow's technologies."
Methodology
Research Design and Approach
To explore the intricacies of ion beam etching, a detailed analysis of existing literature, empirical studies, and case applications is essential. The approach examines various IBE techniques, their underlying principles, and integration into real-world applications. Key focus areas include observing advancements in equipment and methodologies that have surfaced over the past few years, as well as scrutinizing the contributions from academia and industry.
Data Collection Techniques
For this exploration of IBE, data collection involves technical papers, industry reports, and patents. These documents provide insight into:
- Theoretical foundations of ion beam etching.
- Comparisons with other etching techniques.
- Case studies showcasing practical implementations of IBE across different domains.
The insights gained from these sources enable a more nuanced understanding of how ion beam etching fits into the broader scientific narrative and technological advances.
Foreword to Ion Beam Etching
Ion beam etching (IBE) is a foundational technique used in material fabrication and microelectronics, especially in the creation of intricate nanoscale structures. Understanding IBE is essential not just for its technical applications but also for its broader implications in advancing fields like nanotechnology and material science. The precision involved in ion beam etching allows engineers and scientists to shape materials at an atomic level, which brings about a host of benefits, including the capability to fabricate complex devices and improve their performance.
In this section, we will detail what ion beam etching is, exploring its definition and historical context, allowing readers to appreciate how this technology developed and evolved over time.
Definition and Overview
Ion beam etching is a specialized process that utilizes ionized particles to remove material from a substrate. In essence, it bombards surfaces with a focused beam of ions, commonly made of gases like argon or xenon. This bombardment facilitates the etching of surfaces, allowing for the production of highly detailed patterns necessary in microelectronics. The process takes advantage of the momentum transfer from ions to the atoms in the target material, effectively dislodging them.
To put it simply, ion beam etching serves as a precise tool for sculpting materials, paving the path for technologies that we now rely on.
Educators and researchers alike often emphasize IBE's role in semiconductor manufacturing, where the demands for miniaturization and precision have never been higher. By allowing manufacturers to achieve such levels of accuracy, IBE plays a crucial role in almost every cutting-edge electronic device we use today.
Historical Development
The journey of ion beam etching is quite fascinating, tracing back to the mid-20th century when the field of ion optics began to gain traction. Early experiments were mostly exploratory, aiming to understand how ions interacted with materials at a basic level. In the 1960s, researchers discovered that ions could be used effectively to etch materials, leading to significant advancements in surface micromachining.
By the 1970s, IBE started gaining traction in industries, especially in the production of semiconductor devices. The adoption of ion beam etching in the microelectronics sector transformed how chips were designed and manufactured. This was not just a fad but a genuine game-changer, allowing for the creation of smaller, more efficient, and powerful electronic components.
Throughout the years, ongoing research and technological developments have refined ion beam etching techniques. This led to the emergence of new applications in fields such as nanotechnology and material sciences, helping industries design functional nanostructures and control properties at the nanoscale.
Ultimately, the historical arc of IBE underscores its significance and adaptability within evolving technological landscapes, which is a testament to its foundational role in modern scientific endeavors.
"Ion Beam Etching: not merely a tool but a key to unlocking new frontiers in material science."
As we proceed, the article will delve further into the underlying principles of IBE, the equipment and setups used, and the array of applications that highlight its quintessential role in contemporary manufacturing.
Fundamental Principles of Ion Beam Etching
Ion beam etching (IBE) stands out as a vital process in the realm of microfabrication and materials science. Grasping the fundamental principles of IBE is not merely an academic pursuit; it serves as the bedrock upon which various advanced techniques are built. This section illuminates the intricacies involved, encompassing the mechanisms of material removal and the parameters that heavily influence the etching outcomes. Recognizing these principles allows researchers and engineers to harness IBE effectively, ensuring high fidelity in their applications.
