Attributes and Applications of 7075 Aluminum Alloy
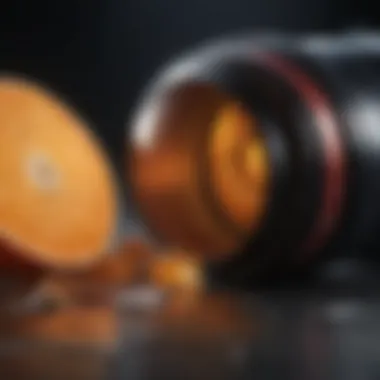
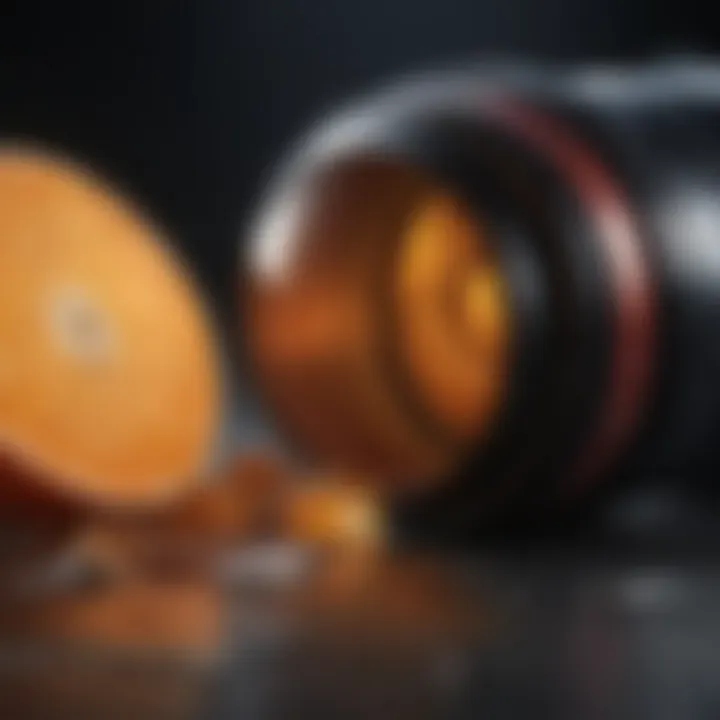
Intro
Understanding materials is fundamental in fields such as engineering, aviation, and manufacturing. Among the plethora of materials used today, 7075 aluminum alloy stands out due to its striking combination of strength and lightweight characteristics. Known to be one of the most robust alloys in the aluminum family, 7075 material plays a critical role in demanding applications, including aerospace frameworks and high-stress components.
In this exploration, we will unravel the essence of 7075, digging into its composition and mechanical properties while also scrutinizing its heat treatment processes. This alloy is not just strong; it’s versatile too, finding its way into various industries. By the end of this article, readers will have a lucid understanding of the alloy's advantages, limitations, and its position in contemporary engineering practices.
Overview of Research Topic
Brief Background and Context
7075 alloy consists primarily of zinc as the dominant alloying element, yielding tremendous mechanical properties. When you look at the components that make up 7075, it’s like putting together a complex recipe where each ingredient plays its part to perfection; zinc, magnesium, copper, and chromium all contribute to the alloy's unique attributes.
The alloy was first developed during World War II for aircraft structures, taking advantage of its lightweight yet robust nature. Over time, it has evolved to be utilized in various fields beyond aviation, showcasing its adaptability. This evolution highlights not only the material's longevity but also its continuous relevance in emerging technologies.
Importance in Current Scientific Landscape
In the modern scientific landscape, developing lightweight materials has become increasingly essential, especially with the push towards energy efficiency and sustainability. 7075 aluminum is often hailed for its potential to reduce overall weight in structures without forfeiting strength.
One of the cruxes of 7075's utility is how it aligns with current engineering trends focusing on resource management and performance optimization. Industries from automotive to marine are tapping into this versatile material, aiming to fulfill both regulatory demands and consumer expectations for durability and efficiency.
"7075 aluminum alloy is not merely a component; it is a game-changer in engineering and manufacturing, effectively merging strength with lightweight properties."
Methodology
Research Design and Approach
The exploration of 7075 material employs a multi-faceted research design incorporating both qualitative and quantitative analyses. By examining existing literature and case studies, insight can be gleaned into the alloy’s performance in real-world applications as well as its microstructural attributes.
