Intergranular Corrosion Testing: Methods and Insights
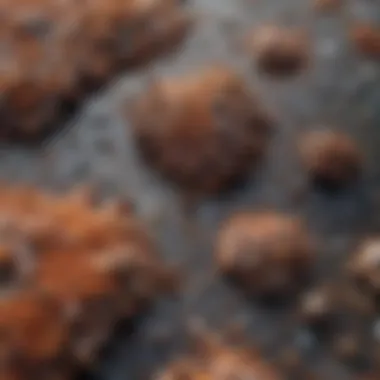
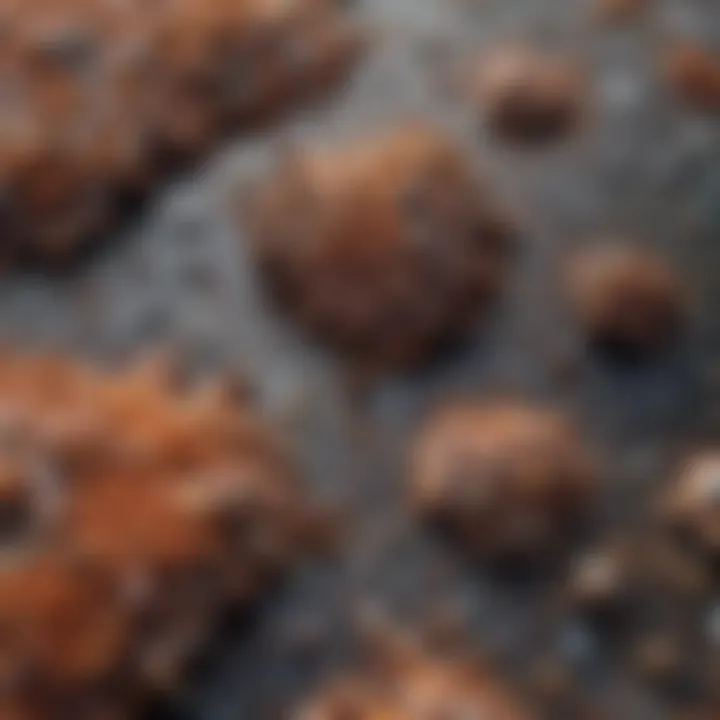
Intro
Intergranular corrosion is a subtle yet insidious form of material degradation that manifests at the grain boundaries of metals. Understanding this phenomenon is crucial, especially in industries where materials face harsh environments. The implications of intergranular corrosion are vast, impacting safety, longevity, and the overall integrity of structures. This article serves as a guide, exploring the methodologies and significance associated with testing for this type of corrosion. It will delve into not only the testing techniques but also the broader impact on various sectors, research advancements, and future challenges in corrosion management.
Overview of Research Topic
Brief Background and Context
Intergranular corrosion occurs more frequently in certain alloys, particularly in stainless steels and aluminum. This type of corrosion is often precipitated by improper heat treatment or exposure to corrosive environments. Understanding the underlying mechanisms is essential for developing effective testing methods. By examining the factors that contribute to this form of corrosion, researchers can identify vulnerable materials and engineering practices.
Importance in Current Scientific Landscape
Understanding intergranular corrosion is imperative in today's scientific and engineering environments. Many sectors, including aerospace, automotive, and energy, depend on materials that can withstand wear and degradation. Failing to recognize intergranular corrosion can lead to catastrophic failures. Thus, promoting awareness and rigor in testing methodologies is fundamental for public safety and material reliability. The ongoing advancements in research elevate this topic, ensuring that new materials meet performance standards while minimizing risks associated with intergranular corrosion.
Methodology
Research Design and Approach
Researching intergranular corrosion is a multidimensional task. The design typically involves a combination of laboratory-based experiments and field studies. Experimentation often focuses on testing materials under controlled corrosive environments. This allows researchers to simulate conditions that can lead to intergranular corrosion. Data collected provide insights into corrosion rates and the efficacy of different alloys under stress.
Data Collection Techniques
Various techniques are employed to evaluate intergranular corrosion. These can include:
- Electrochemical Testing: This technique measures corrosion potential and current to assess susceptibility.
- Optical Microscopy: Used for visual examination of microstructures before and after exposure to corrosive environments.
- Scanning Electron Microscopy (SEM): Offers high-resolution images of the material's surface, revealing specific corrosion patterns.
- X-ray Diffraction (XRD): Helps in identifying phases present in materials that may enhance susceptibility to intergranular corrosion.
"Effective testing of intergranular corrosion is essential to prevent material failure in critical applications. Understanding material behavior is key to innovation in corrosion resistance."
These diverse approaches to data collection allow researchers to build a comprehensive understanding of how different materials and conditions interact, paving the way for future advancements in material science.