Basic Mechanisms of Material Removal
Material removal in ion beam etching relies heavily on the interaction between energetic ions and the target material. When an ion strikes the surface, it imparts energy, setting off a chain reaction that leads to the ejection of surface atoms. This is often described through models of sputtering, where the collision between ions and atoms results in displacement and scattering. There are several key mechanisms at play:
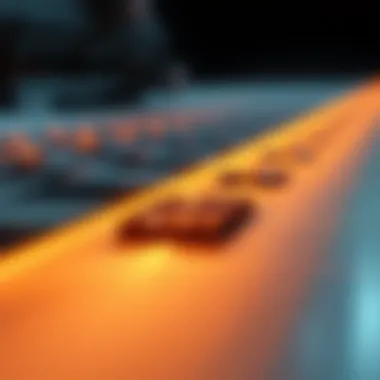
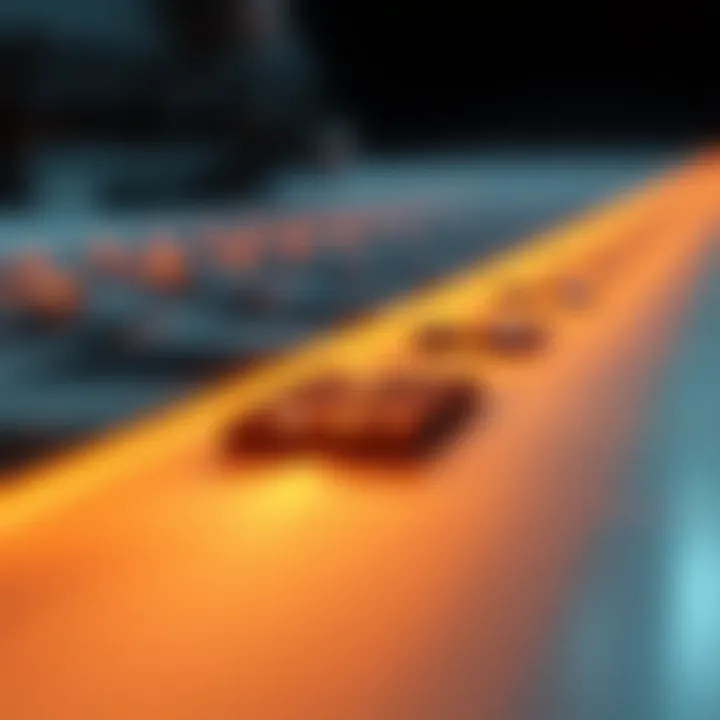
- Sputtering: The primary mechanism involves the transfer of energy from the ion beam to the target material. The high-energy ions dislodge target atoms by imparting momentum, causing them to escape into the vacuum environment. This process can be fine-tuned by adjusting the ion beam energy and incidence angle.
- Chemical Reactions: Depending on the material and the environment, chemical reactions can occur that aid in the etching process. For example, reactive ion etching incorporates gases that react with the material, enhancing the overall removal rate.
- Resputtering: When secondary particles are released, they may be further impacted by incoming ions. This resputtering can lead to complex patterns but also presents challenges in maintaining uniformity.
Understanding these mechanisms is crucial as they dictate the efficiency and quality of etching, influencing the final outcomes in applications ranging from microelectronics to nanotechnology.
Key Parameters Influencing IBE
Several critical parameters must be considered when conducting ion beam etching, as they directly affect the etching quality, speed, and any damage to the substrate. These parameters include
Beam Energy
Beam energy refers to the kinetic energy of the ions in the beam, typically measured in keV (kilo-electron volts). A higher beam energy can result in a higher material removal rate but may also increase the risk of substrate damage. Key characteristics of beam energy include:
- Impact on Sputtering Yield: Higher beam energy often leads to a greater sputtering yield, meaning more material is removed in a shorter time frame. This makes beam energy critical for processes demanding fast turnaround.
- Substrate Considerations: Different substrates respond differently to beam energy. For instance, sensitive materials may require striking a balance to mitigate damage while achieving the desired etching rate.
"The choice of beam energy is like walking a tightrope; you need the right balance between efficiency and preservation."
Ion Species
The type of ion used in the etching process can significantly influence the outcomes. Ion species span a spectrum from noble gases like argon to reactive species like chlorine and fluorine. Here's why the choice of ion species matters:
- Effectiveness of Material Removal: Different ions interact differently with materials. For example, argon ions are often chosen for inert sputtering, making them popular in various applications.
- Selective Etching: Utilizing specific ions can result in selective removal of materials. Reactivity plays a major role, with some species causing preferred etching via chemical reactions.
- Byproduct Management: The choice also influences the byproducts generated, which can impact the cleanliness and efficiency of the etching process.
Pressure Conditions
The operating pressure during ion beam etching is yet another crucial factor. High vacuum conditions are generally preferred, but variations can alter the etching dynamics:
- Mean Free Path: At lower pressures, the mean free path of ions is extended, allowing for fewer collisions with gas molecules, making the process more effective and controlled.