Data Collection Techniques
Data was gathered through various techniques, including:
- Literature reviews of scholarly articles and technical papers accessible through databases like JSTOR and ScienceDirect.
- Interviews with experts in metallurgy and materials science.
- Field studies and case evaluations of projects utilizing 7075 alloy to measure performance outcomes.
Through these data collection techniques, a comprehensive understanding of 7075's applications, advantages, and drawbacks can be assembled, ensuring that our examination is rooted in factual evidence and relevant experiences.
Preamble to Material
7075 material is a particular aluminum alloy that stands out in various applications due to its notable properties. Recognized primarily for its exceptional strength-to-weight ratio, it captures interest across multiple industries. Understanding 7075's attributes and applications is not just about recognizing a material; it’s about appreciating its role in pushing engineering and design boundaries.
Historical Context
The origins of 7075 alloy date back to World War II. At that time, the demand for lightweight yet strong materials surged as military aircraft required components that could endure extreme conditions without adding excessive weight. 7075 material was developed by the Aluminum Company of America, primarily using zinc as the main alloying element. It swiftly gained traction in the aerospace sector, establishing a reputation for reliability and performance under stress. An interesting anecdote involves its use in the construction of the iconic Boeing B-17 Flying Fortress, showcasing how necessity drove innovation just as much as experimentation and research.
Fast forward several decades, and the historical significance of 7075 alloy is still relevant, as it adapts and thrives in new applications. The ongoing demand for stronger materials in airplane fuselages, high-performance automotive parts, and other critical infrastructures continues to make 7075 a key player in technological advancement.
Current Relevance
Today, 7075 material is more critical than ever. In a world where lighter and stronger materials are essential for innovation, its relevance spans various fields. From aerospace engineering to sports equipment manufacturing, its qualities are sought after. Companies like Boeing and military manufacturers still rely on 7075 alloy for components where weight reduction can significantly enhance performance.
In addition, its properties are not limited to high-stress situations. The versatility of 7075 means it’s also being explored in industries not traditionally associated with aerospace, like automotive and consumer products. If we look closely, the advent of electric vehicles has opened up new opportunities for 7075 to shine. As manufacturers aim for increased efficiency and reduced weight, this alloy becomes even more appealing.
"7075’s adaptability makes it a favored choice, not only in aerospace but also beyond, indicating its broad potential to lead innovation."
Simple yet striking, the legacy of 7075 is visible not just in its historical applications but in its vibrant growth trajectory. By understanding both its past and present, engineers and researchers can look forward to how 7075 material can be leveraged even more effectively in the future.
Chemical Composition of
Understanding the chemical composition of 7075 aluminum alloy is crucial because it directly influences its properties and applications. This alloy is widely used due to its impressive strength-to-weight ratio, making it particularly attractive for industries where performance and durability are paramount. The specific elements that make up 7075 dictate not only its mechanical behavior but also its corrosion resistance and workability. Knowingly, insights into these components lay a solid foundation for grasping the benefits and limitations this material presents across various fields.
Base Elements
At the core of 7075's chemical makeup are its base elements, which include aluminum, zinc, magnesium, and copper. Each of these contributes uniquely to the alloy's overall performance:
- Aluminum (Al): The principal component, which provides the alloy with its lightweight characteristics.
- Zinc (Zn): This is the prime alloying element in 7075, significantly enhancing strength. Zinc boosts the hardness level considerably, making the alloy suitable for high-stress applications.
- Magnesium (Mg): Magnesium complements zinc by improving machinability and corrosion resistance. Its presence helps stabilize the structure during heat treatment.
- Copper (Cu): Copper adds strength and improves resistance to stress corrosion, although it can make the alloy less resistant to pitting corrosion, especially in marine environments.