Prelims to Intergranular Corrosion
Intergranular corrosion is a form of localized corrosion that occurs along the grain boundaries of materials, most notably metals. Understanding this phenomenon is essential for professionals and researchers in fields such as materials science, engineering, and structural integrity. The implications of intergranular corrosion are diverse, impacting everything from the long-term performance of components to safety and reliability in various applications.
Definition of Intergranular Corrosion
Intergranular corrosion refers to the degradation of a metal or alloy primarily along its grain boundaries. This process often occurs when metals are exposed to specific environmental conditions that facilitate the attack at the interfaces where the grains meet. At the atomic level, this type of corrosion manifests due to the different electrochemical potentials along the grain boundaries, often exacerbated by factors like alloy composition or heat treatment. For example, in stainless steel, the presence of chromium carbides can deplete chromium near the grain boundaries, leading to susceptibility to corrosion. The result can weaken the structure, rendering it less capable of withstanding stress, ultimately risking failure in applications where integrity is paramount.
Historical Context and Relevance
The study of intergranular corrosion has evolved significantly since its initial documentation. Early research focused primarily on stainless steels in harsh environments. However, as industries expanded, so too did the understanding of materials and their vulnerabilities. Today, this knowledge has reached crucial importance, particularly in sectors like aerospace, marine engineering, and chemical processing.
Understanding the historical context provides insight into why intergranular corrosion testing has become a necessity. The catastrophic failures experienced in the past underscore the urgency for comprehensive testing protocols. The relevance remains pronounced today as industries confront the challenges posed by newer alloys and more aggressive environmental conditions. As standards and regulations evolve, keeping abreast of intergranular corrosion implications ensures not only compliance but also the safeguarding of human life and the integrity of materials used in critical applications.
"Intergranular corrosion is often called silent killer of metals; it can go undetected until significant damage has occurred."
In summary, the significance of addressing intergranular corrosion cannot be overstated. Its definition establishes the groundwork for understanding its mechanisms, while the historical context emphasizes its ongoing relevance across multiple sectors. Thus, a thorough examination of testing methodologies will follow, elaborating on practical techniques to mitigate the risks and implications of this condition.
Mechanisms of Intergranular Corrosion
Understanding the mechanisms of intergranular corrosion is essential for professionals working in material science, engineering, and related fields. This type of corrosion occurs primarily at the grain boundaries of metallic materials. These mechanisms are complex and involve a combination of electrochemical processes, specific characteristics of grain boundaries, and environmental factors. Each of these elements plays a crucial role in the initiation and propagation of intergranular corrosion, affecting material performance and longevity.
Electrochemical Processes
Electrochemical processes are vital in explaining how intergranular corrosion develops. The phenomenon involves the anodic and cathodic reactions that take place at the grain boundaries. When metal alloys, such as stainless steel, come into contact with a corrosive environment, localized electrochemical reactions can occur. For example, if certain alloying elements are depleted in the vicinity of the grain boundary due to prior exposure or thermal treatment, the area becomes anodic in relation to the bulk material, leading to accelerated corrosion.
Factors like pH, temperature, and presence of chlorides also influence these electrochemical reactions. A low pH level or high chloride concentration can significantly increase corrosion rates at grain boundaries. In summary, by understanding these electrochemical mechanisms, one can better predict material performance in corrosive environments.
Grain Boundary Characteristics
The characteristics of grain boundaries are another key element in the study of intergranular corrosion. Grain boundaries can vary in composition, structure, and orientation, influencing their susceptibility to corrosion. In homogeneous materials, grain boundaries may act as barriers to corrosion, but in certain alloys, they can become preferential sites for attack.
Grain size and shape also matter. Fine-grained materials may present a larger surface area for corrosive attack, leading to higher susceptibility. Additionally, impurities or second-phase particles at grain boundaries can serve as initiation sites for corrosion.
Understanding these characteristics helps engineers in selecting and processing alloys to mitigate risks of severe intergranular corrosion. For this reason, studying the microstructural properties of grains is critical in predicting failure modes.
Environmental Factors
Environmental factors contribute significantly to the formation and progression of intergranular corrosion. Conditions such as humidity, temperature fluctuactions, and exposure to aggressive chemicals can enhance corrosion susceptibility. These factors can alter the electrochemical state of the metal and increase the likelihood of localized corrosion.
For instance, materials that are exposed to marine environments often face high chloride concentrations. This can lead to faster degradation rates at grain boundaries compared to other environments.
Moreover, changes in stress conditions, such as mechanical loading or residual stresses from fabrication, can exacerbate the effects of corrosion. Understanding these environmental influences is crucial for material selection and design, especially in applications where reliability is paramount, like aerospace and marine engineering.