- Gas Background: Introducing specific gases can support reactions, yet excess gas can hamper the process by introducing unwanted collisions.
Managing these parameters can significantly enhance the quality of ion beam etching, and understanding them is fundamental for anyone delving into the field. Coupling practical experience with theoretical knowledge enables researchers to push the boundaries of what can be achieved with this versatile technique.
Equipment and Setup for Ion Beam Etching
In the realm of ion beam etching, having the right equipment and setup is not just a requirement; itās fundamental to achieving precise and controlled results. The delicate nature of nanoscale material removal calls for specialized hardware that can manage various parameters to produce the desired etching effects. A well-structured approach to equipment can make or break the outcomes in both research and industrial applications.
Ion Beam Sources
Types of Sources
Ion beam sources are the core components that generate the beams used for etching. Various types exist, each with its advantages and unique characteristics. For example, sputter ion sources are well-known for their ability to provide high-quality ions and customizable energy levels. They work by ejecting atoms from a target material, creating a stream of ions that can be directed onto the substrate.
Another common source is the RF (Radio Frequency) ion source. This type is renowned for its simplicity and effectiveness, often producing a steady ion current ideal for consistent etching. The main characteristic of RF ion sources is that they employ electromagnetic fields to accelerate ions, making them efficient in delivering energy to the substrate.
In summary, both types provide strong options depending on the desired etching application. While sputter sources might shine when high-quality ions are required, RF sources are favored for their ease of use and operational reliability.
Selection Criteria
When selecting an ion beam source, several criteria come into play. One critical aspect is scalability; the source should accommodate different sizes and types of substrates without compromising etching quality. Additionally, ion species being generated plays a significant role.
Choosing between noble gases like Argon or reactive gases such as Xenon can substantially impact the etching process. Each gas contributes differently to the etching outcomesāreactive gases can lead to more aggressive material removal, while noble gases often yield cleaner, less damaged surfaces.
Another unique feature to consider is energy tunability. The versatility of an ion source to adjust energy according to the substrate and material being used is vital for optimizing the etching process. However, itās crucial to balance performance with cost, as specialized sources may significantly hike up the budget.
Etching Systems and Chambers
Beyond the ion sources, the etching systems and chambers create the environment where the actual etching takes place. These setups must be meticulously designed to control factors like pressure and temperature, which substantially influence etching precision. Chambers should typically maintain a high vacuum to reduce the presence of unwanted particles that could interfere with the beamās effectiveness.
Applications of Ion Beam Etching
Ion Beam Etching (IBE) is a crucial technology in many facets of material fabrication and analysis. Its precision and unique ability to pattern at the nanoscale make it a sought-after process in various applications. As industries strive for finer features and intricate designs, the relevance of IBE cannot be overstated. This section will cover its significance in semiconductor manufacturing, nanotechnology fabrication, and material science, providing a comprehensive overview of how IBE influences modern technological progress.
Semiconductor Manufacturing
In the realm of semiconductor manufacturing, Ion Beam Etching plays an indispensable role. It's largely used for creating intricate patterns on silicon wafers, a necessity for fabricating integrated circuits. The demands for high precision in this sector are relentless, and IBE meets these needs by offering:
- High Resolution: One of the primary advantages of ion beam etching is its capability to produce features smaller than traditional etching techniques allow. This precision is fundamental as transistors decrease in size and the need for finer circuits increases.
- Controlled Etching: Unlike chemical etching methods, which can lead to undercutting and unwanted side reactions, IBE provides a more focused beam that minimizes damage to adjacent materials. This is pivotal in maintaining the integrity of the semiconductor structures.