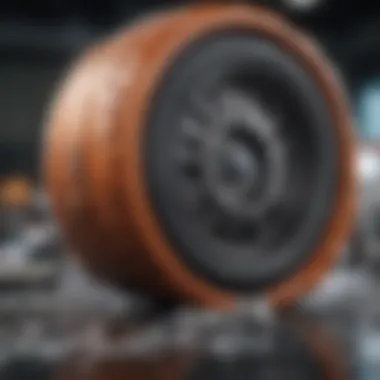
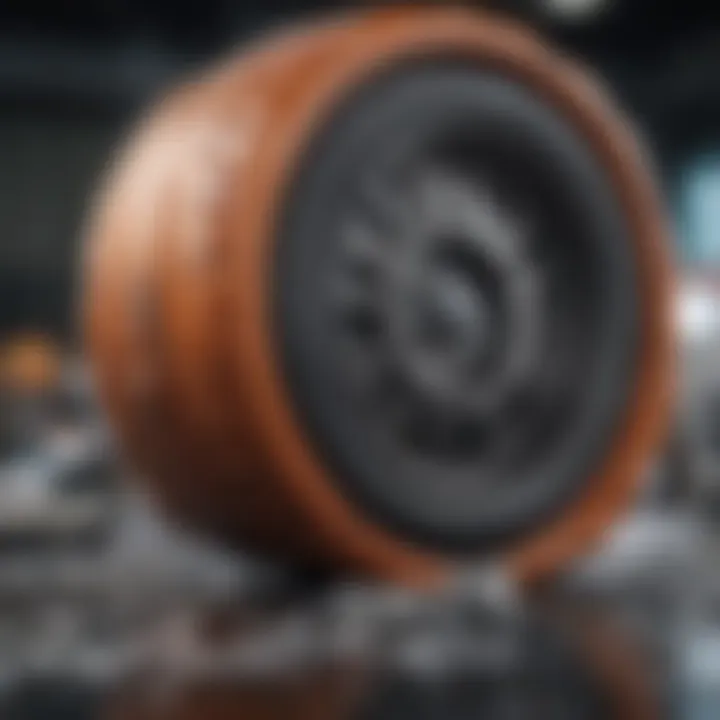
Together, these base elements develop an alloy that enjoys robust application in aerospace, automotive, and other demanding industries.
Trace Elements and Impurities
In addition to the base elements, 7075 also contains trace elements like chromium, silicon, and iron. While typically present in small quantities, these can influence performance:
- Chromium (Cr): Known for enhancing stress corrosion resistance, chromium also improves the alloy’s strength.
- Silicon (Si): Though present in minor amounts, silicon helps with casting and shaping while improving fluidity in molten form during production.
- Iron (Fe): While ideally kept to a minimum in aluminum alloys for quality control, small amounts can still find their way in. Iron can increase strength slightly but may also lead to issues like lower ductility.
In the case of impurities, the 7075 alloy is designed with tight tolerances, ensuring that undesirable elements don’t compromise its performance. Manufacturers actively monitor the contents to minimize the presence of elements like lead or bismuth, which can adversely affect its properties.
"The efficacy of an alloy often hinges on the balance of its chemical constituents, making precise composition analysis a cornerstone of material science."
In summary, diving into the chemical composition of 7075 not only unearths the secrets behind its remarkable capabilities but also prepares one to tackle its potential drawbacks effectively. A solid understanding shapes informed decisions about its use in various environments.
Mechanical Properties
Understanding the mechanical properties of 7075 material is pivotal, especially for those involved in fields like aerospace, automotive, and sports equipment manufacturing. The mechanical attributes influence the performance and durability of the material in real-world applications. When designing components, engineers must consider these properties to ensure they meet safety and functionality standards. After all, using the right material with appropriate mechanical properties can make or break a project.
Tensile Strength
Tensile strength is one of the most critical mechanical properties of any material. For 7075 aluminum alloy, this property is particularly impressive. It signifies the maximum amount of tensile or pulling stress that a material can withstand before failure. The tensile strength of 7075 can reach values around 570 MPa, making it one of the strongest aluminum alloys available. This capability allows it to endure high stresses during operation, especially in the aerospace and automotive sectors where safety is paramount.
In practical terms, when engineers design an aircraft or an automotive component, they ensure that the tensile strength of 7075 can handle operational loads without deformation or breakage. Thus, its high tensile strength is not just a number; it directly correlates to the reliability of the machinery or structure built using the material.
Yield Strength
Next up is yield strength, which although somewhat related to tensile strength, is critical in determining how a material behaves under stress. Yield strength reflects the stress at which a material begins to deform plastically. For 7075, yield strength typically hovers around 500 MPa, which means that once this level is exceeded, the material won’t return to its original shape, leading to permanent deformation.
