Flow It: A Deep Dive into ALC Flowable Composites
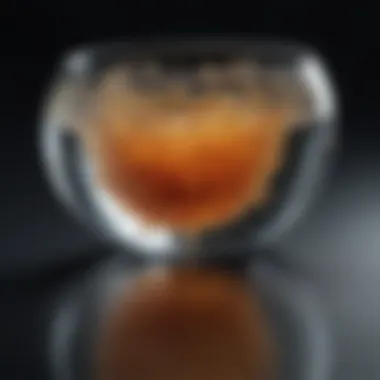
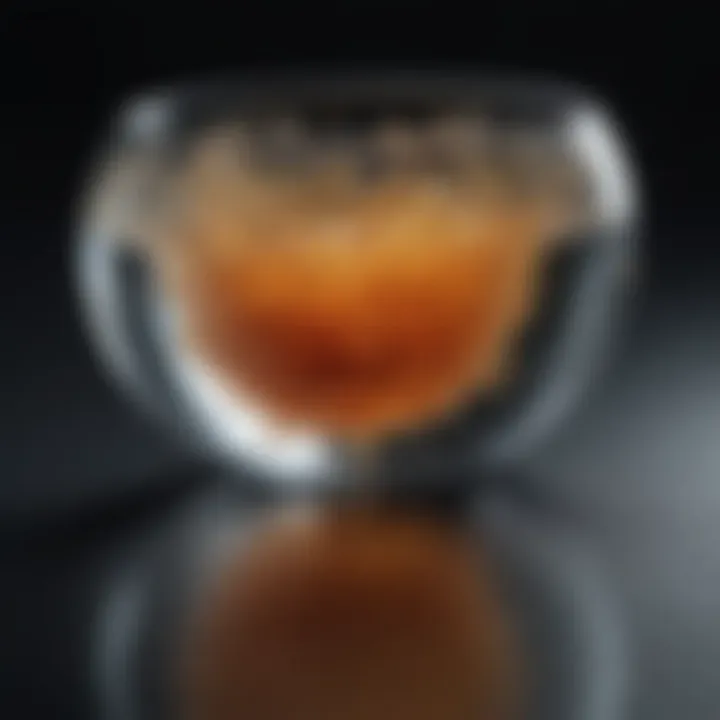
Overview of Research Topic
Brief Background and Context
ALC flowable composites represent a significant development in material science. These materials combine the benefits of traditional composites with enhanced flowability, allowing for a diverse range of applications. Unlike conventional composites, which can be challenging to mold and shape, ALC flowable composites can fill complex geometery with ease. This property makes them particularly valuable in the construction and manufacturing sectors. The material is often composed of a blend of resins and filler materials, which contribute to its unique characteristics. Understanding the characteristics of ALC flowable composites is crucial for professionals working in engineering and material science.
Importance in Current Scientific Landscape
The significance of ALC flowable composites cannot be understated. As industries move towards more efficient and sustainable practices, the adaptability of these materials has captured the attention of researchers and manufacturers alike. With rapid technological advancements, the demand for materials that support innovative designs while maintaining structural integrity has grown.
"ALC flowable composites are redefining the boundaries of material application in modern engineering and construction.”
Both academics and professionals need to stay informed about trends and research surrounding ALC flowable composites to harness their full potential in their projects.
Methodology
Research Design and Approach
The analysis of ALC flowable composites is primarily based on a review of existing literature, as well as an examination of case studies from various industries. This approach allows for an in-depth understanding of the properties and applications of these materials. Researchers employ qualitative and quantitative methods to evaluate the effectiveness and performance of ALC flowable composites in real-world scenarios.
Data Collection Techniques
Data for this comprehensive analysis has been gathered through peer-reviewed journals, industry reports, and expert interviews. Key metrics such as durability, cost-effectiveness, and long-term performance are central to the discussion. Collaborations with manufacturing firms provide practical insights into how ALC flowable composites are used in current projects. Additionally, a survey of recent market trends sheds light on the product's growing popularity.
With this groundwork, the subsequent sections will explore the diverse characteristics, applications, advantages, and challenges of ALC flowable composites.
Prelude to ALC Flowable Composites
ALC flowable composites represent a significant advancement in material science and engineering. Their unique characteristics make them particularly suitable for a variety of applications in modern manufacturing and construction. This introduction sets the stage for understanding the underlying principles, historical progression, and practical implications of these materials.