Importance of Testing for Intergranular Corrosion
Testing for intergranular corrosion is crucial in materials science and engineering. As this type of corrosion can lead to severe structural failures, understanding its implications is essential for ensuring the longevity and safety of various applications. Testing allows professionals to identify susceptible materials early in the design phase or during service. Without thorough testing, the compromises in material selection may not be evident until catastrophic failures occur.
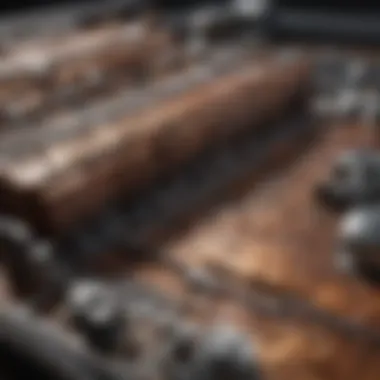
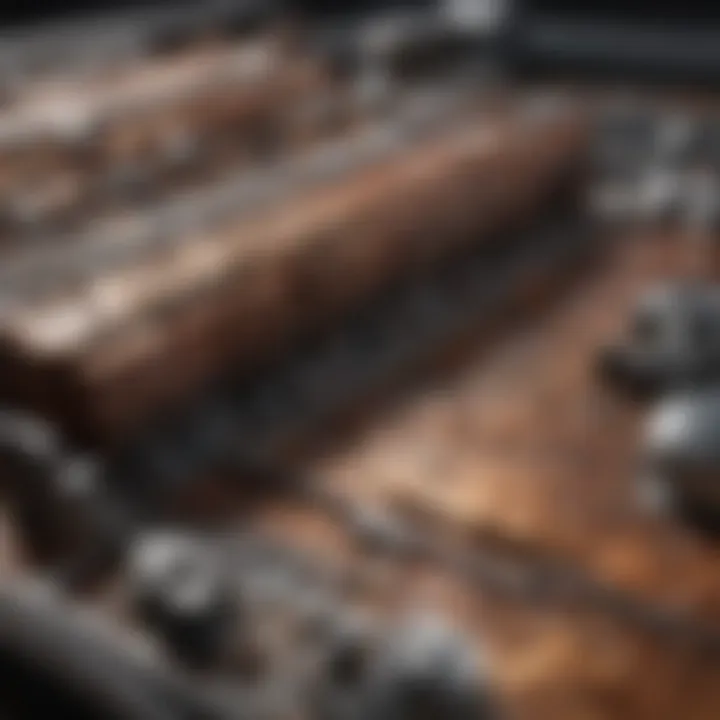
Testing helps mitigate risks associated with intergranular corrosion. It guides material choices based on functionality and environmental factors. Professionals can make informed decisions, reducing the likelihood of unexpected failures. Moreover, regular testing ensures that materials used in critical structures meet the required standards for performance. This ultimately protects the integrity of the structures and the safety of the people using them.
Impact on Material Selection
Material selection is a foundational aspect of engineering. Corrosion resistance should influence choices, especially in environmental conditions that predispose specific alloys to intergranular corrosion. Testing identifies materials that will perform well under expected service conditions. For example, Austenitic stainless steels may show susceptibility based on welding or heat treatment. When engineers are aware of these factors, they can select alternative materials or modify processing parameters to enhance performance.
Considerations for material selection based on testing results may include:
- Alloy Composition: Knowing the chemical makeup helps predict susceptibility.
- Processing Techniques: Testing outcomes influence manufacturing methods.
- Service Environment: Understanding the exposure conditions is vital.
Effective testing strategies can refine the selection process and help avoid costly mistakes. It leads to better material performance, making investments in testing essential.
Consequences for Structural Integrity
Intergranular corrosion can compromise the integrity of structural components. When it occurs, it can initiate cracks that propagate rapidly, often without any visible signs. This can lead to failures in structures like bridges, pipelines, and aircraft. The implications of such failures are serious, leading to potential loss of life or significant financial repercussions.
Failures due to intergranular corrosion can manifest in various ways:
- Unexpected Fracture: Sudden, unpredicted failures under load.
- Leaking: In critical pipelines, leaks due to corrosion can lead to environmental contamination.
- Reduction of Load Capacity: As components weaken, they can no longer carry expected loads, posing risk.
Thus, proactive testing practices are vital to ensure that the structural integrity is maintained. Regular and systematic evaluations allow for the timely identification of corrosion, allowing for maintenance or replacement before failures occur.
Regulatory and Standards Considerations
The importance of regulatory standards in corrosion testing cannot be overstated. Several organizations have set guidelines that dictate how testing should be conducted to ensure safety and reliability. Compliance with these standards is mandatory in many industries. It provides a framework for evaluating risks associated with intergranular corrosion.