This aspect is crucial in applications where components must maintain their shape under load. In aerospace, for example, parts must endure not just the weight of the aircraft but also the stresses of turbulence and maneuvers. The yield strength of 7075 enables engineers to create shapes and structures that can absorb shocks without yielding, which is invaluable for safety and performance.
Fatigue Resistance
Lastly, fatigue resistance stands out as a significant property of 7075 aluminum. Fatigue refers to the weakening of a material caused by repeatedly applied loads. With cyclic loading, materials can gradually lose their integrity, leading to unexpected failures. 7075 exhibits excellent fatigue strength, which means it can withstand numerous stress cycles without cracking or failing over time.
This property is why 7075 finds routine use in components subjected to cyclical loads, like airplane wing structures or high-performance sports equipment. A component's ability to resist fatigue ensures longevity and reliability, practical selling points that resonate well in competitive markets.
Key Takeaway: The mechanical properties of 7075 material, notably its tensile strength, yield strength, and fatigue resistance, underline its importance in various demanding applications. These attributes not only enhance safety but also contribute significantly to performance, making 7075 a preferred choice among engineers and designers.
Heat Treatment Processes
Heat treatment processes are crucial for maximizing the performance and characteristics of 7075 material. Particularly in alloy metallurgy, these processes significantly enhance the mechanical properties, allowing this aluminum alloy to achieve exceptional strength and durability. The treatment techniques not only improve resistance to stress and fatigue but also allow for more versatile applications in different industries.
Solution Heat Treatment
Solution heat treatment involves heating the 7075 aluminum alloy to a specific temperature, typically around 480 to 520 degrees Celsius. This temperature range varies depending on specific alloy compositions. The purpose of this step is to dissolve soluble alloying elements such as zinc and magnesium into a solid solution. As a result, the microstructure of the metal becomes uniform, which is crucial for achieving the desired mechanical properties.
After reaching the desired temperature, the alloy is rapidly quenched, often in water or oil, to retain the soluted elements in a supersaturated condition. This sudden drop in temperature locks in the configuration of the alloy structure, setting the stage for further treatments such as aging. It's a way to get the metal hot enough to loosen up its atoms and then rapidly cool it to keep them from going back to a more disordered form.
Aging Process
The aging process, sometimes referred to as precipitation hardening, is essential for enhancing the strength of 7075 material. After solution heat treatment, the alloy is held at a lower temperature, usually between 120 and 200 degrees Celsius, for an extended period. During this time, the previously dissolved solute atoms precipitate out, forming fine particles throughout the metal's matrix.
This precipitation serves multiple purposes. Firstly, it hinders the motion of dislocations within the microstructure, which enhances the material's hardness and strength. Secondly, it helps to relieve some of the residual stresses imparted during the cooling process. There's a certain finesse in timing and temperature during aging; if done right, it can lead to a significant boost in mechanical performance. But if the conditions aren't ideal, it might result in subpar material characteristics.
Impact of Heat Treatment on Properties
Heat treatment dramatically influences the properties of 7075 material, particularly its tensile and yield strength. The careful control of heating and cooling rates, as well as the specific steps undertaken in the heat treatment process, contribute to the favorable attributes of this alloy. Here are several key impacts to consider:
- Increased Strength: Post-treatment, 7075 exhibits spectacular strength-to-weight ratios, making it a favorite across aerospace and automotive industries.
- Enhanced Durability: The heat treatment processes improve resistance to wear and tear, adding to the longevity of structural components made from 7075.
- Fine-Tuned Flexibility: The ability to manipulate heat treatment allows engineers to tailor the alloy’s properties for specific applications, sometimes requiring a delicate balance between strength and malleability.
In summary, the heat treatment processes applied to 7075 material directly contribute to its standing as one of the strongest aluminum alloys. Understanding these processes helps in making informed decisions about its suitability for different applications.
By focusing on these thermal processes, engineers not only ensure the performance of the materials but also their reliability over time, which is vital for high-stakes applications.
Applications of Material
The application of 7075 material spans a wide range of industries, making it a fundamental component in modern engineering and manufacturing. The significance of its strength and lightweight nature cannot be overstated. In sectors where performance and safety are critical, such as aerospace, automotive, and sporting goods, 7075 stands out as a favored choice among engineers and designers. Its unique attributes, derived from its chemical makeup and treatment processes, create opportunities for innovative designs and enhance product efficacy.