Flowable composites are distinguished by their capacity to be easily manipulated and shaped into complex forms, a property that is crucial in industries where precision and versatility are paramount. These materials combine the benefits of traditional composites—such as strength and durability—with enhanced flow characteristics. As a result, they can be applied in settings that demand not only mechanical resilience but also intricate assembly and application processes.
The importance of ALC flowable composites lies in their adaptability. They cater to diverse sectors, ranging from construction to automotive and aerospace. Thus, understanding their properties and potential applications is essential for professionals, educators, and students who are involved in material science.
ALC flowable composites offer a compelling alternative to traditional materials, providing enhanced efficiency and performance in various use cases.
In this article, we will delve into the definitions, historical utilization, and the unique physical and chemical properties of ALC flowable composites. Analyzing these aspects will offer a comprehensive view of why these materials are gaining traction across multiple industries.
Defining Flowable Composites
Flowable composites are defined as composite materials designed to flow easily when applied. These composites typically consist of a polymeric matrix combined with various fillers and additives that alter their viscosity and other mechanical properties. The essential feature of these materials is their ability to conform to shapes and contours, which is particularly beneficial in applications requiring detailed worksmanship.
The composition plays a crucial role in determining the flow characteristics of these composites. ALC flowable composites, for instance, exhibit excellent moldability and can be modified according to specific requirements. This means that they can be customized for particular scenarios, enhancing their utility significantly. Their flowability provides a competitive edge in manufacturing and construction processes.
Historical Context
The evolution of flowable composites can be traced back to advancements in polymer technology during the 20th century. Initial developments focused on improving the mix of plastic materials and reinforcements to create compounds that could resist various environmental challenges.
As industries explored new ways to improve efficiency, researchers began investigating how various materials could be engineered to provide optimal flow characteristics without sacrificing structural integrity.
By the early 21st century, materials such as ALC flowable composites began to emerge as valuable contributors, particularly in construction and manufacturing sectors. Their introduction has reshaped the landscape, encouraging continuous research and development efforts to refine their properties and applications.
Physical Properties of ALC Flowable Composites
Understanding the physical properties of ALC flowable composites is vital. These properties dictate performance, usability, and effectiveness in various applications. When discussing flowable composites, it is essential to consider how viscosity, adhesion, and durability reflect the practical advantages these materials offer. The insights into these physical characteristics differentiate ALC composites from more conventional materials.
Viscosity and Flow Characteristics
Viscosity plays a crucial role in the field of flowable composites. ALC composites exhibit low viscosity, allowing for smooth flow and easy application. This characteristic is important during installation, as it facilitates the filling of complex shapes and voids. Additionally, lower viscosity contributes to better workability, which is essential in situations requiring precision for construction or automotive applications.
Measurement protocols for viscosity often involve the use of rotational viscometers. Such methods provide detailed information that designers and engineers can use to optimize formulations. This enables the adjustment of viscosity levels based on different application methods such as casting or extrusion. Thus, understanding viscosity aids in creating effective and user-friendly materials that can adapt to various environments.
Cohesion and Adhesion Properties
Cohesion and adhesion are integral to the performance of ALC flowable composites. Cohesion refers to the attraction between molecules within the composite material. High cohesion in ALC composites leads to improved structural integrity, diminishing the likelihood of cracks or failures.
Adhesion, on the other hand, is about how well the composite bonds to different substrates. Effective adhesion enhances durability and longevity, making these materials suitable for tough applications like roadways or structural components. Evaluating adhesion often involves standardized tests that measure the bond strength to various surfaces. For instance, applying stress tests can reveal how well ALC composites maintain their integrity under load.