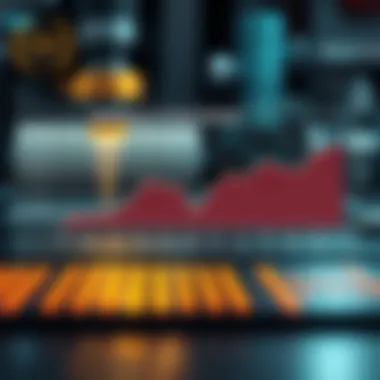
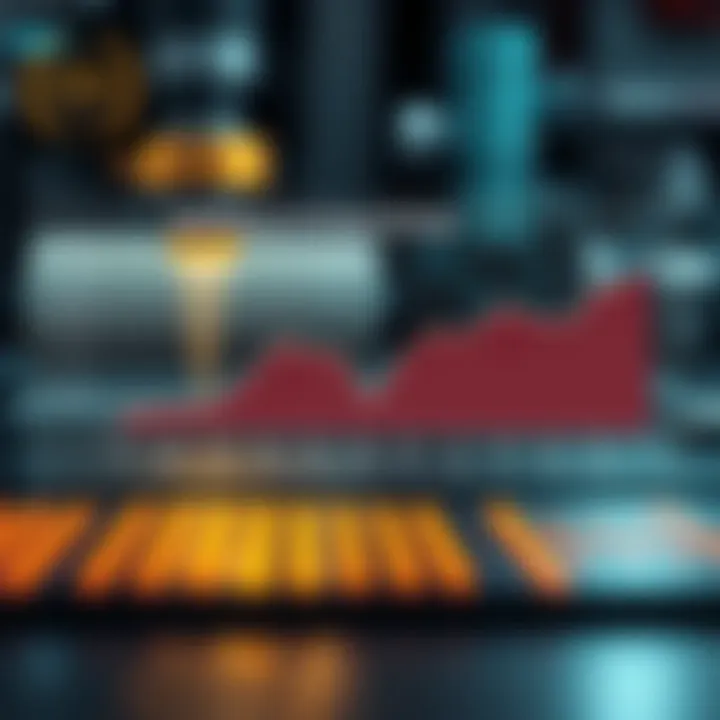
The use of IBE in semiconductor manufacturing epitomizes how advanced techniques directly influence performance and efficiency in electronics.
Nanotechnology Fabrication
Nanoscale Patterning
Nanoscale patterning has become an essential aspect of nanotechnology. IBE enables the creation of highly detailed nanostructures, which are pivotal for applications ranging from sensors to drug delivery systems. One of the standout features of nanoscale patterning through ion beam techniques is:
- Unique Feature: IBE allows for the direct writing of patterns with minimal collateral damage, which is often a major concern in nanoscale fabrication. This translates to better overall device performance.
- Advantages: The ability to pattern on a nanoscale opens myriad possibilities in research and industrial applications. However, patience is key; the speed of the process tends to be slower compared to other methods, which can be a disadvantage in high-throughput environments.
Functional Nanostructures
When it comes to functional nanostructures, IBE plays a significant role. These structures serve specific purposes, enhancing the functionality of various applications. The notable aspects of functional nanostructures include:
- Key Characteristic: Their ability to be tailored to meet precise specifications makes them highly versatile across different scientific fields.
- Unique Feature: The manufacturing process of these nanostructures often involves creating multiple layers, where IBE shines by providing excellent depth control, resulting in multilayer devices with distinct properties.
- Disadvantages: That said, the complexity involved may introduce challenges in quality control and reproducibility, which researchers must navigate carefully.
Material Science
In material science, Ion Beam Etching serves as a tool of innovation. IBE is utilized to modify surfaces and alter material properties at a microscopic level. It can be instrumental in:
- Surface Cleaning: By removing contaminants without affecting the underlying material, IBE offers a precise way to prepare surfaces for further analysis or application.
- Material Layering: It allows scientists to create precise multilayer systems, enabling the study of layered materials and their interactions. This can be particularly useful in developing new composites or coatings.
Advantages of Ion Beam Etching
Ion Beam Etching (IBE) as a method in materials processing is not just another tool in the box; it stands out for its distinct advantages that are vital for modern technological applications. Understanding these advantages gives insight into why IBE is extensively utilized in various sectors like microelectronics and nanotechnology. Letās dig into how IBE creates unique value through its precision and material versatility.
High Precision and Resolution
One of the standout benefits of Ion Beam Etching is its capability for high precision and resolution. This feature is crucial in fields where accuracy countsālike fabricating microchips, where even a minute mistake can lead to significant failures. In practice, the precision of IBE enables the creation of intricate nano-patterns on surfaces with a resolution that often sits in the sub-micron range.
The controlling nature of ion beams allows for selective material removal, creating defined features without the collateral damage that can easily occur with traditional etching techniques. This is largely due to the focused energy of the ions striking the substrate, which allows for tailored etch profiles and minimizes unwanted side effects.