Key regulations often considered include:
- ASTM Standards: These criteria provide detailed methodologies for conducting corrosion tests.
- ISO Specifications: International standards promote consistent testing processes across borders.
- Industry-specific Guidelines: Certain sectors, such as aerospace and marine, have unique requirements tailored for their challenges.
Adhering to these standards strengthens the credibility of testing results and fosters confidence in structural performance. Inadequate testing or non-compliance can lead to severe penalties and compromised safety.
Effective testing and adherence to standards are essential in preventing intergranular corrosion issues. Failure to comply may lead to safety hazards and substantial financial losses.
Common Testing Techniques
Testing for intergranular corrosion is a critical need for many industries, as it helps safeguard the integrity and longevity of structural materials. Understanding the common testing techniques carries significant weight in comprehending how different methods can unveil the susceptibility of materials to corrosion. Each technique has its own strengths and weaknesses. These testing methods serve as benchmarks, guiding material selection and informing maintenance strategies. Professionals in various fields, including aerospace, marine engineering, and chemical processing, must grasp these techniques to mitigate risks associated with intergranular corrosion.
ASTM G28 Method
The ASTM G28 method is among the most widely recognized testing standards for evaluating intergranular corrosion resistance. This methodology is specifically designed for stainless steels, primarily focusing on detecting susceptibility after processes like welding. The test involves exposing the sample to a corrosive environment, typically a boiling solution of sulfuric acid and nitric acid, for a specified duration. Following exposure, metallographic examinations help assess the extent of corrosion.
Reasons to choose ASTM G28:
- Provides a clear, reproducible framework.
- Focuses on relevant materials used in critical applications.
- Offers insights into post-weld corrosion behavior.
However, potential drawbacks include the harshness of the chemicals involved, which can limit its applicability to specific environments. There is also a risk of overemphasis on specific corrosion types, which might not represent behavior in all real-world scenarios.
ISO Standards for Corrosion Testing
ISO standards offer a diverse array of methods for corrosion testing, including specific protocols targeting intergranular corrosion. These standards promote a harmonized approach, facilitating global communication among researchers and engineers. The ISO 15156 series is notably relevant, as it sets requirements for materials used in oil and gas production environments, focusing on corrosion under oil field conditions.
Benefits of ISO standards include:
- Global recognition and adoption.
- Adaptability to different materials and environments.
- Rigorous protocols that enhance the reliability of results.
That said, implementation can sometimes be cumbersome. Understanding and adhering to the standard's requirements may involve a learning curve for organizations new to corrosion testing. Additionally, these standards may not entirely address unique challenges present in specific industries, making it essential to supplement with other methodologies.
Electrochemical Testing Methods
Electrochemical testing methods are instrumental for in-situ assessments of corrosion behavior. Techniques such as potentiodynamic polarization and electrochemical impedance spectroscopy allow for real-time monitoring of material reactions under actual service conditions. These methods provide pertinent data on corrosion rates, passivation behaviors, and overall material performance.
Key aspects of electrochemical methods:
- Non-destructive testing allows for the preservation of samples after assessment.
- Rapid data acquisition offers real-time insights into corrosive conditions.
- Versatility in application across various materials, including alloys and coatings.
Despite these advantages, electrochemical methods may require specialized equipment and trained personnel to conduct the tests effectively. Additionally, data interpretation can be complex, needing advanced knowledge to derive practical conclusions from the findings.
"Effective corrosion testing is not merely about choosing a method; it involves understanding the implications, limitations, and specific needs of the material being analyzed."
In summary, common testing techniques form the backbone of intergranular corrosion assessment. By leveraging methods like ASTM G28, ISO standards, and electrochemical approaches, industries can develop a comprehensive strategy to address corrosion challenges. This knowledge base lays the groundwork for informed decision-making in material selection and maintenance practices.
Material-Specific Testing Considerations
Material-specific testing considerations play a vital role in understanding intergranular corrosion. Each material behaves uniquely under different environmental conditions. It is crucial to address the specific characteristics of the materials used in various industries. Focusing on the nuances of testing helps optimize performance, ensure safety, and prolong the lifespan of structures.