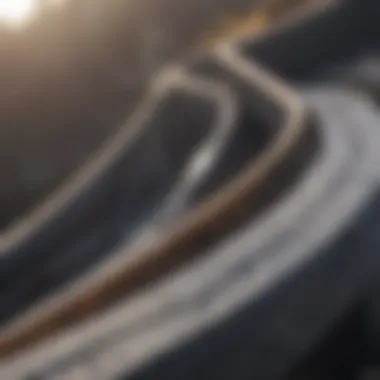
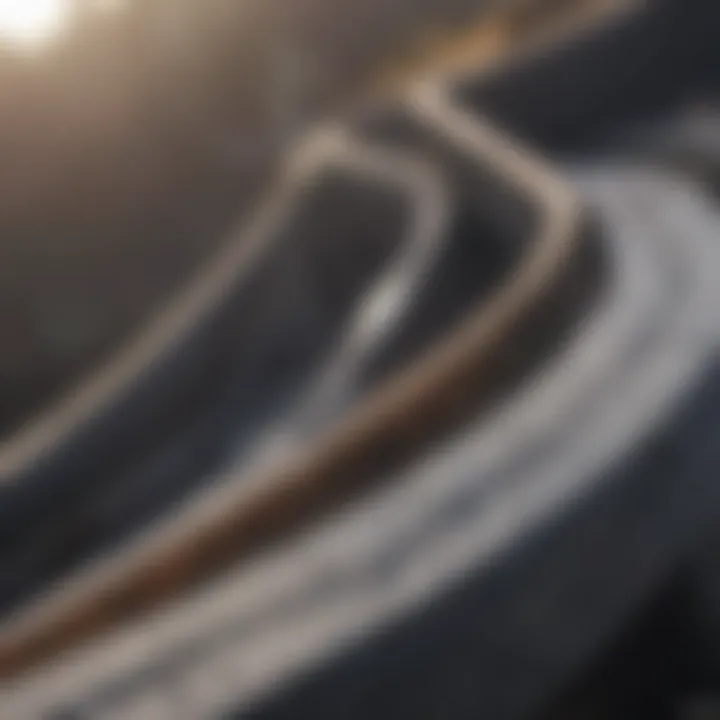
Durability and Longevity
Durability is a critical consideration for any material, and ALC flowable composites are no exception. The lifespan of these composites is influenced by several factors including environmental exposure, mechanical stress, and material composition. ALC composites generally offer good resistance to weathering, thermal cycling, and chemical exposure.
Localized testing can help assess performance under specific conditions. For instance, exposing samples to extreme temperatures and moisture can simulate real-world scenarios. Results from such experiments guide engineers in determining long-term stability. The combination of cohesion, adhesion, and overall durability ensures that ALC flowable composites maintain their structural integrity over time. This reliability ultimately leads to enhanced performance in applications ranging from construction to automotive manufacturing.
Viscosity, cohesion, and durability form the backbone of ALC flowable composites, allowing for effective and reliable applications across a wide range of industries.
Chemical Composition of ALC Flowable Composites
Understanding the chemical composition of ALC flowable composites is essential. It determines not only the mechanical properties but also the performance characteristics of the material in various applications. The right chemical makeup enhances properties such as durability, workability, and adhesion. Moreover, it enables manufacturers to tailor the composite for specific uses in construction, automotive, and aerospace industries.
Polymeric Base Materials
The polymeric base materials used in ALC flowable composites play a crucial role in defining their overall characteristics. These materials often form the matrix that holds the composite together. Common polymers include epoxy, polyurethane, and polyester resins. Each polymer has unique attributes. For example, epoxy resins are known for their exceptional adhesive strength and chemical resistance. Polyurethane, on the other hand, offers flexibility and toughness, making it suitable for applications demanding higher elongation.
The choice of polymer significantly influences the end product’s performance. A well-optimized polymer matrix can enhance the durability and lifespan of the composite.
Fillers and Additives
Fillers and additives are important components in ALC flowable composites too. They enhance the properties of the base polymer, offering benefits such as improved thermal stability and mechanical strength. Fillers like silica and calcium carbonate not only reduce material costs but also influence viscosity, enabling better flow characteristics during application.
Additives may include plasticizers, which enhance flexibility, or retardants, which can slow down curing times. Each additive has a function that contributes to the performance profile of the composite. Understanding the appropriate types and quantities of fillers and additives is essential for achieving desired properties in the final product.
Manufacturing Processes
The manufacturing processes employed in the production of ALC flowable composites are critical for ensuring the material's quality and performance. These processes encompass the steps that contribute to the characteristics of the final product, influencing its application across various industries. By understanding the manufacturing methods, professionals can improve outcomes, reduce costs, and optimize performance.
Preparation Techniques
Preparation techniques are vital in determining how well the components of the flowable composite will interact. ALC flowable composites generally require precise ratio mixing of polymeric materials and fillers. Commonly, the preparation begins with thorough cleaning of all equipment and surfaces to prevent contamination. The raw materials need to be pre-measured accurately to maintain consistency and quality in the final mix.