Moreover, the ability to adjust parameters such as beam energy and incidence angle enhances the control over etching profiles. As a result, researchers can manipulate these settings to achieve desired outcomes for specific applications. Aside from creating precise patterns, the clean nature of IBE prevents residue from interfering with subsequent process stepsāan essential factor in high-tech manufacturing.
Versatility Across Different Materials
The versatility of Ion Beam Etching cannot be overstated. Unlike some etching methods that work splendidly on specific materials but falter on others, IBE is adaptable to a wide variety of substrates including metals, ceramics, and polymers.
- Materials Compatibility:
- Silicon: Extensively used in semiconductor fabrication.
- Metals: Such as gold or aluminum, allow for devices that require conductive layers.
- Polymers: Enable the etching of complex microfluidic devices.
The broad range of compatible materials opens up avenues for innovative applications like functional nanostructures, where different material properties can be employed to engineer unique functionalities.
- Multiple Applications: The adaptability also means IBE can be used across diverse fields, contributing to semiconductor manufacturing, optics, and biomedical devices. This multifaceted capability allows researchers and engineers to explore novel solutions that utilize various materials, further advancing technology and scientific research.
Thus, within the grand design of modern fabrication techniques, IBE shines through both its precision and versatility as a key player, cementing its role in various advanced applications. Hereās a takeaway:
"Whether you're tailoring a microchip or sculpting a nanoscale device, the advantages of Ion Beam Etching extend beyond ordinary expectations. Its precision and flexibility make it a cornerstone of modern materials science."
Ion Beam Etching, with its unique attributes, is not just an added benefit in the toolkit of advanced fabrication; itās become synonymous with innovation and precision, paving the way for next-generation technological breakthroughs.
Challenges in Ion Beam Etching
Ion beam etching (IBE) offers significant benefits in the precision and control of material removal, but it is not without its hurdles. Understanding these challenges is crucial when considering the adoption and implementation of IBE in various applications. From potential damage to substrates to the complexities of process control, these factors play an essential role in the operational efficiency of ion beam etching.
Damage to Substrates
One of the foremost challenges with ion beam etching is the risk of damage to substrates. When high-energy ions bombard a surface, thereās a fine line between effective etching and causing irreversible harm. This damage can manifest as rough surface features, altered material properties, or even structural degradation of the underlying substrate.
For instance, silicon wafers, often used in semiconductor manufacturing, can be particularly susceptible to defects when facing a bombardment of high-energy ions. If the energy levels are not meticulously calibrated, it can lead to what some researchers term āsputter damage.ā This refers to the unintended removal of atoms from the material's surface that can compromise its integrity and functionality.
To mitigate substrate damage, one must consider several strategies:
- Energy Calibration: Properly tuning the beam energy can prevent excessive damage while maintaining etching efficiency.
- Beam Angle: Adjusting the angle of incidence can help manage the extent of interaction between the ions and substrate.
- Temperature Management: Sometimes, chilling the substrate can minimize thermal effects that exacerbate damage during etching.
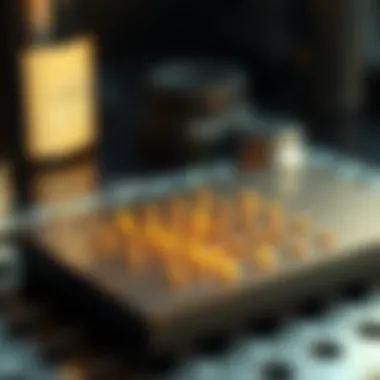
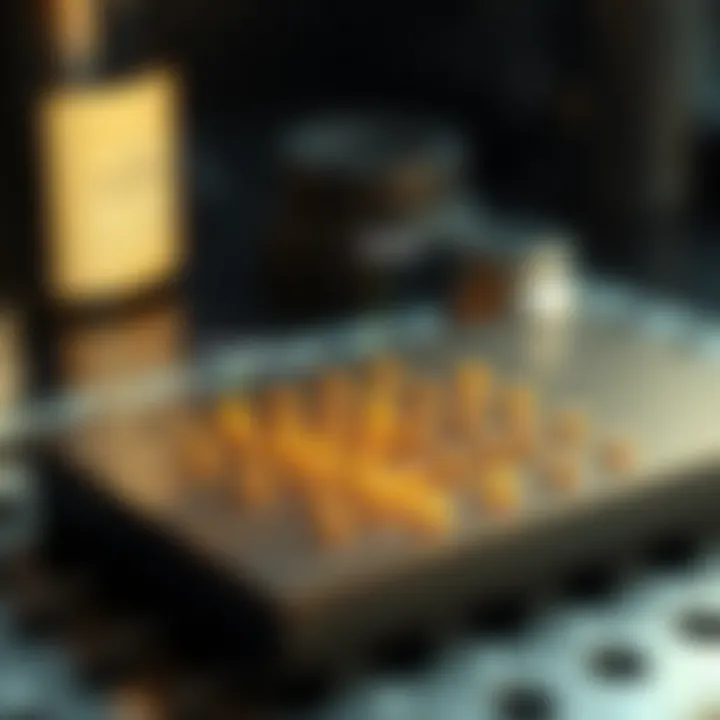
Incorporating these considerations can improve the survivability of the substrate and maintain its intended properties after IBE processes.