Stainless Steel Corrosion Testing
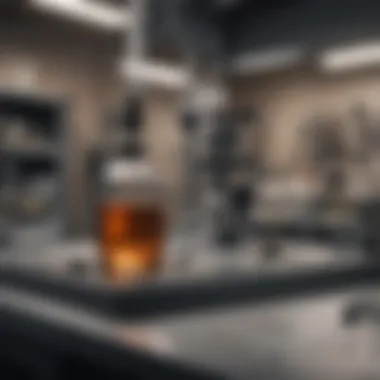
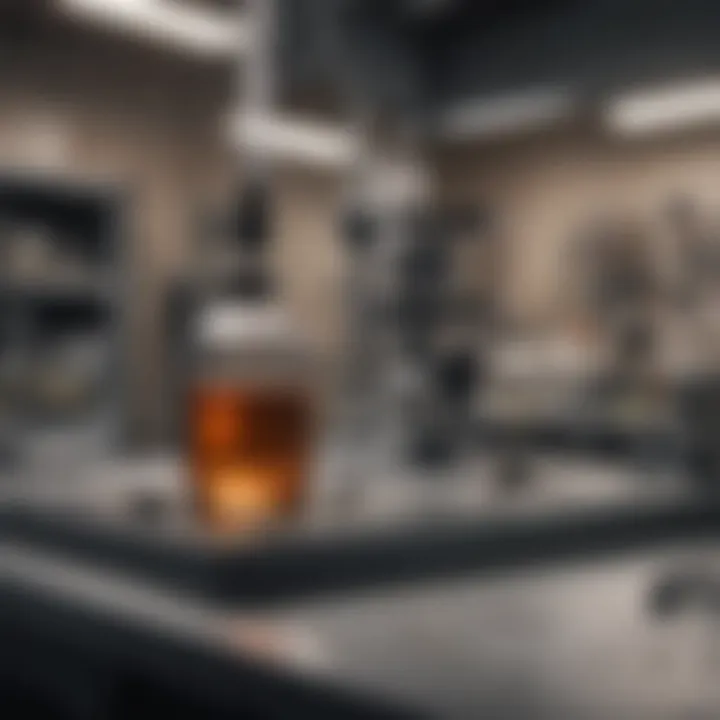
Stainless steel is highly regarded for its corrosion resistance. However, this material is not immune to intergranular corrosion, especially in certain grades. For instance, the presence of chromium carbides at grain boundaries can diminish corrosion resistance. Testing for intergranular corrosion in stainless steel typically involves methods like the ASTM A262 test. This test examines microstructures to reveal potential weaknesses. Also, sulfide stress cracking in high-strength stainless steels has added complexity to this issue, requiring careful evaluations.
Careful interpretation of test results is critical to ensure the durability of stainless steel products. Understanding these facets allows for better material selection and processing techniques.
Aluminum Alloys and Corrosion Susceptibility
Aluminum alloys are commonly employed in industries such as aerospace and automotive. Nonetheless, their susceptibility to intergranular corrosion cannot be overlooked. Alloy composition, especially the amount of copper and magnesium, affects how these materials react under corrosive conditions. Testing protocols aim to reveal the characteristics of specific alloy formulations.
An essential technique includes the use of potentiodynamic polarization. This method discloses critical information about the corrosion mechanisms at play. Monitoring the pit initiation and progression within the alloy helps researchers identify the materials' limitations.
Visual inspections and microstructural analysis are also important, as they can help predict performance in the field. This attention to detail in testing can help manufacturers refine their alloy mixtures, leading to enhanced durability.
Nickel Alloys in Corrosive Environments
Nickel alloys are renowned for their resilience in harsh environments, making them suitable for chemical processing and marine applications. However, even these robust materials are not exempt from intergranular corrosion challenges. Nickel alloys' performance can be influenced by factors such as temperature, concentration of corrosive agents, and stress levels.
Testing for intergranular corrosion in nickel alloys is often carried out using methods like the ASTM G48 test. This test provides insights into the material's resistance under specific conditions. Additionally, electrochemical tests can help analyze localized corrosion behavior.
Given the high cost of nickel alloys, accurate testing is paramount. Failure to detect intergranular corrosion could lead to catastrophic failures in critical applications. Thus, continuous advancement in testing methods is necessary to ensure the functionality and reliability of nickel materials in corrosive environments.
Emerging Trends in Intergranular Corrosion Research
Emerging trends in intergranular corrosion research are vital for advancing materials science and engineering practices. Understanding these trends helps professionals in various industries mitigate risks associated with corrosion. Innovations in research can drive solutions that enhance longevity and performance of structural materials.
Nanostructured Materials and Corrosion Resistance
Nanostructured materials are gaining attention due to their unique properties that can improve corrosion resistance. Materials at the nanoscale often demonstrate better mechanical properties and can form more protective oxide layers.
Research indicates that by modifying the grain size at the nanometer scale, it is possible to create materials that resits intergranular corrosion more effectively. Such modifications can lead to improved durability, especially in critical environments such as aerospace or marine applications. Key benefits of this approach include:
- Enhanced Strength: The smaller grain sizes contribute to overall mechanical strength.