Often, the mixing process involves the use of high-shear mixers. These mixers ensure that ingredients are uniformly incorporated, enabling an even distribution of fillers and additives, which significantly impacts the composite's properties. Maintaining specific temperature conditions during mixing can also enhance the chemical interactions among materials.
Another crucial aspect is the quality control checks during preparation. Monitoring the viscosity and flow characteristics at various stages helps to preempt any issues that may arise during application.
Application Methods
Application methods for ALC flowable composites are diverse and tailored to specific use cases. These methods dictate how the material is placed and often influence its performance and durability. Common application techniques include pouring, spraying, or using specially designed applicators.
The choice of application method can depend on the complexity of the target surface and the desired finish. For example, spraying might be more efficient for large surface areas, while pouring may be ideal in confined spaces. Maintaining a consistent temperature and controlling humidity during application is also crucial, as fluctuations can affect the curing process and final outcome.
Training personnel in the proper application techniques is essential to avoid common pitfalls, such as uneven distribution or premature curing. It ensures that the material adheres correctly and functions as expected in the long term.
Curing and Setting Processes
Curing and setting processes are the final stages that significantly affect the mechanical and physical properties of ALC flowable composites. Curing involves chemical reactions that solidify the composite, transforming it into a durable material. The time and conditions under which curing occurs can vary based on the formulation used.
Methods for curing can include room temperature curing or using heat sources for accelerated setting. During this period, monitoring the environment is important. Ambient temperature and humidity can greatly impact curing times. Too much humidity can lead to improper hardening and potential defects in the material's structure.
Post-curing processes, which can include heat treatments or controlled cooling, may be used to enhance properties like strength and impact resistance. These treatment phases ensure that the composites meet the required specifications for their intended applications.
Curing is not just a final step; it is a critical phase that defines the long-term viability of ALC flowable composites in real-world applications.
Applications of ALC Flowable Composites
The significance of ALC flowable composites can be observed in a wide range of applications across multiple industries. These composites bring unique properties that make them beneficial for contemporary use in both manufacturing and construction. A thorough examination of these applications reveals their versatility, efficiency, and performance advantages over traditional materials.
Construction Industry Uses
In the construction sector, ALC flowable composites are utilized primarily for their excellent workability and adhesion characteristics. These composites facilitate smooth application, allowing for faster project completion. For example, they are commonly used in repair works, such as filling cracks in structures or resurfacing roads. Their fluid nature ensures they can be easily applied in hard-to-reach areas. Additionally, they offer reduced waste during application, which is an essential consideration in environmentally conscious building practices. The composites also withstand weathering and provide durable solutions in structures exposed to various elements.
Automotive Sector Applications
The automotive industry leverages ALC flowable composites in manufacturing processes and repairs due to their lightweight properties. Using these materials contributes to the overall reduction in vehicle weight, which enhances fuel efficiency. Flowable composites are especially popular in the production of body panels, where they provide strength without adding significant mass. Their ability to resist impacts while maintaining flexibility makes them valuable in crash protection systems. Furthermore, repair shops find flowable composites ideal for mending vehicle parts with precision, ensuring quality and longevity in fixes.