Process Control and Optimization
Another challenge often encountered in ion beam etching is maintaining precision in the control and optimization of the etching process. The dynamics of ion beam etching can become quite intricate, with numerous parameters interacting in ways that may not always be predictable.
To achieve optimal outcomes, several factors need constant monitoring and adjustment:
- Beam Current: Too high a current can speed up the process but may compromise quality, while too low could lead to inefficiencies.
- Etching Time: Accurately timing the etch process is essential to achieve desired depth and pattern fidelity.
- Environmental Conditions: The pressure and gaseous environment in which IBE occurs can also introduce variables that must be fine-tuned.
Optimizing IBE involves balancing these parameters in a way that maximizes efficiency while minimizing unwanted byproducts or issues. It's often a game of trial and error, where experience plays a crucial role. A recommendation for those delving deeper into IBE is to utilize tools and data acquisition systems that can provide real-time feedback on process parameters.
In summary, while ion beam etching stands out due to its unrivaled precision and applicability across various domains, the associated challenges such as substrate damage and process control must be diligently addressed. The ongoing research and continuous improvements in equipment and methodologies will help alleviate these concerns, paving the way for a broader adoption of IBE techniques across diverse industries.
Recent Research and Innovations
In the ever-evolving field of materials science, the exploration of ion beam etching shines brightly. Recent research and innovations in this area are crucial for pushing boundaries and enhancing existing methodologies. With the surge of interest in nanoscale fabrication and the demand for precision, researchers are consistently exploring new avenues to refine IBE techniques. This focus not only promises improved performance but also fosters a creative environment that invites collaboration and multi-disciplinary approaches.
Novel Techniques in IBE
Researchers are continually introducing novel techniques in ion beam etching, which offer significant advancements over traditional methods. For instance, one such technique is the development of variable angle ion beam etching. This approach allows for better control over the etching process by adjusting the angle of ion incidence. By varying the direction, it can minimize unwanted effects such as shadowing. This can result in more uniform etching profiles, which is a critical requirement for modern semiconductor devices.
Another innovative method, mass-selected ion beam etching, has gained traction. This technique harnesses selected ions with specific masses to etch materials. The benefit is twofold: it enhances the precision of etching and reduces contaminants during the process. The ability to control the ion species also allows for finer adjustments in the material removal rate, optimizing the overall performance of IBE.
Additionally, plasma-assisted ion beam etching is showing promise. By combining plasma treatments with traditional IBE, researchers improve the etching rates and the quality of the etched features. The ion bombardment is complemented by reactive species created in the plasma, leading to enhanced material removal efficiency. This integrated approach opens doors to various applications in nanostructuring and enables fabricators to tackle more complex patterns.
"The landscape of ion beam etching is being transformed through innovative techniques that redefine what's possible in materials fabrication."
Integration with Other Fabrication Techniques
The integration of ion beam etching with other fabrication techniques presents intriguing possibilities that can address the limitations of each individual method. For example, combining IBE with photolithography leads to highly controlled and precise micro- and nanoscale patterns. Photolithography lays down the initial pattern, while IBE can further refine these features, achieving dimensions that traditional photolithography alone cannot.
Moreover, merging atomic layer deposition (ALD) with IBE can yield enhanced results in creating complex structures, such as multilayer films. The layered approach allows for the deposition of materials followed by targeted etching, creating intricate patterns essential in device fabrication. This synergy enhances control over layer thickness while ensuring tight tolerances, fundamental in semiconductor applications.