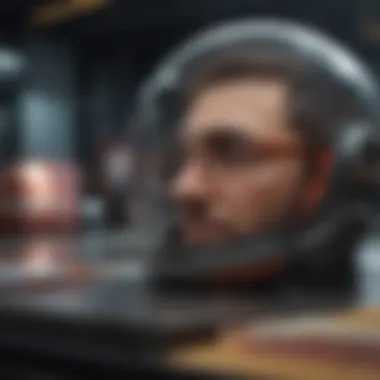
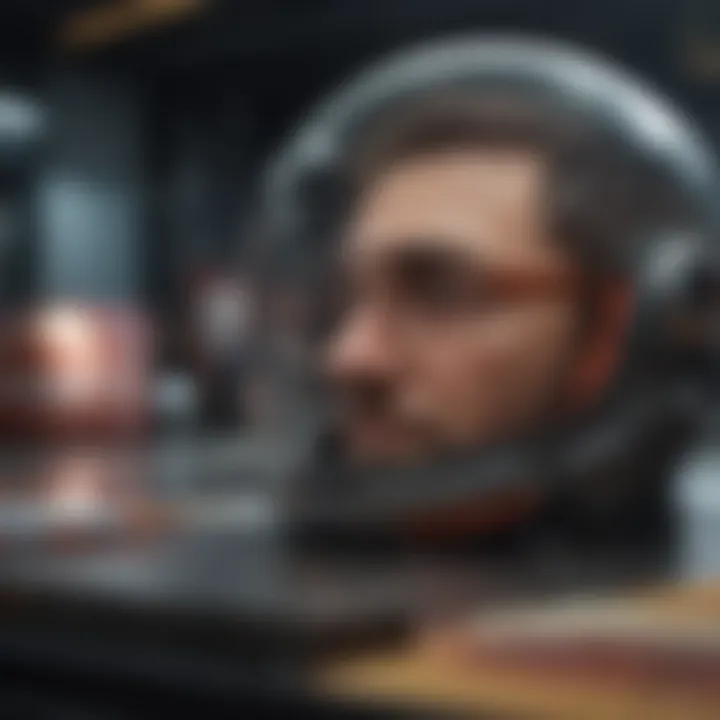
With the rise of technology and performance demands, understanding where and how to optimally apply 7075 material is crucial. This section highlights various pivotal applications that underscore its indispensable role in the development of cutting-edge products, catering to the needs of both consumer and industry standards.
Aerospace Engineering
In aerospace engineering, the stakes are incredibly high. Here, performance, safety, and weight are interlinked factors that significantly affect aircraft and spacecraft designs. 7075 aluminum alloy is often the go-to option, due to its outstanding strength-to-weight ratio. The material is often found in critical components such as aircraft wings, fuselage skins, and high-stress parts like landing gears.
Some key reasons for its adoption in aerospace include:
- High specific strength: This allows for reduced weight without compromising structural integrity.
- Fatigue resistance: Essential for parts exposed to cyclical loads, such as in flight.
- Good corrosion resistance: When treated appropriately, 7075 can withstand harsh atmospheric conditions.
"In the realm of aviation, every ounce matters. The combination of light weight and robustness in 7075 can be the difference between a successful mission and a failure."
Automotive Industry
In the automotive sector, there's a never-ending pursuit of efficiency and performance. Manufacturers are looking at 7075 aluminum as a material that can deliver both safety and reduced energy consumption. The automotive industry is using this alloy for various components like chassis, suspension parts, and even engine blocks. This ensures that vehicles not only weigh less—contributing to better fuel efficiency—but are also tough enough to withstand the rigors of driving.
Advantages of using in automotive applications include:
- Enhancement of fuel efficiency: Lowering vehicle weight is a direct contributor to improved fuel economy.
- Durability: The alloy’s ability to endure high stress makes it ideal for performance vehicles.
- Design freedom: Its workability allows for intricate designs that shape modern vehicle aesthetics and functionality.
Sports Equipment Manufacturing
In the sporting goods industry, where performance can make or break a career, 7075 aluminum alloy has carved a niche for itself. Equipment such as bicycle frames, golf clubs, and high-performance sports gear utilize this alloy due to its remarkable strength and low density.
Key benefits of in sports equipment include:
- Lightweight Characteristics: Athletes benefit from lighter gear that does not sacrifice performance.