Aerospace and Beyond
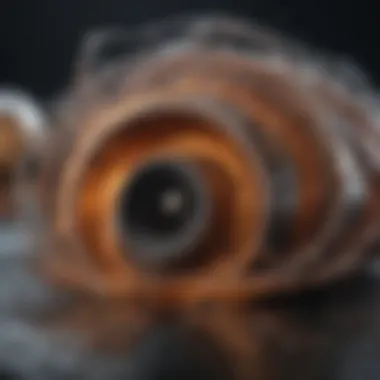
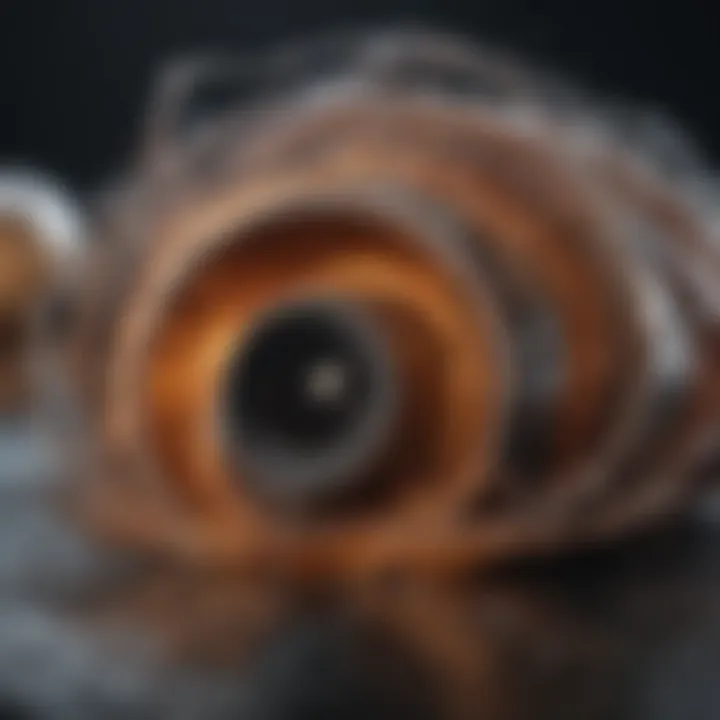
In aerospace applications, ALC flowable composites are harnessed for their high strength-to-weight ratio and thermal stability. These properties are vital in aircraft manufacturing, where every gram counts. Flowable composites facilitate the creation of lightweight structural components, enabling more efficient flight mechanics. Moreover, the aerospace sector often requires materials that can endure extreme conditions, and ALC composites meet these demands exceptionally well. Beyond aerospace, sectors such as marine and military are beginning to recognize the advantages of these materials, using them for structures requiring both resilience and adaptability.
ALC flowable composites represent a transformative shift in material science, impacting how industries approach design and efficiency.
With the advancement of technologies and growing environmental concerns, the use of ALC flowable composites is likely to increase. Their applications extend well beyond current capacities, suggesting potent future possibilities in various fields.
Advantages of ALC Flowable Composites
ALC flowable composites bring several distinct advantages to various sectors, especially in construction and manufacturing. Understanding these benefits is crucial as it highlights why these materials have gained significant attention in contemporary applications. Their unique properties not only improve material performance but also lead to more efficient processes, making them indispensable in today’s competitive landscape.
Enhanced Workability
The enhanced workability of ALC flowable composites is one of their most significant advantages. The formulation allows for easier manipulation during application, especially in intricate designs and hard-to-reach areas. ALC composites exhibit lower viscosity compared to traditional composites, resulting in smoother and more controlled pouring and spreading. This quality minimizes the effort involved in shaping and finishing, leading to faster project completion times.
Moreover, the smooth consistency aids in the incorporation of intricate features without compromising structural integrity. For workers in the field, this translates into improved efficiency, reducing labor costs and increasing productivity. Improved workability not only appeals to contractors but also ensures that end products are of higher quality due to fewer defects during application.
Reduced Waste in Application
Another notable advantage of ALC flowable composites is their potential to significantly reduce waste during usage. Traditional materials often lead to excess by requiring careful measurement and application techniques. In contrast, ALC composites conform more closely to the desired specifications and flow into place without leaving much excess material behind.
This reduction in waste contributes to cost savings and can also reduce the environmental impact associated with material disposal. As sustainability becomes a priority in many projects, the efficient use of resources in ALC composite applications aligns with these goals. Less waste means that more projects can be completed with fewer raw materials, enhancing the overall efficiency of construction zones.
Versatility in Design
Versatility is yet another key feature of ALC flowable composites. These materials can be tailored for a wide range of applications, from simple structures to complex architectural innovations. Builders can optimize composites with various additives to enhance specific characteristics like strength, flexibility, or resistance to environmental factors.
This adaptability allows for innovation in design, enabling architects and engineers to push boundaries without the limitations that often accompany conventional materials. Projects can benefit from customized solutions that meet specific structural or aesthetic requirements. The ability to create diverse textures and finishes also makes ALC composites a desired choice for creative applications, extending their use beyond traditional settings.
"ALC flowable composites revolutionize the way we think about material application in various industries, paving the way for innovation and efficiency."
In summary, the advantages of ALC flowable composites are significant and multifaceted. Enhanced workability aids application ease, reduced waste leads to cost-efficiency, and versatile design opportunities allow for creative freedom. Understanding these benefits is critical for professionals seeking to improve their processes and outcomes.