- Improved Resistance: Greater resistance to localized corrosion processes occurs.
- Tailored Properties: Materials can be designed specifically for rigorous conditions.
Advancements in Alloy Development
Advancements in alloy development have led to the creation of new materials that are less susceptible to intergranular corrosion. Researchers are focusing on optimizing the composition of alloys to balance corrosion resistance with mechanical performance. For example, advancements in stainless steel alloys are directly targeting susceptibility to sensitization, which is a cause of intergranular corrosion.
New approaches in alloy development include:
- Reduced Chromium Content: Some studies show that lower chromium content can reduce sensitivity while maintaining corrosion resistance.
- Buffering Elements: Adding other elements like titanium or niobium can stabilize the microstructure.
- Meta-alloy Systems: Combining different alloy systems can lead to enhanced resistance against specific corrosion forms.
These advancements not only contribute to reliability but also extend the life cycle of materials, which is crucial for safety-focused industries.
Novel Testing Techniques
The innovations in novel testing techniques are also crucial in the realm of intergranular corrosion. Traditional methods often fall short in providing comprehensive insights into corrosion behavior under realistic conditions. New methods aim to mimic operational environments more closely.
Techniques such as in-situ monitoring and more advanced imaging technologies allow for:
- Real-Time Data Collection: Continuous monitoring yields instant feedback on corrosion processes.
- Improved Imaging: High-resolution imaging techniques enhance the ability to understand microstructural changes.
- Better Predictive Models: Advanced data analysis, including machine learning, aids in predicting corrosion trends based on historic data.
In summary, these trends indicate a strong focus on both materials and testing methodologies, driving forward the study and practical understanding of intergranular corrosion.
"Emerging technologies in corrosion research provide opportunities for enhanced material performance and longevity in critical applications."
Intergranular corrosion is no longer only a concern but becomes a focus of innovation, shaping the future of materials used across industries.
Case Studies in Intergranular Corrosion Testing
Intergranular corrosion testing plays a critical role in various industries as it helps identify material weaknesses that may not be evident during routine inspections. Each case study provides insights into different applications of testing methods and their significance in real-world scenarios. Understanding these contexts is essential not only for researchers but also for engineers and professionals committed to maintaining the integrity and safety of structures. Insights gained from these studies help in refining testing techniques and material choices, leading to enhanced safety standards across industries.
Aerospace Industry Applications
In the aerospace sector, the stakes are particularly high. Aircraft components are subject to extreme conditions, and failure due to intergranular corrosion can result in catastrophic outcomes. For instance, a case study focusing on aluminum alloys used in aircraft frames revealed that susceptibilities often occurred unnoticed. The ASTM G28 method was applied to identify intergranular corrosion in these critical components. By mapping the corrosion resistance of various alloy compositions, engineers could refine material selections, ensuring higher safety margins.
Implications for the aerospace industry include
- Enhanced component life
- Compliance with stringent regulatory standards
- Reduction in maintenance costs due to early detection and preventative actions.
This case illustrates how a focused approach to testing can bolster safety and ensure long-term performance in highly regulated environments.
Marine Engineering Contexts
Marine environments are notorious for their corrosive conditions. Here, stainless steels often face intergranular corrosion due to exposure to saltwater and varying temperatures. A noteworthy case study investigated the failure of a marine substructure due to unsuspected intergranular corrosion. Testing methodologies, including ISO 15156, highlighted specific factors contributing to the corrosion.
The following key points emerged from this study:
- The importance of environmental assessments in defining material performance
- Detailed insights into grain boundary characteristics that heighten susceptibility to corrosion
- Strategies for corrosion mitigation through better material selection and protective coatings.