- Impact resistance: Items can endure rigorous activities, such as cycling or golfing, which often involve significant stress.
- Customizability: Manufacturers are able to mold the metal into complex shapes that enhance performance features.
Understanding these applications is just the tip of the iceberg when it comes to appreciating the versatility and importance of 7075 material across different sectors. As industries evolve and new technologies emerge, the future application landscape for 7075 aluminum alloy is wide open, holding promise for innovation and advancement.
Advantages of Material
The advantages of 7075 material are what place it at the forefront of engineering solutions. Its unique characteristics make it a preferred choice in several high-performance applications. By understanding these advantages, professionals can better appreciate its role in various industries, from aerospace to sports equipment manufacturing.
Strength-to-Weight Ratio
7075 aluminum alloy boasts an exceptional strength-to-weight ratio that makes it highly desirable in applications where minimizing weight is crucial while still maintaining robust structural integrity. The alloy’s tensile strength often outshines steel, which is quite remarkable, considering it’s much lighter. This trait becomes particularly significant in industries like aerospace, where every ounce counts. For instance, the 7075-T6 variant offers a tensile strength of about 570 MPa, making it ideal for aircraft components that require both strength and reduced weight.
The combination of strength and lightness provides engineers the freedom to innovate and design more efficient structures without the heavy burden of excess weight.
Corrosion Resistance
One of the often underrated but significant benefits of 7075 material is its corrosion resistance, which stems from the alloy’s specific composition. While it can be prone to corrosion compared to other aluminum alloys, proper metallurgical treatment significantly enhances its resistance. For example, applying a protective coating or anodizing can safeguard against environmental factors like humidity and saltwater, which can be damaging in transportation settings.
In marine applications or even in outdoor structures, where exposure to elements is constant, ensuring that 7075 material is treated effectively can prolong its lifespan considerably. This resistance not only enhances reliability but also reduces maintenance costs over time, making 7075 a wise choice for long-term applications.
Versatility in Forming
Another crucial advantage of 7075 material is its versatility in forming processes. This alloy can be easily machined, welded (with some caution), and formed into various shapes, accommodating different manufacturing techniques. The ability to fabricate complex geometries from 7075 allows for its use in a broad spectrum of applications such as automotive frames, aerospace structures, and sporting goods.
This flexibility in design and manufacturing contributes to its growing popularity, as engineers can tailor products to meet specific needs without compromising on the material’s inherent properties.
The adaptability of 7075 aluminum alloy is not just a perk; it’s a cornerstone of modern engineering, enabling innovations that were previously thought impractical.
In summary, the advantages of 7075 material—its striking strength-to-weight ratio, enhanced corrosion resistance when treated, and versatility in forming—illustrate why it has become a stalwart in the engineering sector. These attributes provide tangible benefits that go beyond individual applications, steering advancements in design and manufacturing across multiple domains.
Limitations of Material
While 7075 material boasts significant strengths, it’s equally crucial to acknowledge its limitations. Understanding these drawbacks allows for informed decision-making in contexts where this alloy will be applied. Misjudging these limitations can undermine project success, particularly in high-stakes industries such as aerospace or automotive. Developers, engineers, and researchers must be mindful of these constraints, ensuring optimal material selection.
Weldability Concerns
Weldability is a common hurdle when using 7075 aluminum alloy. High zinc content contributes to its strength, but also creates challenges in joining processes. The welds produced can lead to considerable stress, making the material susceptible to cracking.
The heat-affected zone around the welds often experiences a reduction in mechanical properties. Welded joints may not meet the same strength criteria as the base material. It’s like trying to patch a tire with materials unfit for the job; it might hold for a bit, but it’s bound to fail under pressure.