Challenges and Considerations
In any discussion about ALC flowable composites, the topic of challenges and considerations naturally arises. Understanding these factors is vital for those looking to incorporate these materials into their work, whether in manufacturing, construction, or research. It provides a clearer picture of the landscape, enabling informed decision-making.
Cost Factors in Production
The production of ALC flowable composites presents notable cost factors that cannot be overlooked. Initially, the investment in the raw materials comprises a significant portion of the production costs. High-quality polymeric bases and fillers are essential to ensure optimal performance. As a result, sourcing these materials often requires careful evaluation to control expenses without sacrificing quality.
In addition to raw materials, manufacturing processes require sophisticated machinery and technology. This equipment may demand a considerable capital outlay, particularly for small businesses or startups. Furthermore, operational costs include energy consumption, labor, and maintenance of the production line. These factors contribute to a cumulative cost that can impact pricing strategies in the marketplace.
Moreover, as ALC flowable composites gain popularity, supply chain dynamics may influence costs. Market fluctuations and demand shifts can lead to price variability, complicating financial forecasting. Stakeholders involved in production must remain vigilant, balancing cost efficiency with the retention of high standards.
Performance Limitations
Despite the advantages of ALC flowable composites, they possess performance limitations that may affect their application in certain scenarios. One key concern is their long-term durability. While they are designed to resist wear and degradation, environmental factors can diminish their lifespan. Extreme temperatures, for instance, may compromise the material's integrity over time, necessitating further research to enhance resistance to such conditions.
Another limitation is the mechanical strength of these composites. Although ALC flowable composites offer good workability, they may not possess the same load-bearing capabilities as traditional materials such as concrete or steel. This difference can be crucial in construction projects where structural integrity is paramount. Users must examine load requirements closely to ensure the chosen material aligns with project demands.
Lastly, the curing and setting processes present additional performance challenges. While these processes are generally efficient, incomplete curing or improper setting can lead to flaws in the finished product. This concern emphasizes the need for rigorous quality control measures throughout production and application phases.
Understanding both the cost factors in production and the performance limitations of ALC flowable composites is essential for optimizing their usage in various industries. These considerations guide informed decision-making that balances innovation with practicality.
Comparative Analysis with Traditional Materials
The significance of comparing ALC flowable composites with traditional materials lies in understanding their unique advantages and limitations. This comparative analysis helps professionals in different fields make informed decisions about material selection, which is essential in construction, manufacturing, and other applications. Knowing how these composites stack up against conventional materials can drive innovation and inform future designs, allowing for adaptability in diverse projects.
Contrasting Performance Metrics
Performance metrics are a critical aspect of comparing flowable composites and traditional materials. ALC flowable composites often exhibit enhanced flow characteristics, allowing for easier application in various contexts. The viscosity of flowable composites enables them to fill intricate shapes and gaps better than many traditional materials. In terms of mechanical strength, ALC composites can achieve comparable, if not superior, results when cured properly.
- Tensile strength: Flowable composites can offer tensile strength on par with traditional options, such as concrete or plaster, while maintaining reduced weight.
- Compressive resistance: Tests show that well-formulated ALC composites withstand compressive stress efficiently.
- Durability: Traditional materials typically have weaknesses in certain environments. Flowable composites may resist environmental impacts more effectively, which leads to longer service life.
This contrast in performance underscores the potential of ALC flowable composites to outperform traditional materials in specific scenarios, particularly in modern engineering and construction environments.