In the microfabrication sector, the combination of IBE with laser ablation techniques is also under investigation. This allows for the benefit of rapid initial material removal via laser systems, followed by precise fine-tuning with ion beams. This hybrid methodology can lead to faster processing times without sacrificing accuracy, which is increasingly important in production environments.
Recent strides in this integration not only enhance overall process throughput but also open pathways for the development of novel devices with unique functionalities. The prosperity of IBE within these hybrid systems underscores its versatility as a key player in the future of advanced materials fabrication.
Future Directions of Ion Beam Etching
As the field of materials science progresses, Ion Beam Etching (IBE) stands to undergo significant transformations. The focus on future directions reveals a landscape rich with possibilities. With the continuous push for miniaturization and precision in manufacturing, understanding these trends is vital. The insights gained not only serve academic interests but also pave the way for commercial advancements. This section examines emerging applications and advancements in beam technology, reflecting the critical nature of ongoing research in IBE.
Emerging Applications
In recent years, the adoption of IBE has expanded beyond traditional boundaries. New industries are capitalizing on the unique capabilities of ion beam etching, primarily due to its exceptional precision and flexibility. Key applications that merit attention include:
- Optoelectronics: IBE is playing a crucial role in the production of photonic devices. The ability to define intricate microstructures makes it a preferred choice for engineering light paths in chips.
- Biomedical Devices: Emerging technologies in healthcare benefit from IBE's ability to create micro and nanoscale features on implants. Such customization enhances biocompatibility and functionality.
- Quantum Computing: As quantum technologies advance, IBE is vital for fabricating qubits with high fidelity. The precision offered by this technique could be a game-changer in developing more reliable quantum systems.
Notably, these applications underscore the versatility of ion beam etching in addressing diverse challenges across industries. The fusion of IBE with other fabrication methods, such as additive manufacturing and photolithography, can further broaden its horizons.
Advancements in Beam Technology
Equally exciting are the advancements in beam technology that are transforming IBE. Innovations focus on enhancing the performance of the ion beams themselves while ensuring efficiency and cost-effectiveness. Some prominent developments include:
- Higher Energy Ion Beams: Research is directing towards increasing beam energy to improve material removal rates while maintaining precision. This exploration could potentially cut processing time significantly.
- Ion Source Improvements: Novel ion sources, such as electron-cyclotron resonance and microwave discharges, are being developed. These sources promise better ionization rates and more control over ion species.
- Adaptive Beam Focusing: The development of real-time adaptive optics aims to provide dynamic focusing capabilities for the ion beams. This technology can potentially allow for better pattern fidelity over larger areas, minimizing distortion and enhancing quality.
"The evolution of ion beam technology could redefine manufacturing standards, fostering higher levels of precision and complexity in engineered materials."
Culmination
In wrapping up our exploration of ion beam etching (IBE), it is clear that this technique has carved out a vital niche in the world of materials science and nanotechnology. The precision that IBE offers in patterning is not just a luxury; it is a necessity in fields like semiconductor manufacturing where even the tiniest mistake can cascade into larger failures.
Summary of Key Points
- Definition and Importance: IBE is crucial for high-accuracy material processing, allowing for nanoscale etching and sculpting.
- Techniques and Equipment: Understanding the various ion beam sources and etching systems is fundamental for optimizing IBE outcomes.
- Applications: IBE plays a pivotal role in sectors such as semiconductor fabrication, nanotechnology, and newer fields in materials science.
- Challenges and Research: Ongoing challenges, including substrate damage and process control, have spurred innovative research aimed at refining these techniques further.
- Future Directions: Emerging applications and advancements in beam technology suggest a promising horizon for IBE, potentially leading to breakthroughs in various high-tech industries.
The Significance of IBE in Modern Research
The role of ion beam etching in modern research cannot be overstated. As technology continues to advance, the need for precision machining at microscopic scales becomes increasingly pertinent. IBE not only meets this demand but also enhances the capabilities of existing technologies. Researchers today rely on the robustness of IBE to drive innovations in electronics and material development.
"Ion beam etching serves as a bridge between theoretical possibilities in material design and practical applications in technology."
In essence, IBE stands as a testament to the evolving landscape of materials science, providing tools that open new avenues for exploration and development in various industries. The intricate balance of efficiency and precision makes IBE an indispensable technique for researchers and engineers alike, solidifying its importance in today's high-tech world.