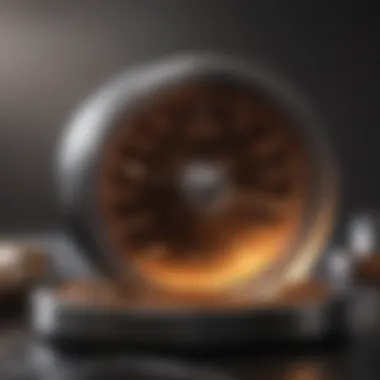
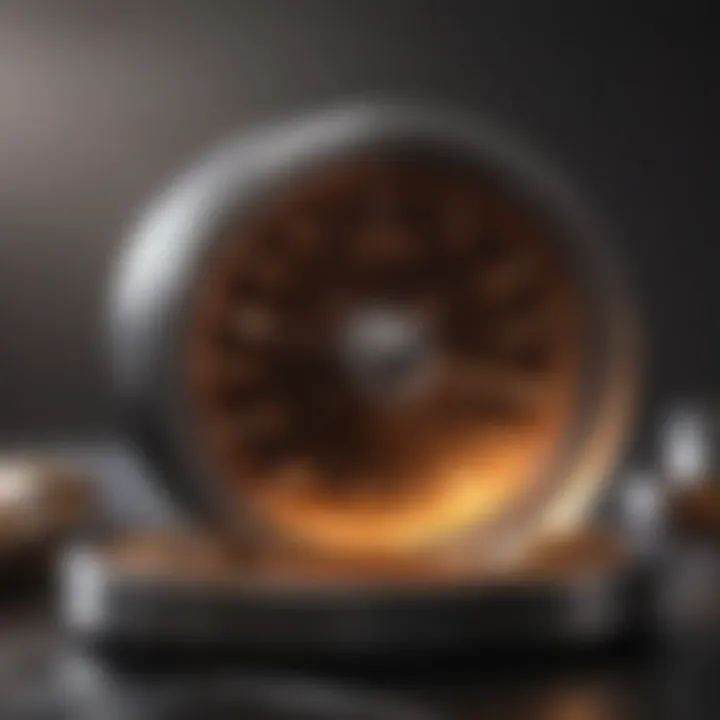
This research underlines the need for careful testing and analysis in marine contexts to avoid significant losses and ensure structural integrity.
Chemical Processing Facilities
Chemical processing facilities handle aggressive environments with various corrosive substances. A case study simulated conditions typical in petrochemical plants. The findings showed a prevalent extent of intergranular corrosion on certain stainless steel grades used in piping systems.
Utilizing electrochemical testing methods, operators understood the correlation between specific chemical exposures and intergranular corrosion tendencies. Benefits observed included:
- Development of corrosion-resistant alloys tailored for specific plant conditions
- Identification of maintenance schedules based on real-time corrosion data
- Improved safety protocols
This case emphasizes the need for continuous monitoring, highlighting how real-time testing can help avoid costly accidents and enhance operational efficiency.
Understanding each unique case provides a foundation for improving practices across industries. Intergranular corrosion testing is evolving, and the implications extend far beyond just identifying material failures; they guide innovations in materials science.
In summary, these case studies underscore the adaptability and essential nature of intergranular corrosion testing. Concrete examples from the aerospace sector, marine engineering, and chemical processing illustrate the techniques' practical impact, shaping future research and development in structural integrity.
Challenges in Intergranular Corrosion Testing
Intergranular corrosion testing faces various challenges that affect the accuracy and reliability of results. Understanding these challenges is vital for engineers and scientists who work with materials prone to this form of corrosion. Several elements contribute to these challenges, including limitations of current testing methods, complexities in interpreting results, and issues surrounding costs and resource allocation.
Limitations of Current Methods
Testing methods for intergranular corrosion often show limitations that can hinder effective evaluation. For instance, traditional testing techniques may not assess all types of alloy compositions comprehensively. Some methods only apply to specific materials, such as stainless steels, and may not suit other alloys like aluminum or nickel.
Moreover, many tests are conducted in controlled laboratory environments, which may not fully replicate real-world conditions. Environmental factors, such as temperature and exposure to corrosive agents, can affect the corrosion process differently outside the lab. This limitation underscores the need for more versatile and adaptive techniques in corrosion assessment. Important testing methods like ASTM G28, despite being widely utilized, may fail to address all aspects of intergranular corrosion, leaving room for improvement.
Interpreting Test Results
Interpreting outcomes from corrosion tests can be complex. Different alloys show varied behaviors under similar conditions, making it hard to predict how a specific material will perform over time. Results can also be influenced by numerous factors, including microstructure and the presence of precipitates at grain boundaries.
Another aspect complicating interpretation is the potential for localized damage that may not be adequately reflected in test results. For example, a material might pass standardized tests but still fail prematurely in actual service due to hidden defects or future environmental changes. Such discrepancies can lead to misjudgments of a material's durability.
"Interpreting corrosion test results requires a holistic approach, considering not just the figures but the inherent characteristics of the material in context."
Costs and Resource Allocation
The economic implications of intergranular corrosion testing cannot be overlooked. Testing can be costly. Advanced methods may require specialized equipment and trained personnel, adding to resource allocation concerns. Companies may face budget constraints that limit their ability to perform sufficient testing on all materials.
In addition, time spent on testing must be balanced with production deadlines. Ensuring thorough testing might slow down manufacturing processes, creating tension between quality assurance and operational efficiency. Thus, a strategic approach must be taken to allocate resources efficiently while maintaining high standards in testing processes.
In summary, recognizing the challenges in intergranular corrosion testing is essential for improving practices in this field. By addressing limitations, enhancing the interpretation of results, and managing costs, stakeholders can better safeguard material integrity in various applications.