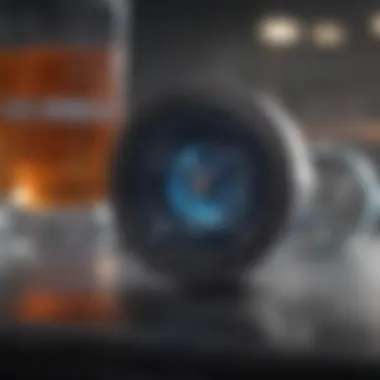
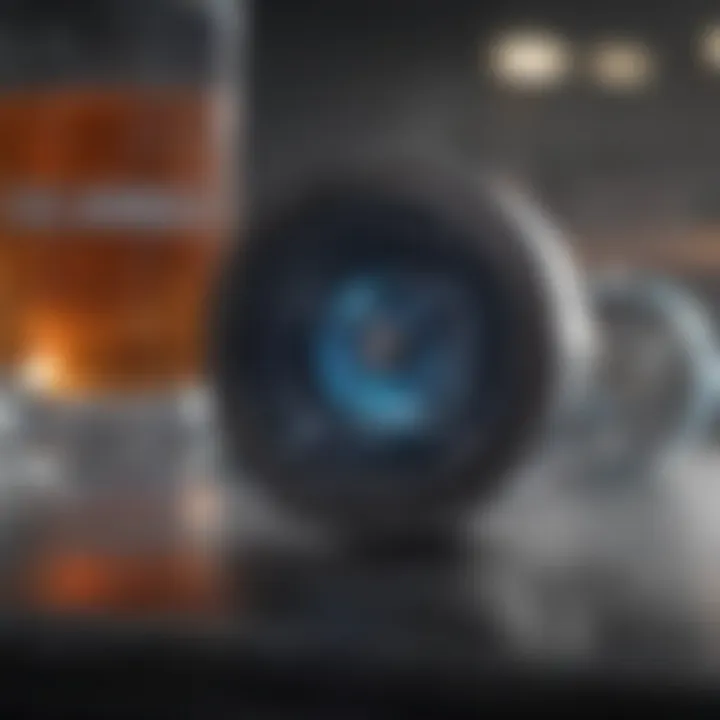
To mitigate these issues, preheating prior to welding and using filler materials designed for 7075 can help—but these are not foolproof solutions. Each project demands specific considerations.
Cost Considerations
7075 aluminum alloy typically comes with a heftier price tag compared to its peers, such as 6061. This increased cost is attributed to several factors, including the complex manufacturing processes and the premium quality desired in commercial applications. For many small businesses or startups, opting for 7075 may result in breaking the bank, especially when the application doesn't absolutely demand such high-performance material.
Even though the advantages can justify the expense in markets focused on high durability and strength, one must weigh whether the additional investment aligns with project budgets and expected performance outcomes.
In summary, while 7075 material is lauded for its exceptional properties, it’s imperative to be cognizant of its limitations. Weldability issues can pose significant challenges when fabricating components, and the higher costs associated with the alloy might not always deliver returns on investment. An informed choice is crucial, ensuring that the selection of materials fits the specific engineering and economic requirements.
Innovations in Processing Techniques
The significance of innovations in processing techniques cannot be overstated when it comes to 7075 aluminum alloy. As industry demands for stronger, lighter, and more durable materials continue to rise, the methods employed in the production and processing of these materials must adapt accordingly. With 7075 being one of the most sought-after aluminum alloys due to its remarkable mechanical properties, advancements in production and machining can enhance its application viability across a spectrum of industries.
Recent Advances in Alloy Production
Innovations in alloy production have resulted in the development of improved methods that optimize the initial characteristics of 7075 material. Techniques such as high-speed casting, powder metallurgy, and rapid solidification are gaining attention. These methods ensure a more uniform microstructure, which can significantly impact the alloy's performance.
- High-Speed Casting: This technique allows for faster cooling rates during the solidification process, leading to finer grain structures. The outcome is a material that displays enhanced tensile properties and overall strength.
- Powder Metallurgy: This process involves compacting and sintering alloy powders, offering precise control over chemical composition and microstructure. This makes it possible to create tailored alloys that meet specific performance criteria, particularly beneficial in specialized applications.
- Rapid Solidification: By employing rapid cooling methods, materials exhibit better mechanical properties. This approach reduces the formation of coarse grains that can impair strength.
Advancements in alloy production are not just about meeting current demands; they pave the way for the future of material science by enabling innovators to design alloys for specific use cases.
Improved Machining Methods
As 7075 material finds its place in more high-performance applications, efficient machining methods become crucial. Traditional machining techniques can be slow and often lead to material wastage. However, the advent of advanced techniques has transformed this landscape significantly.
New methods such as ultrasonic machining and laser machining allow for precise cuts with minimal waste. The benefits include:
- Reduced Tool Wear: Tools can last longer when they operate with higher precision and less friction.