Cost-Benefit Evaluation
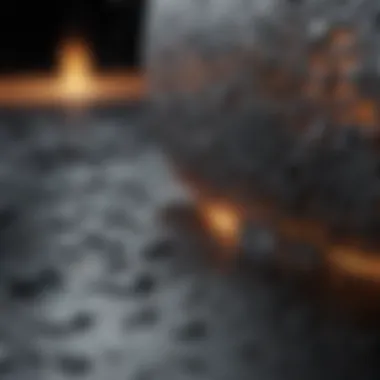
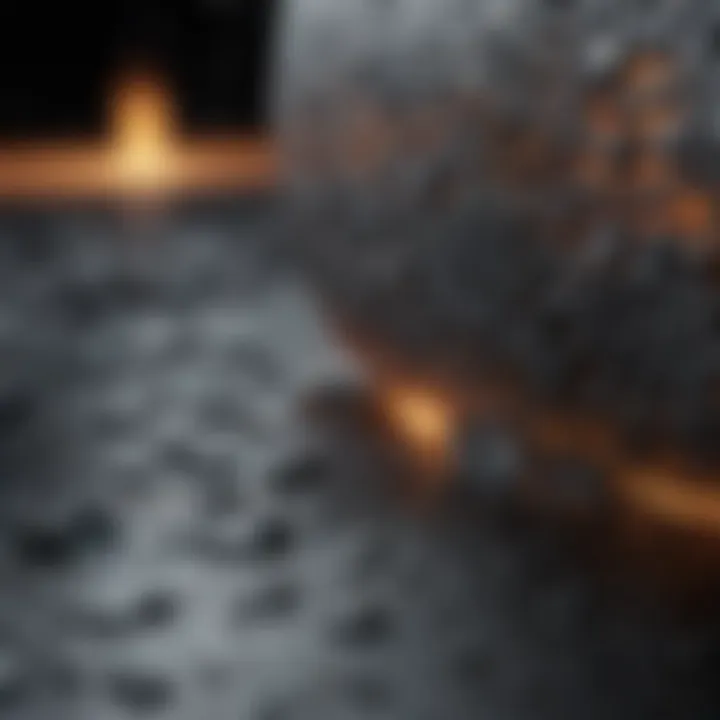
The cost-benefit evaluation helps stakeholders analyze the economic implications of using ALC flowable composites versus traditional materials. While initial costs may be higher for composites due to advanced manufacturing techniques and specialized ingredients, long-term savings can offset these initial investments.
- Initial Costs: ALC flowable composites may require more expensive raw materials and production methods. However, their unique properties can justify the higher upfront expense.
- Labor Costs: The ease of application can significantly reduce labor costs. Professionals can often complete jobs faster, lowering overall project expenses.
- Maintenance Costs: Flowable composites can lead to lower maintenance costs due to their enhanced durability. Less frequent repairs or replacements can save financial resources over time.
Ultimately, the cost-benefit analysis reveals that ALC flowable composites can be more economical in the long run, depending on the specific application and environment of use. Evaluating both short-term and long-term financial impacts allows decision-makers to determine the value of these advanced materials distinctly.
Recent Research and Developments
Recent research and developments in ALC flowable composites are crucial for understanding their potential and adaptability in various domains. The modernization of material science brings about the necessity for continuous innovation and improvement of these composites. As industries evolve, the demand for materials that offer not just strength but also flexibiity and sustainability increases. This section explores two key aspects: innovations in composite materials and future trends in ALC composites.
Innovations in Composite Materials
The field of composite materials has seen significant innovations in recent years. Researchers are focusing on enhancing the mechanical properties of ALC flowable composites through better formulation and processing techniques. New studies indicate that integrating hybrid additives can lead to improved durability and performance.
- Nanomaterials: The inclusion of nanomaterials such as carbon nanotubes has shown promise in improving the tensile strength and thermal stability of the composites. These tiny structures significantly enhance the composites' performance without adding considerable weight.
- Bio-based Materials: There is an increasing interest in bio-based fillers that not only improve the mechanical characteristics but also promote environmental sustainability. The shift toward natural fibers and fillers is a response to global concerns about sustainability and waste reduction.
- Smart Composites: The development of smart composites, which can respond to changes in their environment, is also on the rise. Such materials have applications in structural health monitoring, where they can detect stresses or damages in real time.
"The integration of new technologies into composite materials is not just a trend; it is a necessity for future advancements in engineering."
Future Trends in ALC Composites
Looking towards the future, several trends are likely to shape the landscape of ALC flowable composites. These trends reflect a shift towards sustainability and efficiency in manufacturing processes.
- Sustainability Focus: Environmental concerns will continue to lead researchers toward developing more eco-friendly composite solutions. This includes the usage of recyclable materials and improved waste management techniques during production.
- Lightweight Solutions: As industries aim for weight reduction to enhance efficiency, ALC composites are likely to evolve in design to become lighter. This can significantly impact the automotive and aerospace sectors by optimizing fuel consumption.
- Advanced Testing Methods: The rise of advanced testing techniques will aid in better understanding material behavior under different conditions. This knowledge is essential for ensuring safety and performance in real-world applications.