Future Directions in Intergranular Corrosion Research
The field of intergranular corrosion research is evolving rapidly, driven by the need for enhanced material performance and longevity in various applications. Recognizing the intricacies of this type of corrosion is essential for ensuring structural integrity across a diverse array of industries. Future directions in this area focus on integrating advanced technologies, conducting comprehensive studies over longer time frames, and fostering cross-industry collaborations. Each aspect presents opportunities to enhance our understanding and management of intergranular corrosion, ultimately leading to better material choices and longer-lasting structures.
Integration of Machine Learning in Corrosion Prediction
Machine learning has emerged as a potent tool in many fields, and corrosion prediction is no exception. The application of machine learning algorithms offers a new path for forecasting intergranular corrosion susceptibility based on various input parameters. By analyzing extensive datasets, these algorithms can identify patterns and correlations that might be overlooked by traditional methods. This predictive capability enables early intervention and targeted treatment strategies, which can significantly improve material lifespan and reduce maintenance costs.
Moreover, machine learning applications can optimize the design process for new materials by predicting their behavior under specific environmental conditions. The integration of real-time data and machine learning can lead to more robust corrosion management practices, facilitating proactive rather than reactive approaches to this pervasive issue.
Long-term Field Studies
Conducting long-term field studies is crucial for accurately assessing the performance of materials in natural environments. These studies can provide invaluable insights into how intergranular corrosion develops over extended periods, revealing the effects of different environmental factors such as humidity, temperature, and chemical exposure.
The results from such studies can guide better design and material selection practices. Understanding how materials behave over time allows researchers to accurately model potential failure points and implement appropriate mitigation strategies. Additionally, long-term data collection fosters the development of guidelines and standards that can inform industry best practices.
Collaborative Efforts Across Industries
Collaboration among various industries is an imperative avenue for advancing research on intergranular corrosion. Different sectors, such as aerospace, marine, and chemical processing, face unique challenges related to corrosion. By sharing insights and techniques, these sectors can collectively address the complexities posed by intergranular corrosion.
Collaboration may take the form of joint research initiatives, sharing of testing methodologies, or the development of universal standards. These efforts can lead to more informed material choices and enhanced designs, ultimately ensuring safer structures. Additionally, industry collaboration can accelerate the adoption of innovative technologies, such as advanced coatings and materials that exhibit electrochemical stability.
The End
The conclusion serves as a pivotal moment in this discussion of intergranular corrosion testing. It enables the consolidation of various insights gathered throughout the article. Understanding the mechanisms and implications of intergranular corrosion is essential not only for engineers but also for researchers and students within the field of materials science.
Here are some specific elements that underscore the importance of this topic:
- Holistic Understanding: Comprehensive coverage aids in grasping complex interactions between materials and their environments. This understanding is crucial for effective material selection.
- Industry Relevance: By outlining the implications for various sectors such as aerospace, marine engineering, and chemical processing, the article emphasizes how fundamental testing is to ensuring material integrity under real-life conditions.
- Future Directions: Identifying challenges and emerging trends prepares stakeholders to adapt to new developments. Incorporating machine learning in research, for instance, could revolutionize corrosion prediction methodologies.
- Regulatory Compliance: The discussed standards and methods are integral for adhering to regulations that safeguard public safety. An awareness of the necessary tests can prevent catastrophic failures in critical applications.
Understanding these elements can lead to better practices in the industry, thereby promoting safety and durability in materials subjected to corrosive environments.
Summary of Key Findings
The analysis provided in this article reveals the necessity of rigorous testing methods for intergranular corrosion. The examination of established methodologies such as ASTM G28 highlights their effectiveness in identifying corrosion susceptibility in different materials. Moreover, understanding specific material behaviors e.g., stainless steel and aluminum alloys, further enriches our comprehension of the problem. The emerging trends, like advancements in alloy development and novel testing approaches, are critical in addressing ongoing and future challenges in corrosion management.
Final Thoughts on Intergranular Corrosion Testing
To conclude, intergranular corrosion testing significantly contributes to the broader goals of materials science and engineering. It is crucial to appreciate that intergranular corrosion can lead to severe structural failures. Therefore, proactive testing is not just beneficial; it is necessary to prevent material degradation and ensure structural integrity. Continued research and development in this field not only enhance our understanding but also provide the tools needed to mitigate risks associated with corrosion. The collective efforts in improving testing techniques and standards will pave the way for safer, more reliable structures in various industries.
"Understanding intergranular corrosion testing is vital for maintaining the integrity of structures that rely on treated metals in harsh environments."
In summary, the journey towards mastering intergranular corrosion testing is ongoing. Collaborations across disciplines will foster innovations that can address complex challenges while ensuring that safety remains a top priority.