- Enhanced Accuracy: Advanced machining techniques can achieve tighter tolerances, which is crucial in applications like aerospace.
- Faster Production Rates: Time efficiency improves significantly, resulting in reduced costs of production.
In terms of implementation, integrating these methods can require new skill sets and equipment, but the investment often pays off in the form of increased efficiency and performance of the final products. As we continue to explore 7075 material applications, the importance of innovating processing techniques remains a cornerstone for reinforcing this alloy’s position in the marketplace.
Future Trends in Material Usage
As industries lean into more sustainable practices and innovative designs, the future of 7075 material is looking increasingly promising. This aluminum alloy presents unique advantages that align well with evolving market demands. In this section, we'll explore key aspects of its anticipated uses, shedding light on the benefits and considerations stemming from such trends.
Market Demand Projections
The demand for high-performance materials like 7075 aluminum alloy is set to rise. Several factors feed into this projected growth:
- Increased Aerospace Production: With companies such as Boeing and Airbus ramping up aircraft production to meet global travel demand, 7075 is ideal due to its excellent strength-to-weight ratio. This makes it a preferred choice for structure and components within aircraft.
- Automotive Lightweighting Efforts: The automotive sector is pushing hard towards lightweight designs to enhance fuel efficiency. Electric vehicles, in particular, require materials that minimize weight while maximizing durability. The trend looks like it will favor 7075 as manufacturers seek to develop cars with lower emissions.
- Growing Recreational Markets: As more people engage in outdoor activities and sports, high-end sports gear made from 7075, such as bike frames and climbing gear, is gaining traction. Performance attributes are intertwined with consumer preferences for lightweight and durable goods.
In sum, the market's trajectory suggests a steady climb in the uptake of 7075 material across multiple industries, making it essential for manufacturers to stay ahead of the curve.
Emerging Applications in Engineering
The versatility of 7075 aluminum alloy allows it to penetrate several emerging engineering applications. These applications are particularly important as advancements unfold:
- Robotics and Automation: Engineers are incorporating 7075 into robotic components where strength and precision are paramount. Its mechanical properties can enhance the durability of robotic arms and drones, ensuring they can withstand rigorous conditions.
- Medical Devices: Innovations in medical technology are requiring materials that are both lightweight and strong. In applications like surgical instruments and prosthetics, 7075 offers biocompatibility along with the structural integrity needed for safety and effectiveness.
- Marine Engineering: As marine technology evolves, the demand for lightweight and corrosion-resistant materials is rising. 7075's resistance to saltwater corrosion makes it a compelling choice in the design of frames for yachts and submarines.
In essence, as different sectors focus on innovation and sustainability, the role of 7075 material is expected to become increasingly significant. Its attribute of strength combined with its lightweight nature opens the floodgates for numerous advanced applications across the engineering landscape.
Comparative Analysis with Other Alloys
In the world of materials science, particularly in the realm of aluminum alloys, the comparative analysis is invaluable. It allows engineers, manufacturers, and researchers to evaluate the strengths and weaknesses of various materials against one another. This not only aids in material selection for specific applications but also enhances understanding of how different alloys perform under varying conditions. The significance of comparing 7075 aluminum alloy against others like 6061 lies in its varied applications, performance metrics, and overall suitability for high-stress environments.
Comparing with
7075 and 6061 are two of the most commonly used aluminum alloys, each heralded for their unique properties.
- 7075 Aluminum Alloy: Known primarily for its exceptional strength-to-weight ratio, 7075 is often the material of choice in applications that require high stress yield and fatigue resistance. However, it is worth noting that its welding properties are not as robust as those of 6061, which can limit its use in certain assembly methods.
- 6061 Aluminum Alloy: This alloy is celebrated for its versatility and easier workability. It exhibits a good balance of strength, corrosion resistance, and machinability, making it suitable for a variety of applications, from structural components to marine contexts.
In comparison, 7075 often outshines 6061 in terms of strength, particularly in aircraft and military applications. However, the latter shines where ductility and weldability are crucial. Thus, if you're designing a lightweight aircraft, 7075 may be your go-to. But if you need a sturdy framework that can be welded easily, 6061 holds its own.
7075 characteristics:
- Tensile strength: High
- Weight: Light
- Weldability: Limited
6061 characteristics:
- Tensile strength: Moderate
- Weight: Light
- Weldability: Excellent