In summary, ongoing research and developments in ALC flowable composites reveal a dynamic interplay between innovation, sustainability-driven practices, and future trends. The insights gained from this field can lead to profound changes not only in manufacturing and construction but also in everyday applications.
Case Studies and Real-World Applications
The exploration of case studies in ALC flowable composites provides valuable insights into their practical implementations. This section underscores the significance of understanding real-world applications. Analyzing diverse scenarios where ALC flowable composites have been effectively employed enables professionals and researchers to grasp their potential benefits. Additionally, it lays a foundation for future advancements in material science and engineering.
Successful Implementations
Several projects have showcased the effectiveness of ALC flowable composites in various industries. One notable example is its use in the construction sector, particularly in high-rise buildings. In these structures, the lightweight and flexible nature of ALC composites allows for easier handling and application, reducing labor costs significantly.
Moreover, a recent case in urban infrastructure development highlighted the advantages of these materials in repairing and reinforcing existing structures. For instance, a bridge renovation project utilized ALC flowable composites to restore strength and enhance durability without adding excessive weight. The outcome not only improved the bridge’s lifespan but also minimized downtime during repairs.
Other successful applications can be found in the automotive industry. Engineers have implemented ALC composites for components that require both lightweight and robust characteristics, such as insulation and heat shielding parts. These composites have resulted in improved fuel efficiency and overall performance.
Lessons Learned from Failures
Despite the many successes, there are lessons to be gleaned from projects involving ALC flowable composites that did not meet expectations. One significant factor in these failures was the lack of thorough testing before full-scale application. For example, an automotive prototype faced challenges when the composite did not adhere properly during the manufacturing process. This incident highlighted the necessity of rigorous quality control measures.
Another lesson arose from the construction field, where some structures exhibited premature wear due to inadequate curing processes. Poor environmental conditions during the curing phase led to compromised durability. This reinforces the importance of strict adherence to guidelines regarding application and curing, ensuring that environmental variables are controlled.
Ending and Future Directions
The discussion surrounding ALC flowable composites culminates in recognizing their significance in contemporary material science and engineering. This section delineates the importance of reflecting on the findings and potential future pathways. Engaging with the topic of flowable composites encourages a deeper understanding of material capabilities and enhancements brought forth by ongoing research.
ALC flowable composites offer unique advantages that may improve efficiency in construction and manufacturing processes. They are versatile, durable, and, most importantly, adaptable to various applications, making them essential in advancing modern infrastructure. The implications of these materials extend beyond mere functionality; they embody a shift in how industries approach construction challenges. Their adaptability allows for innovation in design and application methods, contributing to sustainability efforts and cost reduction.
"The future of material science lies in understanding and harnessing the potential of advanced composites."
Summarizing Key Takeaways
In this article, several critical points regarding ALC flowable composites were explored. The following key takeaways stand out:
- Applications Across Industries: From construction to aerospace, ALC flowable composites demonstrate impressive versatility.
- Physical and Chemical Properties: Understanding their viscosity, adhesion, and durability explains their increasing adoption.
- Challenges to Address: Cost factors and performance limitations present important considerations for future development.
These elements create a compelling case for continued interest in ALC flowable composites and their role in future innovations.
Implications for Material Science
The implications of ALC flowable composites for material science are profound. The ongoing study of these materials can open new avenues for innovation and improved practices in several fields. Key implications include:
- Enhanced Performance Metrics: Advancements in composite materials can drive performance improvements in various applications.
- Sustainability Focus: The adaptability of these materials aligns with the growing emphasis on sustainable practices within manufacturing and construction.
- Market Growth Potential: As industries recognize the benefits, the demand for flowable composites is likely to rise, influencing material science development.
As material science advances, ALC flowable composites will likely play a crucial role in shaping the future of various industries.
Call for Further Research
While the analysis presents a comprehensive overview of ALC flowable composites, there remains a significant gap in understanding the full scope of their potential. Therefore, further research is imperative. Areas for future investigation include:
- Expansion of Applications: Exploring new industries or contexts of usage can uncover additional benefits and efficiencies.
- Long-Term Performance Studies: Rigorous testing concerning the longevity and durability under diverse conditions can validate their efficacy.
- Cost Reduction Strategies: Investigating ways to lower production costs while maintaining quality will enhance their marketability.
These focus areas can guide future researchers and industry professionals toward maximizing the benefits of ALC flowable composites.